Skippers David Gatt and Barry Reid and the crew quickly started to confirm the capabilities of the versatile new 27.8m whitefish boat Audacious BF 83, by landing 2,000 boxes of whitefish at Peterhead from back-to-back pair-seining trips in just over two weeks following the vessel’s well-attended naming ceremony at Macduff, reports David Linkie
Audacious is the latest in a succession of new whitefish boats that reflect the confidence skippers have in the long-term future of their industry, based on healthy and sustainable stocks allied to strong market demand, given viable fishing opportunities and quota allocations. In addition to full versatility between pair-seining and single-boat trawling, the vessel features a number of new ideas, including:
- custom-built touch-screen vessel management alarm, monitoring and control systems
- two sets of fishroom scales and labelling machines
- two KM 5 gutting machines
- Scanmar new-generation net-monitoring receivers.
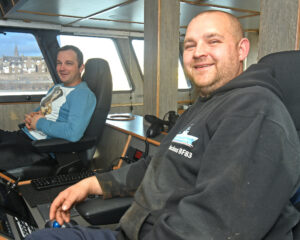
Audacious skippers Barry Reid (left) and David Gatt.
That Audacious is designed in line with the requirements of two highly motivated skippers, who although already well-experienced, still have most of their careers ahead of them, is particularly significant.
So too is the fact that one of the most advanced whitefish vessels to join the Scottish fleet to date was designed and completed in-house by Macduff Shipyards within sight of Whitehills, the small traditional Moray Firth fishing village where David Gatt and Barry Reid were brought up, and where Billy Gatt, a partner in Audacious together with Don Fishing, has lived all his life.
At a time when focus is understandably on the latest Brexit negotiations, it is worth recognising and remembering the extent to which UK fishermen, along with shore-based companies, continue to lead from the front in terms of both sustainability and boatbuilding.

Twin split net and bagging drums are positioned at each end of the trawl deck, which is protected by sidewalks at boat deck level.
Too often, good news stories in the fishing industry are undersold to the general public, while the efforts of everyone involved with successful outcomes are, at best, glossed over.
The reasons for the Audacious partnership placing the order for their new whitefish boat, and the end result nearly three years later, are achievements that everyone who contributed towards the outcome should be quietly proud of.
Audacious replaces its 27.4m predecessor of the same name, built as the single-rig whitefish trawler Nordfjordr K 139 in 1989 by James N Miller & Sons of St Monans for Orkney skipper Malcolm Brown. Subsequently sold to Peterhead and re-registered PD 118, Nordfjordr became Audacious five years ago, before being bought by DR Diesel of Kilkeel in September as Audacious BF 830, when its replacement was nearing completion at Macduff.
Although designed to replicate the fishing patterns of its predecessor, and of similar LOA and carrying capacity, in every other respect, including bagging aft, Audacious is a very different boat, with a considerably lower main engine power (577kW compared to 735kW).
Incorporating the latest design, fishing and propulsion technologies, the end result is designed to bring enhanced levels of fishing efficiency, crew/vessel safety, catch quality and fuel economy in years to come.
That Audacious and pair-seining neighbour Faithlie FR 220, completed just 16 months ago by Vestværftet ApS for skipper Davie Milne, replace a pair-team with a combined age of 60 years, underlines the extent to which the current influx of new vessels is long overdue, and is just as important to the long-term future of the UK fleet as sustainable stocks and viable fishing quotas.
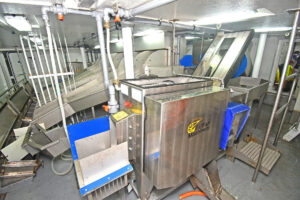
KM gutting machines are positioned either side of a highly automated fish-handling system designed to optimise catch quality.
Shortly before starting to land in Peterhead fishmarket at the end of a successful maiden trip, skipper David Gatt said: “We are extremely pleased with the end result, and with initial indications of how Audacious will perform. In addition to the builders, a large number of people have made highly significant contributions to the design, build and completion of Audacious, including those who work diligently behind the scenes. Although too many to name individually, they know who they are, so to everyone, sincere thanks for your invaluable support down the years.
“Watching Audacious evolve in the offices at Macduff, before materialising and nearing completion on our doorstep, has been a rewarding experience. Now the onus is on us to prove the fishing capabilities of a locally-built boat in years to come. While nothing can ever be taken for granted in our industry, particularly at the moment, we are quietly confident that in Audacious, we have a suitable tool for the job, and one that will help us to meet the challenges that will inevitably be encountered.”
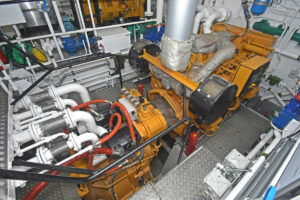
General view of the engineroom and the Caterpillar 3508C main engine.
