Aalskere is, without question, one of the most advanced whitefish vessels to join the Scottish fleet, reports David Linkie
The high level of specification of the new Aalskere reflects the depth of thinking that Orkney skipper Iain Harcus put into a project that was more than four years in the planning and build.
Standout features on Aalskere K 373 include:
- Two customised catch-handling systems
- Two sets of fishroom scales and labelling machines
- Capability to make over 30t of flake and slush ice per 24 hours
- Deckhead and underfloor chilling in 2,500+-box fishroom
- Five single/twin-rig trawls available to shoot away
- Bow and stern thrusters
- 16 bunks
- Two multibeam sonars
- Quad-view video wall
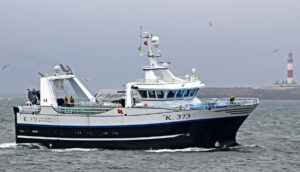
The 35.25m stern trawler Aalskere incorporates a number of significant firsts designed to maximise catch quality.
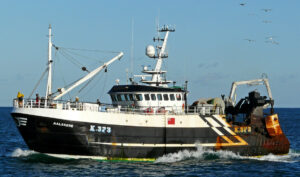
The 33.9m Aalskere was built in Poland in 1997 as Vandal LK 337, before being bought by skipper Iain Harcus 19 years ago.
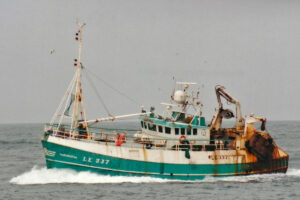
kipper Iain Harcus’ first Aalskere, after being renamed Maranatha by Shetland skipper Angus Cumming.
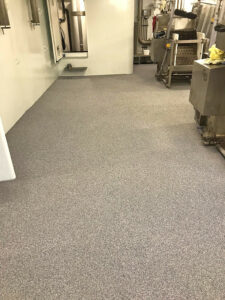
Degafloor hardwearing non-slip resins were applied to the catch-handling and trawl decks by Fraserburgh specialist PBP Services.
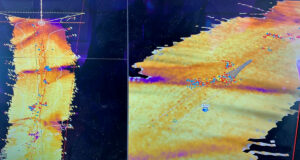
SeapiX 3D hardness mapping showing fish on edges of clean ground. Each dot shows individual fish biomass.
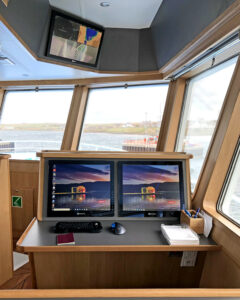
Computer and e-log reporting facilities are provided in a desk area on the starboard side of the wheelhouse.
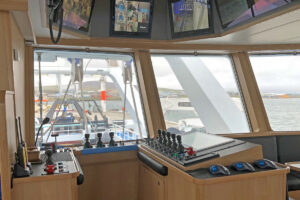
The central fishing console.
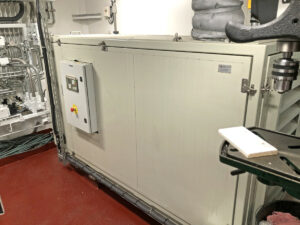
An air-cooled Cummins 6BY harbour genset is housed in a soundproofed cabinet in the main deck workshop.
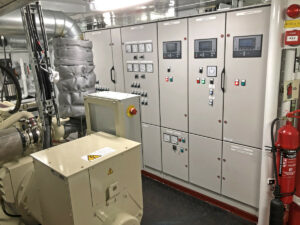
Two Cummins QSB7-based generators feed into Aalskere’s integrated electrical distribution system.
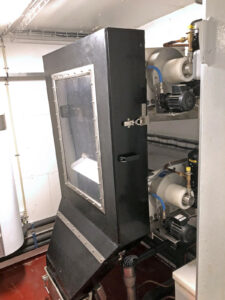
Two Buus flake ice machines give a daily output of 9t.
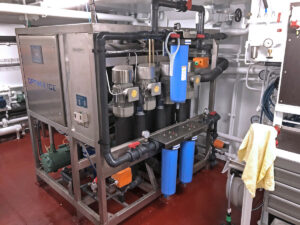
The Optimar slush ice machine can deliver 24t per day.
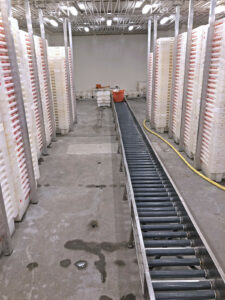
Baskets of fish and squid are moved forward for boxing in the fishroom by roller conveyor, from which sections are removed during a trip.
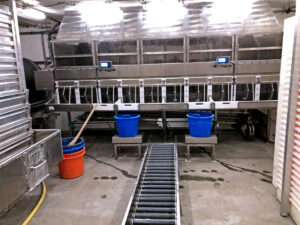
Twelve selection receiving bins are positioned on the aft bulkhead of the fishroom.
