Macduff Shipyards delivers 19m twin-rig trawler built at Buckie for local skipper Steven Clarke
Moray skipper Steven Clarke and the crew of Caledonia III are now twin-rig trawling on grounds to the north of Scotland from Scrabster harbour, reports David Linkie
Completing fishing trials from Buckie, where Caledonia III was built and fully fitted out by Macduff Shipyards, and sailing 48 hours later for the vessel’s maiden trip, were particularly poignant moments for Steven Clarke. As a local lad, he has fished from Buckie for his whole career, during which he has owned two trawlers sharing the registration BCK 35.
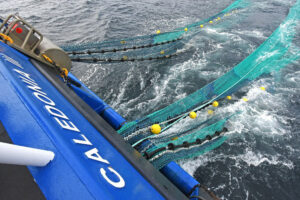
Caledonia III shooting away the 180ft letterbox-style twin-rig nets made by Faithlie Trawl…
Caledonia III is reported to have performed well on a four-day shakedown trip, fishing northwest of Noup Head, that yielded 400 boxes of fish. This total included a typical mix of megrim and monkfish, two of the main species Caledonia III is expected to land, when generally fishing from Orkney, west to the Butt of Lewis, including the Otter Bank.
Some of Caledonia III’s ground fish will continue to be bought by Jack Fish of Peterhead, thereby continuing skipper Steven Clarke’s association with Ian Jack, whose longstanding support is much appreciated.
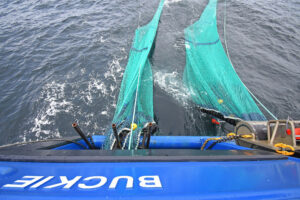
… for the first time, on fishing trials in the Moray Firth.
Insured by Sunderland Marine and working through Caley Fisheries (Fraserburgh) Ltd, Caledonia III is expected to follow a similar pattern of fishing to that which proved consistently successful for her predecessor, and paved the way for the new build.
“Caledonia III is everything I expected, plus a fair bit more”
Skipper Steven Clarke said: “Caledonia III is everything I expected, plus a fair bit more. Every member of Macduff Shipyards’ team at Buckie has done a superb job. The level of build quality, machinery installation and internal finish is of the highest order, and speaks for itself. Throughout the design and build programme, the level of co-operation was first-class.
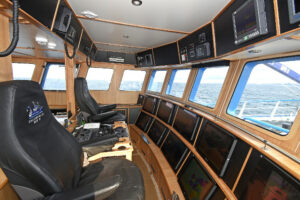
General view of the wheelhouse interior.
“Over the past 12 months, watching Caledonia III steadily evolve at a harbour where I grew up, and first went to sea from, has meant a lot to me. Buckie has a proud tradition of boatbuilding. After a gap of some 15 years, it is great to see new fishing boats being launched into the harbour again, at the same time as Macduff Shipyards continues with its major development plans, which will bring long-term benefits for Buckie, as well as for skippers in northeast Scotland and further afield.
“Building Caledonia III fulfils a lifetime’s ambition. While Caledonia II would have continued to serve me well, it is important to look to the future. Stocks are in good shape, consumer demand is strong, and Jonny Roe (mate and son-in-law) is keen and strongly motivated, so now was the time to reinvest.
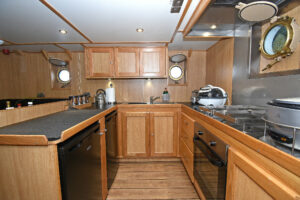
The well-equipped galley.
“Being fully shelterdecked, Caledonia III represents a major step up for us. For the first few trips at least, well-established working practices will need to be revised, and new ones established. However, at the end of the day, we expect to fish the new boat along similar lines to the previous one, working four- to six-day trips for most of the year from Scrabster, and grabbing a couple of days here and there, whenever the weather permits, during the winter months.
“If initial impressions are any guide, Caledonia III will prove to be a safe, efficient and economical boat in years to come”
“If initial impressions are any guide, Caledonia III will prove to be a safe, efficient and economical boat in years to come. Macduff Shipyards has done its job to the full; now the onus is on us to prove the capabilities of the new boat.”
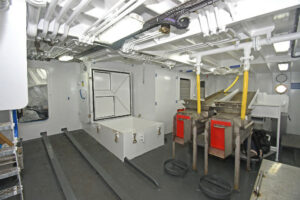
… and catch-handling arrangements amidships.
Designed in-house by Macduff Shipyards, before being built in its fabrication hall, Caledonia III has the distinction of being the first boat to be fully fitted out and run sea trials from Buckie for a local skipper since Herd & Mackenzie completed the 23m fully-shelterdecked wooden-hulled whitefish trawler Eleanda BCK 60 for Buckie skipper David Main in 1988.
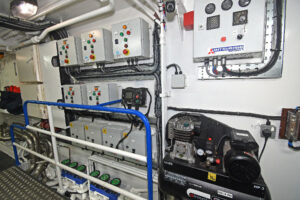
Electrical switchboards and box coolers are arranged across the fore end of the engineroom.