Insured by Sunderland Marine, Audacious is expected to normally fish six- to eight-day trips, working through Don Fishing Company. The vessel’s whitefish catches will be placed in boxes supplied by Box Pool Solutions, before being sold on Peterhead fishmarket. Skippers Barry Reid and David Gatt expect to share wheelhouse duties trip about, after sailing together on the first few trips. Mate Bryan Sangster, and engineers Ian ‘Chocky’ Anderson and Harry Smith, along with Matthew Pirie, James Napier and Gavin Wiseman, form a crew of six.
Macduff Shipyards began to design the layout of Audacious, in close collaboration with skippers David Gatt and Barry Reid, nearly three years ago. Particular emphasis was placed on combining a spacious working deck, a streamlined catch-management system and good fishroom capacity with propulsion efficiency and fuel economy.
The new deep round bilge hull form was developed in close co-operation with Macduff Ship Design, with CFD technology used to optimise the underwater design, propulsion efficiency and fuel economy. Macduff Ship Design subsequently produced a full set of hull construction plans that were approved for DNV classification.
With main dimensions of LOA 27.8m, length BP/registered 23.95m, beam 8.6m and depth to shelterdeck 6.4m, the hull was fabricated under subcontract at Finomar Shipyard in Szczecin, Poland, before being towed to Macduff for all machinery installation and full internal fitting-out, when Seafish and the MCA carried out their customary surveys.
On completion, Audacious sailed to Fraserburgh, where the vessel was rigged out, after being taken out of the water by shiplift for final hull work. At this time, PBP Services undertook a final application of two-coat PPG (Sigma) paint to the hull. Signwriter Nic Nicolaou applied the finishing touches, in the form of stem and quarter crests depicting the Fitehills (Whitehills) crest.
General layout
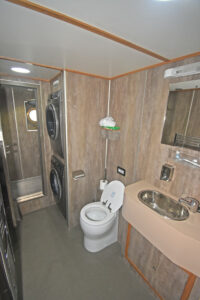
Shower/laundry and WC room on the main deck.
Audacious features three decks. From forward, the main deck is subdivided into three different areas: main accommodation; highly automated catch-handling processing; and central large refrigerated reception hopper, flanked either side by a walk-in storeroom and engineer’s workshop.
A large winch room, housing three separate split trawl winches, is situated at the fore end of the shelterdeck, positioned forward of an upper accommodation area and the trawl deck, on which twin trawl tracks are arranged in line with hydraulically operated stern gates either side of the central codend hatch aft.
At boat deck level, sidewalks giving enhanced protection on the trawl deck extend aft from the aluminium wheelhouse, fitted immediately forward of amidships, to wrap around the stern, where two bagging drums and a Gilson winch are mounted under the strongly constructed trawl gantry.
The hull below the main deck is subdivided into five watertight compartments: forepeak, bow thruster compartment, two large freshwater tanks, 1,300-box-capacity fishroom, engineroom, and aft peak housing fuel, lube and hydraulic oil tanks.
The exceptionally high quality of finish evident in all internal accommodation areas, which feature modern laminates and planked flooring, is a further example of the excellent workmanship for which Macduff Shipyards is renowned.
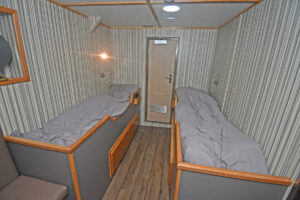
Two-berth skipper’s en suite cabin at boat deck level, port side forward.
The messdeck and galley, positioned to port of the vessel’s centreline, run almost the full length of the deckhouse, forward of a central changing room. Four twin-berth cabins and a large shower/WC compartment are arranged in the similar area to the starboard side of the deck casing, forward of a dedicated ice-making room accessed off the catch-processing deck.
A skipper’s twin-berth en suite cabin is located parallel to the portside of the deck casing, one deck higher at shelterdeck level, adjacent to a safety locker. A sixth two-berth cabin lies to starboard, aft of a walk-in electrical room. A large gear store extends the full length of the deckhouse along the starboard side of the hull, with direct access onto the trawl deck.
All internal accommodation areas are served by slim-profile electric heaters and an air-conditioning system supplied by Easy Air UK.
The vessel’s complete firefighting systems, together with crew protective clothing, lifesaving equipment and CO² system, were supplied by Blue Anchor Fire and Safety Ltd of Fraserburgh.
Quiksling and Lalizas MOB recovery systems are also fitted.
Fishing arrangements

Looking down on the trawl deck from the wheelhouse roof.