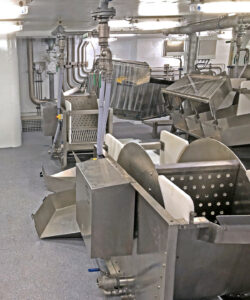
Dedicated rotary fish washers serve the two KM gutting machines.
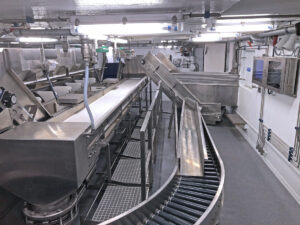
Squid picked off the main selection conveyor are placed in baskets positioned on drop-in trays, before being moved forward by roller conveyor
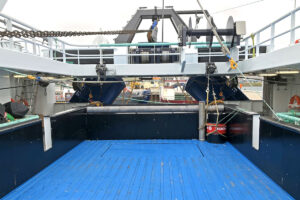
A hydraulically operated gate is positioned between the stern ramp and the central hatch leading to the catch reception hopper.
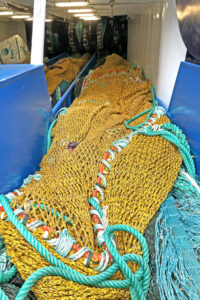
The fishing gear and trawl chandlery for the new Aalskere came from Jackson Trawls of Peterhead.

The middle wire leads over the top of the starboard split trawl winch.
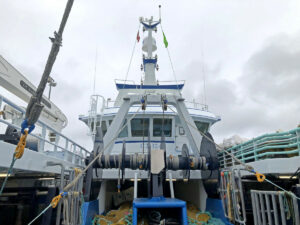
… and a further two from split net drums positioned above the trawl deck.
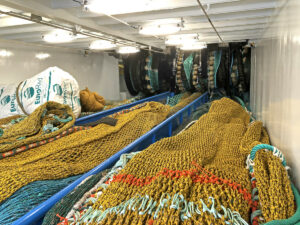
Three nets are hauled along the full-length trawl deck by three sets of split sweepline winches…
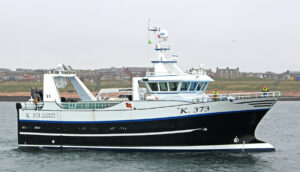
Aalskere is expected to fish in the North Atlantic for extended periods each year.
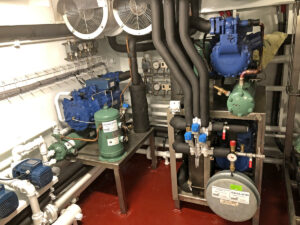
Compressors for the fishroom deckhead and floor chilling systems and Buus 4.5t flake ice machines.
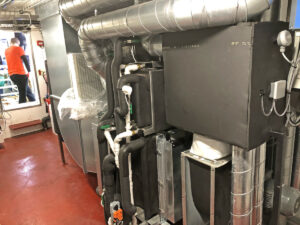
Aalskere’s air-conditioning unit.
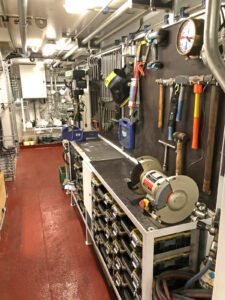
The engineer’s workshop and store aft on the main deck.
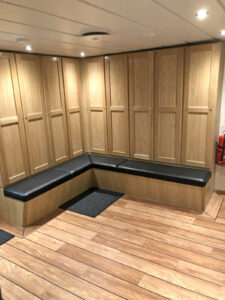
General crew locker room.
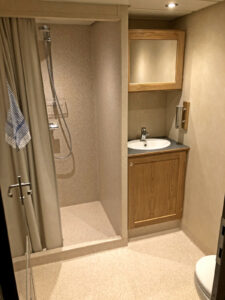
… and two main shower rooms.

One of three four-berth cabins…
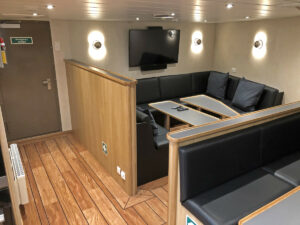
… and TV lounge.
Given the high level of interest that the new Aalskere generated before her arrival at Kirkwall via Peterhead, it is unfortunate that the Covid-19 pandemic spoilt the excitement and celebration that normally prevails when a new state-of-the-art vessel berths at her home port for the first time. During the two weeks that Aalskere was alongside at Kirkwall waiting for the Certificate of Registry and fishing licence to be issued, the vessel was effectively out of bounds to all but her skippers and crew.
Owned by skipper Iain Harcus, his wife Elizabeth, his father John and Don Fishing (Skelwick LLP), Aalskere was built to replace the partners’ previous 23-year-old boat of the same name. Although just over 1m longer than her single-trawl predecessor, by featuring a full-length triple-track trawl deck and stern ramp, the new Aalskere bears absolutely no resemblance to the old one, which had two net drums on the quarter and used a boomswinger to take the codend aboard forward.