Caledonia III is the second build by Macduff Shipyards of a new model of under-ticket-length (16.49m) twin-rig trawler. Asteria BRD 250, handed over to Alasdair and Andrew Montgomery of Portree, Isle of Skye, after being built at Buckie and completed at Macduff, was the first (Fishing News, 9 October, 2017).
The hull was developed in conjunction with Macduff Ship Design Ltd, using computer-based CFD technology which helped to minimise overall resistance and ensure a clean flow of water to the propeller to maximise propulsion efficiency.
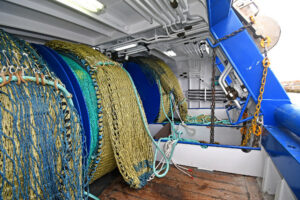
Two sets of split net drums are mounted on the hardwood-planked quarter.
Macduff Profilers, a division of the shipyard, supplied the steel kit, formed by CNC-controlled plasma torch from cutting information supplied by Macduff Ship Design Ltd.
The steel kit was subsequently fabricated in Macduff Shipyards’ large new modern boat hall at Buckie, at the same time as all engineroom and deck machinery were installed prior to launching.
The entire vessel is built from Lloyds Grade A steel, apart from the aluminium wheelhouse and aft mast.
Caledonia III has main dimensions of LOA 19m, registered length 16.48m, beam 7.2m, depth moulded 4.1m, draft 4.3m and GT 168t. Fuel capacity is 20,200 litres, and 10,000 litres of freshwater is carried.
Caledonia III features a fairly conventional arrangement. Below the main deck, the hull is divided into forepeak, fishroom, engineroom and accommodation cabin.
Under the full-length shelterdeck, a full-width bulkhead, incorporated into the aft end of the steel deckhouse, separates the forward fish-handling area from the net-handling area at the transom.
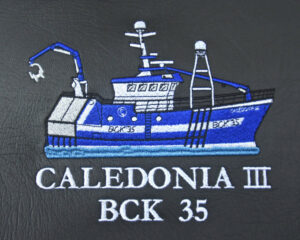
Profiles of Caledonia III are embroidered on the headrests of the NorSap skipper’s seats.
The connecting passageway gives access to the quarter via the top shelterdeck and an easy-access companionway is offset to the port rail. A heated glove/boot dryer, supplied by Dutch company Pronomar BV, is located at the fore end of the passageway, where the crew’s other deck clothing is stored when not in use.
In addition to oilskins, this includes mandatory hard hats and PFDs fitted with McMurdo Smartfind S20 personal AIS beacons, illustrating the importance placed on crew safety by skipper Steven Clarke.
A watertight steel bulkhead is fitted on the main deck, forward of the catch reception hopper, to create a separate winch room, which by eliminating greasy wires passing through the fish-handling area, enhances both catch quality and crew safety.
An additional dedicated walk-in steel compartment housing a Geneglace 1t ice machine and refrigeration machinery is arranged forward on the portside of the main deck.
The catch-handling area is kept free of excess water from the fishwashers by two deck sumps drained by electrically driven Azcue pumps.
Extending the full length of the deckhouse to starboard, the combined galley and messdeck, which includes a large table, giving the crew plenty of room to sit comfortably, is finished to the high levels of craftsmanship the boatyard is renowned for.

Caledonia III recorded an average top speed, into and with the tide, of 9.5 knots.
The usual range of electrical units in the galley, together with the separate washer and tumble dryer located in the passageway, were supplied by RD Downie of Fraserburgh, which as is customary with all Macduff builds, wired Caledonia III and manufactured the engineroom and wheelhouse electrical distribution cabinet boards.
The main accommodation cabin aft has been cleverly arranged to give a skipper’s three-berth en suite cabin to port and a five-berth cabin on the starboard side. Every opportunity has been taken to maximise locker storage and bench seating for the comfort of the crew, with most of the storage facilities incorporated along the sides of the passageway leading to the starboard cabin.

Developing 447kW @ 1,800rpm, the Caterpillar C18 ACERT main engine is coupled to a Reintjes 7.409:1 reduction gearbox.
Shower/toilet facilities are also arranged in the deckhouse. An additional toilet compartment is also accessible from the passageway on the port side.
Macduff Shipyards manufactured most of the deck equipment installed on Caledonia III, including the three-drum trawl winch positioned forward on the main deck in a dedicated self-contained compartment.
A Nilfisk SC UNO 5M-200 electric power-washer is also housed in the winch room, illustrating the emphasis skipper Steven Clarke places on maintaining catch quality on the main deck.
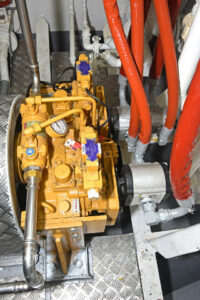
A Dongi clutched PTO, mounted at the fore end of the main engine, provides a net-retrieve system.
Rated 23.8t core pull, the winch is fitted with a Hägglunds CA140 compact drive motor. The winch barrels are spooled with 275 fathoms of 20mm-diameter compact trawl wire, supplied by Karl Thomson of Buckie.