French hydraulic specialists BOPP manufactured the customised package of deck machinery fitted on Audacious. This will be serviced in years to come by Jim Cowie and his team from JC Hydraulics, BOPP’s agent in Peterhead. Jim Cowie worked alongside BOPP engineers to commission the sophisticated control system, which performed well from the off, initially in single-boat trawling mode, before Audacious buckled up with Faithlie for the first time for pair-seining trials in the Hole of the Broch.
BOPP also designed the load-sensing hydraulic system, installation of which was carried out in-house by Macduff Shipyards.
Three split trawl winches, with a combined core pull of 53t, are housed in a large walk-in winch compartment arranged across the full beam forward, from which warps run over three large-diameter sheaves and under the wheelhouse floor, before a similar integrated triple-sheave arrangement directs them to selected hanging blocks mounted on the underside of the trawl gantry.
Mounted across the centreline, the dedicated pair-seining winch has a designated capacity of 1,000m x 24mm-diameter wire and 380m x 28mm-diameter wire and four coils of 50mm-diameter four-strand combination rope. Powered by a Poclain two-speed motor, and fitted with a hydraulic dynamic disc brake for fast shooting, the pair-seine winch has a 20t core pull at 30m per minute on first speed, and 10.5t/60m per minute on second speed.
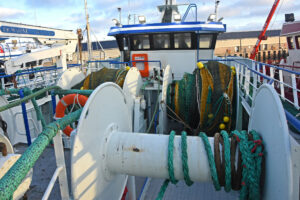
Bagging drums are positioned at boat deck level.
Two split trawl winches, positioned slightly aft on either side of the middle unit, are angled towards the central sheaves. Again fitted with Poclain two-speed motors, giving core pull ratings of 16t/32m per minute in first speed and 8t/64m in second, the outer winches can accommodate 1,650m of 24mm-diameter wire.
All three winches are operated through a bespoke BOPP automated system. When pair-seining, the middle winch is remotely controlled in conjunction with a Scantrol PairLink and the Scanmar net-monitoring system.
The automated functions of the radio-operated Scantrol PairLink delivers maximum benefit from the high-tech fishing systems installed on each boat, and allows the nominated master vessel to control the partner boat when towing, including alignment, course heading, separation distance, propeller pitch, and adjusting warp length to maintain net symmetry.
Once the required distance, usually 0.25-0.3 miles, is programmed in, the Scantrol PairLink software keeps the two boats the set distance apart automatically, by collecting information from the vessels’ autopilots.
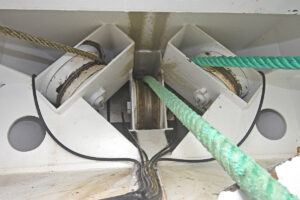
… in the forward winch room, from which three rollers lead the warps under the wheelhouse floor.
Two large-capacity split net drums are mounted on the shelterdeck abaft the deck casing, to provide a large working deck area that will be beneficial to the crew when mending torn gear. The port unit is positioned slightly further aft, allowing for the fishroom landing hatch offset to the portside. The 2 x 10t split net drums are served by twin trawl tracks to port, passing either side of the central catch hopper and a companionway giving access to the transom boat deck.
Hydraulically operated stern gates, which can be lowered at the time of hauling and shooting the gear and are capped with large-diameter rollers, are incorporated into the transom openings. With the stern already watertight up to the level of the shelterdeck, this feature provides an added metre of protection, and will further enhance safe working when the crew are repairing gear in heavy weather.
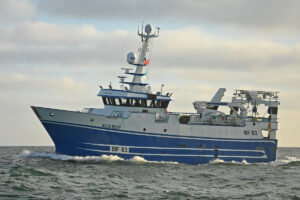
Audacious, which features a full-length boat deck, in profile.
Two hydraulically operated shooting poles, recessed into the shelterdeck when lowered, are also fitted, to assist with taking the heavy pair-seines onto the split net drums.
Two 8t bagging winches are mounted at boat deck level towards the transom stern. This arrangement enables the wings and mouth of the pair-seine to be hauled by the net drums until the middle hoppers are just forward of the bagging drums, which are then used to take up the long taper and codend extension.
The codend is lifted centrally at the transom by a 7.5t Gilson winch mounted at boat deck level, before being hauled inboard through the stern gantry between the shelterdeck and boat deck, and released through the hydraulically operated hatch of the 250-box-capacity reception hopper. In order to maintain fish quality as soon as catches are taken aboard, the central reception hopper is refrigerated.
The Gilson winch, together with the bagging and net drums, are fitted with Poclain multi-brake discs.
All the deck machinery can be remotely operated from the trawl console in the wheelhouse, from which skippers David Gatt and Barry Reid have a commanding view of all shooting, hauling and bagging activities.
Manufactured by EK Marine of Killybegs, from Weldox 800 plate a customised knuckle-boom crane (1.2t at 10m reach), featuring continuous slew and radio remote control, is stepped on the port boat deck, aft of the fishroom landing hatch.