Skippered trip-about by Iain Harcus and William Brown, and sailing with a crew of eight or nine, Aalskere is expected to fish in the North Atlantic west of Orkney for most of the year, including the Rockall grounds, with occasional trips to Faroese waters.
The new vessel is insured by Sunderland Marine. Aalskere’s whitefish catches will be placed in boxes supplied by Box Pool Solutions before being sold through Don Fishing, Peterhead.
When fishing west, Aalskere will mainly work from Ullapool, where the extensive quay space and deepwater berthing is well suited to landing requirements and for pulling damaged gear onto the pier for repair.
Having heard good reports from skippers who had taken delivery of a variety of new whitefish boats designed by Ove Kristensen of Vestværftet ApS, Iain Harcus initiated discussions with the Danish designer when he took the decision to build a new boat tailored to his specific requirements, to allow him to fish with enhanced levels of safety, efficiency and catch quality through most of the year, in the challenging conditions routinely endured in the North Atlantic.
General layout
With main dimensions of LOA 35.25m, registered length 30.58m and beam 10.5m, Aalskere’s new design of round bilge steel hull was built to Class at the Stal-Rem SA shipyard in Gdansk, Poland before being towed to Thyborøn for completion by Kynde & Toft.
Given that the registered length was over 24m, the design and build process was monitored throughout to +1AI by Bureau Veritas as the certifying authority. It also carried out the plan approval.
Skipper Iain Harcus said: “A large number of people, using their specific areas of expertise, have made major contributions to Aalskere. Although they are too many to mention by name, they know who they are, so sincere thanks to all. Any new build requires friendship, collaboration and effective teamwork, which was delivered in full by all involved.
“The boat, together with the onboard systems and fishing gear, performed well on the first trip to Rockall. While these are challenging and unprecedented times, Aalskere has started to show her capabilities in terms of fishing efficiency, crew and vessel safety, and catch quality, which should stand us in good stead in years to come.”
Aalskere features three full-length decks: main – accommodation and catch-handling systems; shelter – gear-handling activity and skipper’s ensuite cabins; forecastle deck – protection for the trawl deck.
Layout below the main deck consists of forepeak freshwater tank, bow thruster compartment flanked by deep fuel tanks, fishroom, engineroom and aft peak housing the Scan AS steering gear and the fuel, daily service, hydraulic and lube oil tanks.
The main accommodation areas are arranged across the forward section of the main deck.
Abaft the forepeak, which provides generous storage for provisions, including walk-in fridge and freezer compartments, a well-equipped galley is arranged to starboard. A spacious messdeck/TV lounge, with bench seating surrounding two tables, lies to port.
From the messdeck, a door leads to a central lobby area that gives access to the rest of the accommodation areas. Three four-berth cabins and a two-berth cabin lie to starboard.
Two adjacent shower/WC rooms span the vessel’s centreline.
Including two separate ensuite skipper’s cabins situated on the port side of the trawl deck, Aalskere has sleeping accommodation for 16, thereby meeting one of skipper Iain Harcus’ main requirements. The considerably higher than usual number of beds means that while Aalskere is berthed at Ullapool for some 24 hours between trips, to land and service gear, the full complement of crew can be accommodated onboard, so that the lads travelling home to Orkney via Scrabster on single-track roads can do so after a decent sleep, rather than when extremely tired.
During a trip, the shared cabins will usually be used at 50% occupancy. The spare beds will also be useful when fisheries scientists and observers are away on Aalskere.
A large deck wardrobe, including a WC compartment, is situated on the port side of the deckhouse, from which a short passageway leads onto the fish-handling deck, inboard of the main hydraulic room to port. A workshop, mainly used for maintaining the catch-handling machinery, while also housing laundry facilities, lies across the vessel’s centreline. A compressor room, which also houses ice-making equipment, extends beyond the line of the deckhouse on the port side of the main deck.
Extensive catch-handling systems, supplied by BOAtech ApS of Hanstholm, are arranged across the full beam of Aalskere, between the forward accommodation casing and the large central catch-reception hopper positioned forward of the stern ramp. Capable of holding around 500 boxes of whitefish, the 22m3 hopper is flanked by a secondary wet-gear drying room to starboard, which also leads to the engineroom, and a store room on the port side. This also houses an air-cooled harbour genset.
A triple trawl deck extends the full length of the shelterdeck from six sweepline winches mounted forward to the wide stern ramp. A deck store/workshop and hydraulic room are arranged to starboard of the deck tracks, while the skipper’s cabins occupy a similar area across to port. The shelterdeck is protected from the aft side of the wheelhouse by full-length boat deck side decks, which are continued around the vessel’s stern.
Continued upwards from the hull sides, the main stern gantry is positioned just forward of the stern ramp, with the port leg housing the engine exhausts. The lower and narrower Gilson gantry is situated immediately abaft the wheelhouse. A dedicated gantry serving the middle clump is integral to the construction wraparound section of the boat deck walkway.
Trawling arrangements
Main contractor Kynde & Toft of Thyborøn supplied Aalskere’s full package of hydraulic deck machinery and designed the load-sensing system.
