Share a day in the life of a Devon withy pot maker with a mission to keep this traditional craft alive
Fifth-generation withy crab pot maker Dave French has dedicated the last 40-plus years of his life to the craft.
His exposure to the craft dates back even further back, with his earliest recollections as a young boy, aged perhaps four, being of watching his grandfather make and mend pots in the back garden. He has inherited the craft from his mother’s side of the family, which was one of the oldest fishing families in East Devon – the Mears.
A typical day in Dave’s life is hard to pinpoint, as the processes and procedures of pot- making stretch throughout the year. The main reason for this extended timeline is the way in which the willow is harvested.
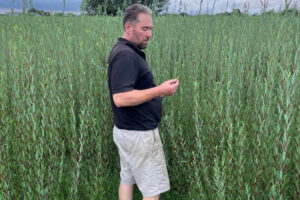
On the Somerset farm where Dave’s willow is grown, the fields are monitored throughout the year. Before harvest, a final examination determines the most suitable batch and rules out issues such as a field being too wet to cut.
Willow is at its best when harvested in the winter – more specifically, during the dormant season. Dave gets his willow from the Musgrove family and their farm in Somerset. The relationship is well-established, with Dave having worked with the Musgroves for many years – as did previous generations of his family.
There are many different varieties of willow, but only very few are suitable for making crab pots. The willow Dave uses is a variety known as black maul.
Dave finds black maul to be the most reliable for making pots as it doesn’t snap easily when it is bent into place, and is overall very sturdy. It is supplied in ‘bundles’ and ‘half bundles’, and Dave needs to work out how much willow he requires for the upcoming year.
He’ll take into account any festivals, local shows and community events, as well as supplying pots to working fishermen, decorative pieces for seafood restaurants and other possible buyers. Displaying his craft at events such as the Plymouth Seafood Festival, Sidmouth Seafood Festival and local heritage craft events sparks a lot of interest, and potential buyers, amongst the public.
It’s vital that Dave calculates the amount accurately, because he cannot risk underbuying for the year ahead. On average, he makes around 57 pots a year.
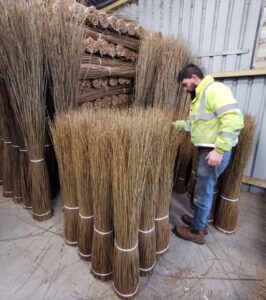
Storage conditions for willow are critical. For example, if the willow becomes wet during storage it can promote mildew, causing the willow to rot. This also applies when travelling back home with the willow from Somerset – the weather must be dry.
When Dave isn’t displaying his craft at shows and events, he typically works on his pots at home, in the back garden, like his grandfather did when he was a young boy. Working pots are always made from freshly cut willow.
When willow is dried and stored properly, it lasts a long time. To make dried willow ready for events, Dave soaks a bundle of 9ft and 4ft willow for between one and two weeks. Timing is critical, and a rough guideline of one day per foot of willow is used to estimate how long each rod of willow needs to be soaked. In his garden, Dave has a 10ft cattle trough, in which enough willow can be soaked to make about three crab pots.
During events, Dave’s withy pot-making displays are typically conducted outside. However, sunshine dries out the willow quickly, even on a warm winter’s day. To counteract this, he brings plenty of water to the events and keeps the willow damp and sheltered from the sun. A handy tactic he uses is wrapping the rods in a wet blanket to preserve moisture. Otherwise, he says, ‘they will get to the point of being so dry they almost turn brittle’.
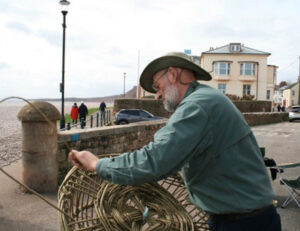
Fifth-generation withy pot maker Dave French promotes the craft not only on social media but also at shows around the South West
in order to keep it in the public eye. Being the last generation of his family to practise the craft, he hopes that by passing his skills on to his friend Sarah Ready, he can help to secure it for the future.
Due to his long experience, Dave can easily identify the first indicators that willow is drying out – ‘you can feel the tips of the willow change’. He uses two different lengths of willow when binding pots. The 4ft rods dry out much more quickly than the 9ft ones. “They’re very thin in comparison and are mainly used as the binders when making pots,” he said.
Dave’s routine of making crab pots has developed into something much bigger over the past two years, since meeting his Queen Elizabeth Scholarship Trust apprentice Sarah Ready.
The first generation of fishermen in her family, Sarah is now also the first generation to make crab pots. For the past two years, she has worked alongside Dave in an effort to revive the critically endangered craft, and they post their work and other updates on their website: traditionallobsterpots.co.uk
As he will be the last generation in his family to make withy pots, Dave is happy to be passing the craft, which he holds very close to his heart, to Sarah.
“She has a dogged determination to succeed,” he said. Sarah’s introduction to the craft is timely, as over the last few years handmade willow pots have been put on the Heritage Crafts Association’s ‘red list’ of critically endangered crafts.
So a day in the life of Dave French goes beyond the craft of making withy pots – it also involves Dave and Sarah’s fight to keep the craft alive.
This story was taken from the latest issue of Fishing News. For more up-to-date and in-depth reports on the UK and Irish commercial fishing sector, subscribe to Fishing News here or buy the latest single issue for just £3.30 here.
Sign up to Fishing News’ FREE e-newsletter here.