Fish-handling and storage

An elevated conveyer to port leads fish forward from the central reception hopper…
After being released from the codend into the chilled hopper, whitefish are moved forward by an elevated conveyor positioned to port, before being transferred to a second conveyor leading across the full width of the main deck, for gutting and selection.
Audacious is equipped with a highly-automated whitefish-handling and electronic catch-management system, designed and fabricated by VCU of Urk, Holland, to deliver optimum levels of catch quality and full traceability in years to come, while minimising the amount of manual effort required from the crew.
Key components of the catch-handling system, which the crew reported to have proved its efficiency from the first haul, are two electrically driven KM5 gutting machines. Supplied by Macduff Shipyards and Seagate Fabrication of Peterhead, who as agents for Danish manufacturers KM Fish Machinery AS, the gutting machines are positioned on either side forward of the main conveyor. Fish selected for machine-gutting are placed in dedicated troughs, from which short elevated conveyors lead directly to the port and starboard machines, both of which are served by dedicated washers and chutes leading to the fishroom.
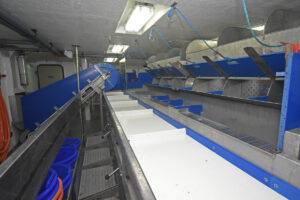
… to the main gutting and selection conveyor.
Crewmen select and gut the catch from the waist-height transverse conveyor, positioned forward of the aft deck casing.
Manually gutted fish are either placed into elevated bins, or directly into compartmentalised rotating drums positioned directly below. The two large revolving stainless steel drums are housed in watertight troughs arranged parallel to, and forward of, the fish selection conveyor. Both independently-operated drums are divided into nine sections, three each transversely and radially. After an adjustable length of time, during which fish in the receiving section are sprayed with water, the drum is automatically rotated through 120°. As a result, the fish are then fully immersed in water at the bottom of the trough and washed thoroughly, after which the drum rotates through a further 120°.
This second movement lifts the fish clear of the water, and they slide across short drainage shelves before being automatically transferred by one of six stainless steel chutes down to the fishroom, via dedicated coamings in the main deck, tight to the aft deckhead of the accommodation casing.
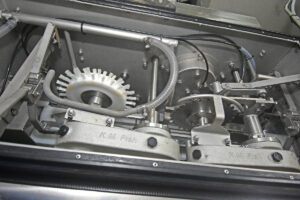
Rotating gutting blades and cleaning brushes in the gutting machines, manufactured by KM Fish Machinery AS.
The fish-handling area is kept clear of water by four Azcue 2.5in pumps, fitted in deck sumps.
To keep the automated selections made into the revolving fish washers and the gutting machines, eight vertical hoppers are arranged against the aft bulkhead of the fishroom. Clear Perspex fronts are fitted to each compartment, enabling the hold men to continually view how much fish is in each of the bins, and decide which ones to focus on first.
Two sets of VCU electronic scales and box-labelling printers are positioned at each end of the holding hoppers in the fishroom. In another notable first for a Scottish whitefish boat, the second units will further reduce the time required for fish to be boxed, iced and stacked for the duration of the trip, further enhancing catch quality. Data recorded by the VCU catch management system is transferred automatically to a PC in the wheelhouse, where it is accumulated to provide a running total of the species, size and weight of the fish onboard.
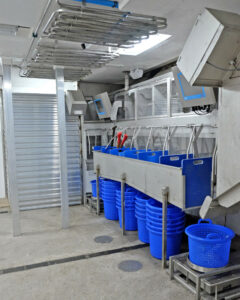
Clear-fronted holding bins are positioned between two sets of fish-weighing and labelling equipment, as part of the highly automated VCU catch-handling and management system installed on Audacious.
Served by a dedicated access hatch and easy-access companionway located to port, the fishroom has a working capacity of 13,000 nest/stack boxes, placed in tiers 11 high.
Eight tonnes of flake ice, made by two 4.5t Buus ice machines positioned in a walk-in compartment located in the aft starboard corner of the main deck casing, can be stored in full-height lockers in the fishroom directly below.
Nordkøl ApS of Hanstholm supplied the ice machines, in addition to fitting the stainless steel refrigeration pipes mounted on the fishroom deckhead.
When landing, a 3t winch, mounted on the fishroom floor at the aft side of the landing hatch, is used to pull full double stacks of boxes aft towards the portside, from where 22 boxes are lifted ashore by the EK Marine knuckle-boom landing crane and Rotzler 2-speed 2t landing winch.
Engineroom machinery
The aft engineroom on Audacious, which is characteristic of this design of vessel, features a well-thought-out arrangement, ensuring that engineers Harry Smith and Ian Anderson have maximum ease of access for all levels of service.