Three single/twin-rig white/ground hopper nets are hauled along the full length of the trawl deck by three 2 x 15t split sweep winches. The middle split sweep winch, from which a single net will usually be worked, is located forward of the port and starboard units.
Two more hopper trawls can be worked from two 2 x 15t sets of split net drums positioned abaft the wheelhouse, the barrels of which are level with the boat deck. These elevated units are mounted on saddles that extend down to the shelterdeck. The middle support between the two sets of split net drums is stepped on a raised box platform positioned above the middle track on the trawl deck.
The two-speed split trawl winches, which have a core pull rating of 34t and a capacity for 2,200m of 26mm-diameter wire, are situated just aft of amidships on either side of the full-length net tracks under the boat deck side walkways. The slightly raised middle wire winch is positioned just ahead of the starboard winch.
The winches operate through a Scantrol autotrawl system, through which the electric/hydraulic pumps are automatically controlled.
The hanging blocks for the outer wires are mounted under the boat deck on either side of the stern ramp, while the middle wire leads over the top of the starboard winch to a block suspended from a dedicated gantry atop the wrap-round boat deck.
Two 15t winches mounted on the boat deck aft of the wheelhouse are used to haul the codends up the stern ramps.
When the bags are clear of the stern ramp, the hydraulically operated ramp gate is raised, followed by the similarly operated hatch above the reception hopper.
A 12t winch mounted on the transom boat deck is then used to hoist the codend up, before the fish are released into the hopper.
Outhaul duties are covered by a second 12t winch. Together with the array of blocks on the Gilson and trawl gantries, the auxiliary winches give various options for handling damaged trawl gear.
EK Marine of Killybegs supplied the 12m stiff-boom crane and 2t landing winch mounted on the port boat deck, which can be used for handling the trawl gear, in addition to discharging catches at the end of a trip.
Catch-handling
The fact that skippers Iain Harcus and William Brown and their crew look to take squid during the short and sporadic early-summer fishery at the Rock influenced catch-handling arrangements on Aalskere.
The different handling that fish and squid require to ensure optimum levels of quality on the market is delivered by two parallel systems, enabling squid to bypass the washing bins and be delivered directly by lift to the fishroom in baskets.
Minimising the time between catches being hauled up the stern ramp and boxed in the fishroom, to maximise product quality at the same time as reducing the manual effort required from the crew, was high on the owners’ list of requirements from the outset.
A lot of detailed thinking was clearly given to the highly automated end result, which was designed, fabricated and installed by BOAtech ApS of Hanstholm.
On being released into the stainless steel reception hopper, catches are moved forward by an elevated conveyor positioned to starboard, before being transferred to a second conveyor leading across the full width of the main deck.
Crewmen select and gut the catch from the waist-height transverse conveyor positioned forward of the aft deck casing. Two sets of Marel electronic scales adjacent to the gutting conveyor are a key part of the selection process. These enable the crew to accurately grade fish by gutted weight, rather than size. The result is that buyers can purchase fish of a predetermined weight – i.e. over 6kg, 3-4kg, etc – secure in the knowledge that it will give a consistent fillet yield closely aligned to their requirements.
Selected fish are placed into one of two large revolving stainless steel drums, with horizontal axes, housed in watertight troughs arranged parallel to, and forward of, the fish selection conveyor. Both independently operated drums are divided into nine sections, three each transversely and radially. After an adjustable length of time, during which fish in the receiving section are sprayed with water, the drum is automatically rotated through 120°. As a result, the fish are then fully immersed in water at the bottom of the trough and washed thoroughly for the selected time, after which the drum rotates through a further 120°.
This second movement lifts fish clear of the washer, and they slide across short drainage racks before being automatically transferred by one of six stainless steel chutes down to the fishroom, via dedicated coamings in the main deck.
Selections of generally smaller fish are made into elevated bins, from where they are released into the main system directly below.
Two KM MKII gutting machines form an integral part of Aalskere’s fish-handling system, and their rapid-fire capabilities will be particularly beneficial during the Rockall spring haddock fishery. Fished picked off the main conveyor belt are delivered by chutes to either the port or starboard gutting machines. After being transferred to dedicated smaller rotary washers, machine-gutted fish are then delivered via chutes to the fishroom selection bins.
The fish-handling area is kept clear of water by four Azcue 4in submersible pumps fitted in deck sumps.
To keep the automated selections made into the revolving fish washers and the gutting machines, 10 freestanding vertical hoppers are arranged against the aft bulkhead of the fishroom. Clear Perspex fronts are fitted to each compartment, enabling the holdmen to immediately see how much fish is in each of the bins, and which ones to focus on first.
To promote the desired levels of efficiency, two sets of Marel electronic scales are positioned forward of the selection bins. On weighing, a label displaying all relevant information, including species, grade, size, time and date, is printed off and affixed to the end of the corresponding box. This information is also transferred automatically to a PC in the wheelhouse, where it is accumulated to provide a running total of Aalskere’s trips.