Finning Power Systems supplied three Caterpillar engines to Audacious.
The 3508C propulsion unit develops 577kW @ 1,200rpm and is coupled to a Heimdal HGH595F gearbox of 9.438:1 reduction, to turn a 2,800mm-diameter four-bladed CP propeller.
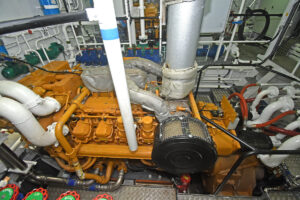
The Caterpillar 3508C main engine and Heimdal 9.438:1 gearbox, on which two PTSs drive large-capacity Rexroth load-sensing pumps.
Operated through one of three sets of Lyngaa Marine electronic engine and propeller pitch controls strategically positioned in the wheelhouse, the slow-running CP propeller turns in a high-efficiency nozzle to provide optimum thrust in conjunction with a triple-rudder system. Audacious returned an average top speed of 10 knots on engine trials off Fraserburgh.
The main hydraulic system is driven by two large (500 litres per minute) Rexroth load-sensing pumps run off PTOs mounted on the Heimdal gearbox.
An electrically driven 39kW power pack is used to drive the towing pump for the pair-seine winch when Audacious and Faithlie are fishing. Two additional electrically driven units enable the deck machinery to be operated when the crew are working on the fishing gear in harbour. All three electrically operated hydraulic pumps can also be linked up to operate a gear-retrieve system.
A standalone power pack, located on the portside of the engineroom, enables the landing crane to be operated if the drivers are carrying out routine maintenance work on the main or auxiliary engines in harbour.
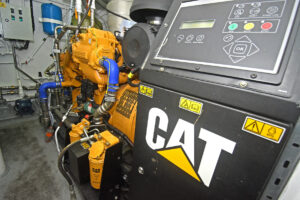
Caterpillar C7.1-based gensets are mounted on the port and starboard tank tops.
Main electrical supplies on Audacious come from two Caterpillar C7.1 auxiliary engines driving 150ekW 415/3/50 generators.
As customary on new-builds by Macduff Shipyards, RD Downie of Fraserburgh undertook the full electrical wiring and installation of Audacious, including the wiring of the BOPP, Marble and Lyngaa control systems.
Box coolers for the three Caterpillar engines and hydraulic system circuits came from Blokland of Holland.
The engine exhausts are routed up through stylishly raked box housing at the starboard quarter, forward of the stern gantry. This arrangement on Audacious, which works as starboard boat, provides skippers David Gatt and Barry Reid with clear lines of vision when Audacious goes alongside Faithlie to pick up and pass over the end.
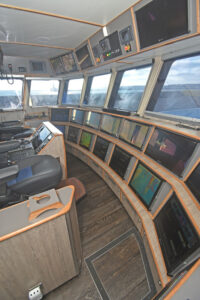
Woodsons, Furuno UK and Scanmar UK supplied an extensive range of the latest electronics equipment…
Audacious can start a trip carrying 48,000 litres of fuel, housed in a combination of six tanks – two double bottom under the fishroom, wing tanks in the engineroom, and two transom tanks. Thirty-two thousand litres of freshwater, serving the ice machines and domestic purposes, are housed in the bulbous bow and a further two wing tanks forward. Eight thousand litres of freshwater held in the antiroll tank, positioned between the main and trawl decks in line with the aft side of the wheelhouse, is also available for use if required. These higher-than-usual fuel and freshwater capacities were requested by the owners to give greater flexibility when working west of Scotland.
At the end of her maiden trip, Audacious immediately showed the benefits of her design by sitting on her waterline and an even trim when moving from the Albert Quay to land some 50t of fish in the north harbour, after taking fuel and freshwater.
Advanced electronics equipment
The comprehensive array of electronic equipment, displayed on 28 flush-mounted 24in and 19in AG Neovo monitors, was supplied and commissioned by three local companies: Woodsons Marine Electronics, Furuno UK and Scanmar UK.
The majority of the screens, on which the arrangement of displays can be customised to suit the skippers’ preferences for the prevailing mode of operation, are arranged over two levels in the main forward console in the superbly crafted and finished wheelhouse.
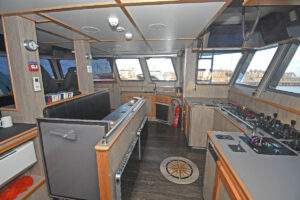
… installed in the superbly finished wheelhouse.
Two NorSap 2000 heated seats, displaying the vessel’s name on the headrests, flank a central island unit, on which the control unit for the Simrad autopilot and main Furuno radar is positioned.
Slim port and starboard wing consoles, formed as an integral part of the forward console, house duplicate sets of Lyngaa Marine electronic engine and propeller controls, and tillers for the Scan ApS steering gear.
An expansive fishing console, from which the skippers have full remote control of all deck machinery, is arranged across the aft end of the wheelhouse. A central office desk area serving the vessel’s catch-management and eLog systems backs onto the island console and the skipper’s seats. Hot drink facilities, together with a small fridge and sink unit, are arranged to starboard. Sola-Cure UK supplied the anti-glare blinds fitted to all the wheelhouse windows.
Fish detection on Audacious is handled by a Furuno FCV-2100 CHIRP fish-sizing echosounder and a SeapiX 3D multi-beam sonar. With the need to target only specific species due to quota and landing obligation requirements, both high-tech units provide the skippers with the highest level of information possible to determine what mix of species is within the area they are fishing, as well as the size and quantity of fish that could be expected to be caught.
Audacious has the distinction of being the first demersal vessel in the UK fleet to install SeapiX, providing a number of key features:
- Bathymetry mapping for the vessel and gear/net security
- Near-bottom fish extraction, with widest coverage on ground displayed in 3D and 2D environment
- Biomass/species percentage evaluation and selection in real time.
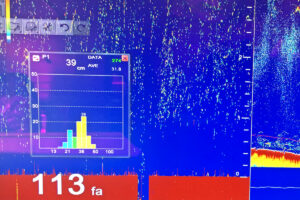
Marking haddock and counting 274 fish, at an average length of 32cm, on the Furuno FCV-2100 fish-sizing sounder, when Audacious ran fishing trials in the Hole of the Broch.
Biomass detection is extracted from single targets of as small as 7cm. Advanced real-time processing allows the skippers to build their own ‘fish species categories’, with their own relevant unique responses. This provides the skippers with both 2D and 3D mapping, displaying both the location and the percentage mix of fish species within the area they are towing, in real time.
Incorporating TruEcho CHIRP technology, Furuno’s advanced FCV-2100 1kW broadband (100kHz +/- 30kHz) fish-finder employs a five-split beam transducer that facilitates multi-directional detection. The transducer divides its elements arranged in four segments, enabling it to detect the accurate location of individual fish, and correctly measure the strength of the returned echo. The short pulse width (down to 0.04ms) of the FCV-2100 ensures high-resolution echogram and high-precision fish-size histogram.
Details of the vessel’s location are processed by two Furuno GP33 GPS navigators, and vessel heading is provided by Furuno SC-50 satellite and Hemisphere GPS gyro compasses. Positioning data received is interfaced to MaxSea TimeZero, Olex 3D and Sodena Turbowin plotting systems. A FishSafe unit is also fitted.
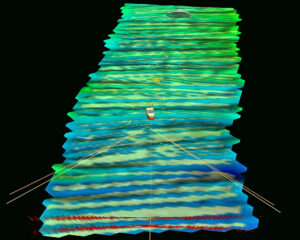
… and on Audacious’ track in 3D mode.
The main radar is a Furuno FAR 2127 X-band set, backed up by a Furuno DRS6AX unit.
Steering is handled by a Simrad AP70 autopilot system c/w three follow-up units and rudder indicators. A Furuno BR-500 watch alarm system incorporating motion sensors is also fitted.
Communications and safety equipment includes Sailor 6310 GMDSS radio telephone, Icom, Sailor and Entel VHFs, Furuno NX700 Navtex, Jotron TR-8000 Class A AIS, Jotron TRON 60S EPIRB, e-SEA 60Ka internet communications system, and e-SEA 80 satellite TV system.
An extensive CCTV system, including 17 high-resolution cameras and a 16-way DVI matrix switcher, was installed by Woodsons throughout Audacious.
All the processing units, computers and power supplies serving the electronic displays and equipment in the wheelhouse are housed in a walk-in instrument compartment on the deck below the wheelhouse, adjacent to the skipper’s cabin and opposite an electrical room.
Jackson Trawls delivers double-bosum pair-seine
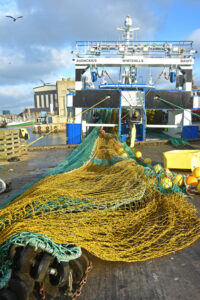
Audacious pulls on the new design of double-bosum…
Peterhead netmaker Jackson Trawls maintained its longstanding relationship with skippers David Gatt and Barry Reid by supplying the complete fishing gear and chandlery packages that Audacious is now using to good effect.
In response to a request from the owners for a pair-seine that, in addition to the customary high-standing headline that pair-seiners favour to take gadoid fish, would also provide increased ground contact, Jackson Trawls designed and made a double-bosum hopper seine.