Squid picked off the main selection conveyor are placed in baskets securely held on removable stainless steel plates. These form a level join between the main belt conveyor and a secondary roller system which, turning through 90°, guides baskets of squid forward on the port side for delivery to the fishroom by a gravity-activated platform that slides down a vertical pillar using only the weight placed on it.
Served by a dedicated access hatch and easy-access companionway, located on the port side aft, Aalskere’s fishroom has a working capacity of over 2,500 BPS nest/stack boxes, stacked 12 to 13 high.
The absence of any terraces further emphasises the amount of space available in Aalskere’s long, flush-floored and parallel-sided fishroom. Positioned between frames 21 and 53, it is 16m long. To maximise efficiency and reduce workload for the crew, baskets of fish, filled from the hoppers at the aft end, are slid forward to the working tier of boxes on a series of rollers. At the start of a trip, eight sections of rollers are joined together in a continuous length, before the forward sections are removed as the number of full tiers accumulates.
Ten tonnes of flake ice, made by two 4.5t Buus ice machines housed in a dedicated room on the main deck aft of the accommodation casing, can be stored in full-height lockers in the fishroom.
Aalskere is also equipped with an Optimar slush ice system that further promotes catch quality. A plant on the main deck can produce up to 24t of slush ice per 24 hours. The constant output is transferred to a 3t storage tank in the fishroom, from where it is delivered by a combination of fixed and flexible pipes to where boxing is taking place.
For most selections of fish, a layer of flake ice is placed in the bottom of each box to give effective drainage. When the contents are neatly aligned, slush ice is pumped in on top of the fish, thereby filling all voids.
The one exception to this is cod, which is not iced in line with the preferences of buyers.
Aalskere’s fishroom refrigeration was installed by Nordkøl ApS of Hanstholm, which also supplied the Buus flake ice machines. Unusually, chilling from the stainless steel refrigeration pipes mounted on the deckhead is augmented by a separate second system positioned under the concrete floor of the fishroom. This was primarily installed to counteract any upward transfer of warmth from the welded channels built into the hull to give freshwater cooling to all the engineroom machinery and ice-making equipment.
When landing, an electric winch mounted on the underside of the main deck, and operated remotely by a crewman in the fishroom, is used to pull stacks of boxes aft towards the port side, from where they are lifted ashore through a large hatch by the EKM stiff-boom landing crane.
The catch-handling deck and fishroom are fully GRP-lined to give flush surfaces to promote optimum levels of hygiene on cleaning, using two large-capacity pressure washers housed in a compartment aft on the main deck.
Engineroom machinery
Aalskere’s aft engineroom, which is characteristic of this design of vessel, features a particularly well-thought-out arrangement that will ensure maximum ease of access for all levels of service.
The ABC 6DZ straight-six main engine develops 749kW @ 860rpm and is coupled to a Hundested 8.36:1 reduction gearbox to turn a Hundested 3,400mm-diameter four-bladed VP nickel-aluminium-bronze propeller mounted in a matching high-efficiency nozzle. The centreline propulsion system is operated through one of four sets of SeaMech electronic engine controls strategically positioned in the wheelhouse.
Two Parker load-sensing pumps drive the main hydraulic system via gearbox-mounted PTOs.
The vessel’s secondary hydraulic system is driven by a 75kW electric power pack. This arrangement also allows the deck machinery to be operated in harbour when the crew are either mending or taking on gear, while the driver is carrying out routine maintenance work on the propulsion unit after stopping the engine.
Two Cummins QSB7 auxiliary engines drive 164kVA Newage Stamford 415/3/50 generators. The electrical generators are fully synchronised through the switchboard panels to give load-sharing and automated auxiliary start-up.
An interesting feature of Aalskere is that the engines, hydraulics and fishroom refrigeration/ice machine cooling/ice machinery are freshwater-cooled by welded channels built into the hull. By eliminating any growth in the cooling systems and pipe corrosion, this arrangement brings the major advantage of being maintenance-free.
The engine exhausts are routed up through the port leg of the stylishly raked aft gantry.
A Cummins 6BT air-cooled harbour genset is housed in a workshop on the main deck aft.
Aalskere can start a trip carrying 80,000 litres of fuel, housed in a combination of six tanks – two forward and aft and two double bottom tanks under the fishroom. Electronic fuel gauges and a fuel meter are conveniently placed in the engineroom adjacent to the pipe manifolds leading from the various tanks to show precisely how much fuel the engineers are transferring.
Freshwater capacity is 53,000 litres. This includes 23,500 litres in the bulb and 15,000 litres in a starboard wing tank in the engineroom.
Hydraulically operated Hundested bow and stern thrusters of 186kW are fitted to give maximum vessel manoeuvrability in restricted areas.
A particular feature of Aalskere is the extremely low level of noise evident throughout the boat. When steaming at 10.5 knots during trials, with 95% load on the ABC propulsion engine, the noise levels in the messdeck and cabins was recorded at 55dB (A). These very low levels, which mean that the main engine is barely discernible, are highly appreciated by the skippers and crew. n
Thanks to everyone whose contributions made this remotely assembled feature possible, particularly Iain Harcus, who despite being focused on getting Aalskere ready for her first trip, still found the time to take and email all the onboard photos and answer frequent questions.