The skippers were extremely pleased with the initial performance of this net, the first of its type to be used by a Scottish pair-seiner. It yielded good results on all species, including increased numbers of groundfish, on the first two trips. Intended for use on semi-clean ground, the double-bosum net features extended wings, and measures 400ft on the fishing line. Rigged on 8in- and 10in-diameter hoppers, the net has 610 x 8in meshes in the fishing circle, and is consistently giving a headline height of over five fathoms.
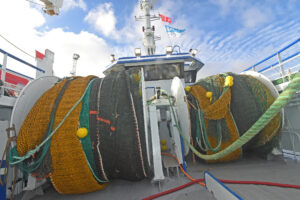
… made by Jackson Trawls of Peterhead.
When targeting fish lying on harder bottom, Audacious uses a heavy-rigged hopper pair-seine. Built with 12in meshes in the top and 8in meshes on the bottom, this net, which has 386 x 12in meshes in the fishing circle, is set on 130ft of ground gear made with 16in- and 18in-diameter hoppers.
Both nets are constructed with 210ft of 24mm Dyneema headline rope and 5mm Sapphire twine to reduce drag and fuel consumption, and 5mm double Sapphire codends are also fitted.
Jackson Trawls also supplied Audacious with four coils of 50mm- and 60mm-diameter VCU four-strand combination rope, 50 fathoms of 36mm-diameter heavy sweep wire and 600 fathoms of 24mm-diameter Bridon Dyform wire spooled on the core of the pair-seine winch.
Four sets of 30-fathom sweeps, comprising 26mm rubber legs and 18mm-diameter wire attached to the fishing line, were also made up by Jackson Trawls and delivered to Audacious at Fraserburgh.
Marble Automation
A key feature of Audacious is an alarm monitoring and control system (AMCS) custom-built to the owners’ specifications by Marble Automation of Urk, Holland.

An alarm monitoring and control system custom-built by Marble Automation of Urk is located on the central console between the NorSap skipper’s seats.
A 15in touch-screen control panel, mounted on the central console between the two skipper’s seats in the wheelhouse, is the focal point of the advanced system. Duplicate consoles are located in the engineroom and the engineers’ cabin.
All parameters of the main engine and associated systems, including defined high and low operating values, are constantly monitored and available to view on a dedicated engine page.
Coverage of the generators and gearbox is provided on similar all-embracing pages. All navigation and deck lights can be switched on and off via the control screens, as well as being continually monitored.
Readings of all fuel/lube/hydraulic oil, freshwater, and antiroll tanks are also available on another bespoke screen, from which the fuel pumps can be operated.
Similar provision is made for the bilge compartments, alarms and pumps.
Scanmar net- and catch-monitoring
Fishing efficiency on Audacious (and Faithlie) is optimised by the latest range of Scanmar net-monitoring receivers, software and sensors, supplied, installed and commissioned by Scanmar UK of Peterhead, which has a longstanding association with the owners. These sensors can also be used as distance sensors if Audacious was to single or twin trawl, as they would display door spread, door depth from the surface and door angle (door pitch and roll).
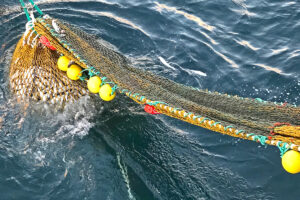
Four Scanmar catch sensors, two of which give real-time temperature readings, are attached to the pair seines Audacious is working, as part of the vessel’s complete net monitoring system supplied by Scanmar UK.
Audacious is the first demersal boat to install Scanmar’s new generation of WDR-42 receivers and a full Windows-based modular system. The new units receive constantly updated data from a variety of sensors, including new wing end sensors, which – in addition to spread across the mouth of the net – allow the skippers to gauge ground contact, and whether or not the toes are lifting, by incorporating depth sensors.
A flow sensor fitted on the headline provides information on net symmetry, and the speed of water flow through it. Two of the four catch sensors provide real-time temperature readings on the seabed, enabling the skippers to pick up and follow thermoclines that proved productive on previous tows, data from which can be stored to build up historic track records.
A Scanmar TrawlEye sounder provides information of headline height from the top of the trawl to the seabed, the opening of the trawl from footrope to headrope, and clearance from seabed to footrope. The density of fish at the mouth of the trawl is displayed with a value from 0-9 and colour density.
The new Scanmar SCU control unit enables a skipper to click and drag each sensor on the main screen display. In addition to being time-saving, the SCU control unit, the three previous installations of which were on the midwater trawlers Altaire, Ocean Star and Voyager, also avoids frequency collision by automatically making any necessary changes.
AUDACIOUS BF 83
DETAILS
Owners: David Gatt, Barry Reid and Billy Gatt – Audacious LLP, Whitehills
Designer/boatyard: Macduff Shipyards Ltd
Agent: Don Fishing, Peterhead
DIMENSIONS and CAPACITIES
Length overall: 27.80m; Length BP/reg: 23.95m; Beam: 8.60m; Depth moulded (to trawl deck): 6.40m; Draft: 5.6m; Tonnage: 358t gross; Fuel: 48,000 litres; Freshwater: 32,000 litres; Lube oil: 750 litres;
Hydraulic oil: 2,000 litres; Fishroom: 1,300 boxes; 8t ice
ENGINEROOM
Main engine: Caterpillar 3508C of 577kW @ 1,200rpm driving through a Heimdal HGH595F 9.438:1 reduction gearbox to a 2,800mm-diameter four-bladed CP propeller Speed: 10 knots
Auxiliary engines: 2 x Caterpillar C7.1 of 150kW @ 1,500rpm driving 150ekW 415/3/50 generators
Bow thruster: BOPP 150kW
Fuel oil/water and hydraulic oil/water separators: CC Jensen
Bilge, deck and fuel transfer pumps: Azcue
DECK MACHINERY
Suppliers: BOPP, Boulogne sur Mer, France and EK Marine, Killybegs
1 x pair trawl winch 24t, capacity 1,000m of 24mm- and 380m of 28mm-diameter wire and 8,880m of 50mm-diameter combination warp; 2 x split trawl winches 18t, capacity 1,650m of 24mm-diameter warp; 2 x split net drums 15t/16.7m³; 2 x bagging drums 6.5t/2.9m³; 1 x Gilson winch 10t; anchor windlass and mooring winch 2.5t; 1 x fishroom winch 3t; EKM 624 continuous-slew knuckle-boom crane 1.2t @ 10m c/w landing winch and remote control
FISH-HANDLING/FISHROOM
Fish-handling system: VCU Urk, Holland; Gutting machines: KM Fish Machinery AS, Denmark – 2 x KM5; Fishroom chilling: Nordkøl, Hanstholm; Ice machines: Buus – 2 x 4.5t
ELECTRONICS
Suppliers: Woodsons Marine Electronics, Aberdeen, Furuno UK, Fraserburgh, and Scanmar UK, Peterhead
Fish detection
Furuno FCV-2100 CHIRP split-beam fish-sizing echosounder; SeapiX 3D multi-beam/sonar system with real-time species mapping and identification; Scanmar monitoring system c/w new-generation WDR-42 receivers, TrawlEye sounder, wing end sensors with depth and angle, flow/symmetry, 4 x SS4 catch sensors, and new SCU control unit; Scantrol PairLink and iSYM system for auto pair-seining
Navigation
Furuno DRS6ANX and Furuno FAR 2127 X Band radars; 2 x Furuno GP33 GPS receivers; MaxSea TimeZero plotting systems; Olex 3D seabed mapping and Sodena Turbowin plotting systems; FishSafe unit; Simrad AP70 autopilot system c/w 3 x FU80 follow-up levers; Navitron NT920 DHR; Furuno SC-50 satellite compass; Hemisphere GPS gyro; Jotron TR-8000 Class A AIS; Furuno BR-500 bridge alarm system with motion sensors; Windsonic ultrasonic wind speed and direction sensor
Communications
Sailor 6310 150W GMDSS MF/HF SSB RT; Sailor 6215 DSC VHF; 2 x Sailor 6210 VHFs; Entel HT649 GMDSS hand-held VHF; Furuno Navtex NX 300; Phontech 3102 talkback system; Iridium Pilot satellite telephone; Jotron TRON 60 GPS EPIRB; TRON AIS SART; eSEA 60Ka internet communications system; e-SEA 80 satellite TV system; VCU catch-management electronic fishroom scales; E-Catch logbook software; CCTV system c/w 17 cameras and 16-way DVI matrix switcher
FISHING GEAR
Warp supplier: Jackson Trawls, Peterhead – 600 fathoms x 24mm-diameter and 50 fathoms x 36mm-diameter Bridon Dyform wire; four coils VCU 50mm- and 60mm- diameter four-strand combination rope; Net supplier: Jackson Trawls, Peterhead – hard ground pair-seine with 386 x 12in meshes in fishing circle, rigged on 130ft of 16in and 18in hoppers; semi-clean ground double-bosum pair-seine of 610 x 8in meshes in fishing circle, on 400ft of 8in and 10in discs
ACCOMMODATION
1 x two-berth skipper’s en suite and 5 x two-berth cabins
GENERAL
Engine controls: Lyngaa Marine ApS; Alarm, monitoring and control system: Marble Automation; Insurance: Sunderland Marine; Lifesaving appliances: Blue Anchor Fire and Safety, Fraserburgh; Paint system: PPG Coatings by PBP Services, Fraserburgh; Steering: Scan ApS; Wheelhouse seats: 2 x NorSap 2000; Wheelhouse windows and weathertight doors: Bohamet, Poland