Scanmar net- and catch-monitoring
Fully satisfied with the results from Scanmar net-monitoring equipment on the previous Aalskere, the consistent performance of which contributed to the new build, skipper Iain Harcus had no hesitation in opting for net-monitoring receivers, software and sensors supplied, installed and commissioned by Scanmar UK of Peterhead, which has a longstanding association with the owners.
A Scanmar Trawleye sounder mounted on the headline provides information on the opening of the trawl from footrope to headrope, and clearance from seabed to footrope. The density of fish at the mouth of the trawl is displayed with a value from 0-9 and colour density.
A headline flow sensor is a new addition to Aalskere, and is primarily mounted on the port net to focus on net symmetry and speed of water flow through it, but will be transferred to the starboard net to alter gear when required. This information is interfaced to the Scantrol autotrawl system, enabling wire lengths to be constantly adjusted to keep the gear square.
Four SS4 catch sensors will be shared equally on the bags when Aalskere is twin-rigging. Another two SS4 catch and temperature sensors will be used in the same manner to monitor water temperature.
Gear spread is monitored by Scanmar SS4 extended double-distance door sensors, which also relay door angle (pitch and roll) readings to monitor stability of the trawl doors. Extended distance assists the flow sensor in relaying information on whether the clump is in line with, in front of or behind the trawl doors.
Peterhead netmaker supplies full fishing gear package
Jackson Trawls supplied a full package of fishing gear and trawl chandlery to Aalskere, thereby continuing the Peterhead company’s longstanding relationship with skipper Iain Harcus.
In terms of ground gear, the biggest net is a high-standing single whitefish trawl rigged on 120ft of 21in and 24in hoppers. With 300mm mesh in the top sections and 200mm in the lower, this trawl features a Dyneema headline and 11in titanium floats.
Designed to target more groundfish while retaining the capability to take higher-swimming haddock, Aalskere’s second single trawl is a 150ft net set on 18in hoppers, of similar construction to the heavier hopper net.
When twin-rig trawling, Aalskere tows two 120ft trawls rigged on 16in and 18in hoppers. These feature 200mm mesh in the top and 160mm in the lower sections, Dyneema headlines and 8in titanium floats.
Built to require low maintenance, Aalskere’s nets incorporate three tearing strips and double Carflex selvages to ensure quick mending at sea, and reverse yellow and blue Sapphire 5mm double 120mm and 140mm codends, with the latter being used when fishing in Faroese waters.
Jackson Trawls also supplied a full trawl chandlery package to Aalskere, including Dyneema Gilson ropes, 5mm double Sapphire codends and tunnels, sweeplines and three 2,200m lengths of 26mm-diameter Bridon Starfish Dyform trawl wire.
Depending on the grounds being fished, Aalskere will use either a set of NETS 5.25m2 Super Sea Tracker or Thyborøn Type 23 trawl doors, and when twin-rigging, a 2,500t clump to spread the gear.
Eighty-five-fathom sweeps are usually worked behind the trawl doors – longer when fishing in deeper water. From the doors, the standard sweeps are made up of 60 fathoms of 36mm heavy wire single bridles and 25 fathoms of 19mm mid-link ground chains/18mm-diameter wire sweeps.
Third Aalskere
The new Aalskere is the third whitefish trawler of the same name and number to be skippered by Iain Harcus in the past 25 years.
Aalskere takes her name from a small skerry off Papa Westray where Iain Harcus started his fishing career from his parents’ home. A profile of Papa Westray and Westray is proudly displayed on Aalskere’s stem crest, in recognition of his lifelong association with the small islands northeast of mainland Orkney.
After first going potting with his father John, Iain Harcus secured a berth on Westray skipper John Bain’s 27m trawler Rivo I K 39, built at Truro in 1986, later joining Tam Harcus on the Campbeltown-built Orkney Reiver K 49.
In 1989, Iain Harcus took a share in skipper Tam Harcus’ new Norwegian-built 27m trawler Keila K 121.
After six years as engineer on Keila, Iain Harcus began his career as skipper by buying the Campbeltown 87 Challenge II UL 33 from Peterhead skipper Gavin Thain. Renamed Aalskere K 373, Challenge II was built in 1988 as Maranatha II UL 33 for pioneering Macduff skipper Niven Ogg.
Five years later, Iain Harcus took the major decision to replace the first Aalskere with the 33.9m trawler Vandal LK 337, built at the Parnica shipyard in Poland in 1977 for skipper Duncan Cumming and his sons Trevor and Angus. This transaction included Angus becoming skipper of the Campbeltown 87, which was renamed Maranatha LK 337, while Trevor remained on the newly renamed Aalskere.
When the new Aalskere was nearing completion last year, her consistently successful predecessor, which is expected to be sold soon, was renamed Gemma Jane K 184.
The K 373 registration continues the longstanding preference shown by Orkney skippers in this short summary for the numbers of their vessels to total 13.
High-end electronics equipment in streamlined wheelhouse
On entering Aalskere’s wheelhouse, the immediate feeling is of space and orderliness, enhanced by the superb level of natural wood finish that is evident throughout the boat.
Skipper Iain Harcus placed the emphasis fairly and squarely on a clean and uncluttered wheelhouse interior, made possible by ever-advancing electronics technology.
A desk area housing the E-Catch reporting computer is positioned on the starboard side forward of hot drink-making facilities and a built-in sink. The trawl console extends along the middle of the wheelhouse, adjacent to extensive bench seating arranged in the aft corner to port.
A single skipper’s chair, supplied by E Vejvad Hansen of Hanstholm, is positioned on the vessel’s centreline at the head of a U-shaped console in front of three 55in 4K bridge monitors. Slightly angled in to each other and set back from the wheelhouse windows, these three units form a quad-view video wall operated through an integrated trackball control system installed by Woodsons, which supplied the majority of the electronic equipment.
Another seven Neovo X24 monitors are located in the overhead forward console, and there are a further six X19 glass-fronted screens at the trawling console.
Slim steering consoles are arranged at the forward corners of the wheelhouse.
Ten monitors are integrated into the Woodsons quad-view video wall control system, selection of which is chosen by a single trackball control and cursor that moves seamlessly between all connected screens to take control of any source within the video wall. An unlimited number of fishing, steaming and in-harbour pre-set modes can be made by the skippers, with the addition of day/dusk/night brilliance control pre-sets across all screens. All can be accessed through either a fixed touchscreen display or iPad.
The importance of accurate seabed mapping and fish classification is highlighted by the array of top-end acoustic equipment now functioning in Aalskere’s wheelhouse.
This includes a SeapiX 3D multibeam sonar (150kHz), providing the skippers with high-resolution 2D and 3D seafloor mapping, with images of detected fish marks overlaid in real time on the chart. The fish marks and seafloor mapping images are displayed across three video-wall screens providing 2D and 3D mapping with ground hardness, echosounder view with triple beam and bottom lock, and fish classification tools utilising a choice of four 120° beam sonar swathes. Using this powerful combination of high-resolution echosounder and seafloor mapping, fish marks can be seen in real time and in relation to their 3D environment and the fishing gear, enabling the skipper to effectively steer the net towards the mark.
Vertical bottom-sounding duties are handled by a Kaijo KSE310 38kHz split-beam fish-sizing echosounder. Having been installed in the previous Aalskere, the Kaijo echosounder’s performance is well-proven in the detection of marks, and accurate calculation of the size of fish within them, utilising its 15 separate beams.
A WASSP F3i multibeam sonar supplied by Furuno UK is also installed. This 160kHz multibeam unit provides seabed mapping and real-time ground hardness, enabling the skippers to quickly build up an accurate 3D representation of the bottom they are fishing, so the gear can be towed tight to small peaks and ground edges where fish could be lying.
Aalskere’s location is displayed at all times on two FishingWin V9 2D/3D plotting systems alongside a TimeZero V4 plotting system. All are interfaced to give a combination of AIS/ARPA, wind, tidal and chart overlays.
Two Sailor 6570 DGNSS navigators process details of Aalskere’s position. Vessel heading is provided by type-approved JRC JLR-21 satellite and Simrad RGC50 compasses.
The Furuno FAR-2228 25kW and JRC JMA-5410-6X BB units provide radar and AIS tracking, both within the radars themselves and also interfaced to the plotters.
Steering is handled by a Navitron NT 921G dual-head autopilot complete with three joystick control sets.
The mandatory GMDSS communications required for the areas where Aalskere will fish include a Sailor 6310 MF/HF 150W radiotelephone, Sailor 6222 Class A DSC VHF, JRC NCR 333 type-approved Navtex, Jotron Tron 60S GPS auto-release EPIRB, Tron SART 20 and two Entel HT649 handheld VHFs.
Additional communications equipment includes two Sailor 6210 VHFs, Phontech 3102 20-way talkback system, LT-3100 Iridium communications system, and e-SEA 60Ka internet and e-SEA 80 satellite TV systems.
Woodsons also installed an extremely comprehensive CCTV system that utilises 24 cameras and an underwater camera monitoring the propeller, nozzle and triple rudder at all times.
Resin deck coatings by PBP Services
Aalskere’s trawl and fish-handling decks are coated with specialist Lloyds-approved Degafloor hardwearing non-slip resins.
PBP Services of Fraserburgh sent a trained and experienced team to Thyborøn to apply the four-coat resins as Aalskere was being readied for sea trials.
PBP Services is the only approved contractor in the UK for these specialist German resin products. Degafloor was developed and introduced into the fishing industry seven years ago, since when it has become extremely popular with skippers, yielding excellent results.
The unique properties of the resins allow for the four-layer system to be applied and cured on the same day if required, with each coating curing in under one and a half hours, allowing almost immediate foot traffic after application.
The resin coating has elastic properties to ensure against movement of steel, which also makes it comfortable underfoot for long periods of standing time.
It is also very aesthetically pleasing, with its blended colours of anti-slip quartz suspended throughout the film thickness of the coatings.
The resin is extremely hardwearing, tough and impact-resistant, and is easy to clean and maintain.
As well as Lloyd’s German shipping class certification, it also comes with health and safety anti-slip testing and certification, and food and drink industry certification for safe production of factory foods.
AALSKERE K 373
DETAILS
Owner: Skelwick LLP, Kirkwall, Orkney
Designer: Ove Kristensen, Vestværftet ApS, Hvide Sande, Denmark
Boatyard: Kynde & Toft, Thyborøn, Denmark (hull built under subcontract at Stal-Rem SA shipyard, Gdansk, Poland)
Class: Bureau Veritas +1A1, Fishing Vessel, unrestricted navigation, dot MACH
Agent: Don Fishing Ltd, Peterhead
DIMENSIONS and CAPACITIES
Length overall: 35.25m; Length reg: 30.58m; Beam: 10.5m; Depth moulded: Main deck 4.59m: Shelterdeck 6.97m; Draught: 4.59m; Tonnage: 644t gross; Fuel: 80,000 litres; Freshwater: 53,000 litres; Lube oil: 2,800 litres; Hydraulic oil: 3,300 litres; Fishroom: 2,500+ boxes; 2 x 4.5t flake ice; 3t slush ice tank
ENGINEROOM
Main engine: ABC 6DZ 749kW @ 860rpm driving through a Hundested 8.36:1 reduction gearbox to a 3,400mm-diameter four-bladed VP propeller; Speed: 10.5 knots
Auxiliary engines: 2 x Cummins QSB7 164kW @ 1,500rpm gensets; Cummins 6BT 91kW @ 1,500rpm harbour genset
Bow and stern thrusters: Hundested 186kW
Fuel and oil filters: CC Jensen
Bilge, deckwash and fish-handling system pumps: Azcue
DECK MACHINERY
Supplier: Kynde & Toft, Thyborøn
3 x 34t split trawl winches with capacity for 2,200m of 26mm-diameter wire; Scantrol autotrawl system; 3 x split sweepline winches 2 x 15t; 2 x split net drums 2 x 15t; 2 x codend Gilson winches 15t; 2 x gantry winches 12t; Fishroom winch electric 2t; EK Marine knuckle-boom deck crane 2t @ 12m c/w 2t landing winch
FISH-HANDLING/FISHROOM
Fish-handling system: BOAtech, Hanstholm; Fishroom chilling: Nordkøl, Hanstholm; Flake ice: Buus 2 x 4.5t; Slush ice: Optimar 24t
ELECTRONICS
Suppliers: Woodsons, Aberdeen; Furuno UK, Fraserburgh and Scanmar UK, Peterhead
Fish detection
Kaijo KSE310 38kHz split-beam fish-sizing echosounder; SeapiX 150kHz 3D sonar system; JRC JFC 180BB multi-frequency sounder; WASSP F3i multibeam sonar; Scanmar Scanbas net-monitoring system c/w double-distance door sensors; Scanmar headline Trawleye and symmetry sensors and six SS4 catch sensors
Navigation
JRC JMA-5410-6X BB and Furuno FAR 2228 BB 25kW radars; 2 x Sailor 6570 DGNSS navigators; Simrad RGC50 gyrocompass; JRC JLR-21 satellite compass; 2 x FishingWin V9 plotting systems; TimeZero Pro plotter; Navitron NT 921G autopilot system; Ultrasonic wind speed and direction sensor
Communications
Sailor 6310/2 150W GMDSS MF/HF SSB; Sailor 6222 Class A DSC VHF; 2 x Sailor 6210 VHF; 2 x Entel HT649 GMDSS handheld VHFs; JRC NCR 333 Navtex type-approved receiver; Phontech 3102 20-way talkback system; Jotron Tron 60 GPS auto-release EPIRB; Tron SART 20; e-SEA 60Ka internet system; e-SEA 80 satellite TV system; LT-3100 Iridium communications system; CCTV system c/w 25 cameras
FISHING GEAR
Net supplier: Jackson Trawls, Peterhead – 1 x 120ft whitefish trawl rigged on 21in and 24in hoppers; 1 x 150ft white/groundfish trawl rigged on 18in hoppers; 2 x 120ft twin-rig whitefish trawls rigged on 16in and 18in hoppers; Warp supplier: Jackson Trawls, Peterhead – 2,200m x 26mm-diameter Bridon Starfish trawl wire; Doors: NETS 5.25m2 Super Sea Tracker trawl doors (Jackson Trawls); Thyborøn Type 23 2,100kg; Clump: Thyborøn 2,500kg
ACCOMMODATION
2 x single-berth ensuite skipper’s cabins; 1 x two-berth and 3 x four-berth cabins
GENERAL
Engine controls: SeaMech; Insurance: Sunderland Marine; Steering: Scan AS; Wheelhouse seat: E Vejvad Hansen