Led up from the drums at nearly 45° to hooded rollers, the outer wires run across the top of the shelterdeck to a second set of sheaves positioned towards the aft corners of the wheelhouse, from where they are directed upwards towards hanging blocks mounted on a conventional trawl gantry. The middle wire runs under the wheelhouse floor, before leading upwards to pass over a roller incorporated into the transom rail, directly above a secure track for the safe storage of the middle roller.
The gear will usually be towed off the blocks in fine weather, and from Dyneema pennants attached to a central towing point on the trawl gantry in poorer conditions.
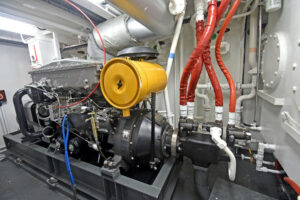
A Mitsubishi 6D24TC auxiliary engine runs the main hydraulics and a 48kW Mecc Alte 415/3/50 electrical generator.
Hardwearing UHMW-PE sheathing panels and strips, supplied by DockGuard, are secured to outer hull areas in line with where the trawl doors and middle roller are worked, to minimise abrasion, wear and paint discolouration.
Two sets of 2 x 7t split net drums, fitted with Hägglunds CA50 compact motors, are arranged side by side on the non-watertight wooden-decked quarter, in line with the customary transom shooting and hauling hatches, the lower edges of which are fitted with free-turning large-diameter rollers.
Thistle Marine Ltd supplied the MKB7 short-post crane with tilting 24in powerblock that is centrally fitted on the trawl gantry.
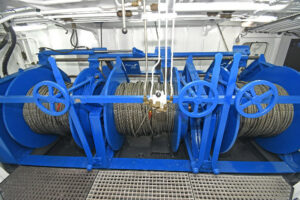
The three-drum trawl winch was manufactured by Macduff Shipyards.
The codends are taken aboard forward on the starboard side by a 5t Gilson winch serving a square-framed lifting gantry, arranged over a hydraulically operated hatch and a large-capacity reception hopper fitted with a sprinkler system.
After being released from the codend into the hopper, the catch is gravity-fed onto a table that leads aft. Standing with their backs against the side of the boat itself, the crew immediately sort the results of a tow off the table into baskets, which are then placed on deck.
As soon as the hopper is clear, the crew begin to gut the catch, species by species, as they are emptied out of the baskets onto the selection table. Gutted fish are then placed on one of two drop-in chutes for delivery to two fishwashers. On release from the washers, ground fish are then hand-washed, to remove any remaining offal from the gills and mouths, from a basket placed on a raised stand, before filled baskets are moved forward for weighing and labelling using a VCU catch management system positioned forward to port.
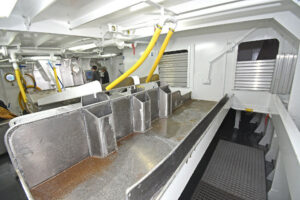
Catches are gravity-fed from the reception hopper onto the selection/gutting table.
Similar to the catch arrangements that worked well on Caledonia II, this system is designed to deliver optimum levels of catch quality, particularly for megrim and cod which, because of their softer flesh, can bruise easily. Gutting by species also promotes greater efficiency for the crew at every stage of the catch-handling process, from the selection table to boxing in the fishroom.
Although Caledonia III is not expected to target prawns on a regular basis, a rectangular two-basket chilled prawn dip tank is positioned forward of the deck casing, in close proximity to the twin washers.
The fishroom has a working capacity of around 650 stacker boxes, supplied by Box Pool Solutions.
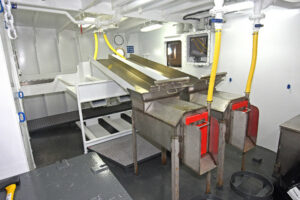
Drop-in chutes are used to deliver gutted fish directly into two washers.
James Elrick of E&R Refrigeration, Fraserburgh, installed the chilling system fitted on the deckhead and engineroom bulkhead. The cooling plant for this, together with a 1t Geneglace flake ice machine, is housed in a separate walk-in compartment arranged on the main deck to starboard, between the winch room and the reception hopper.
Stacks of boxes, pulled forward to the deck hatch by a small hydraulic winch, are lifted ashore from the fishroom using a Thistlelift MFB8 stiff-boom landing crane and 1t landing winch.
The degree to which the owners, in close liaison with the builders, have endeavoured to ensure that Caledonia III will be an efficient and economical boat to operate well into the future, is reflected by the combination of centreline machinery in the well-arranged engineroom.
Caledonia III is powered by an electronically controlled Caterpillar C18 ACERT main engine, supplied by Finning UK Ltd.
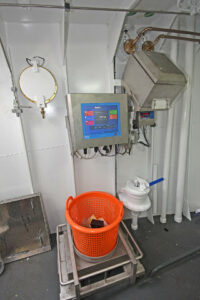
A set of Marel electronic scales and a VCU catch management system are located on the portside of the main deck amidships.
Developing 447kW @ 1,800rpm and solely dedicated to propulsion duties, the main engine drives a 2,000mm-diameter four-bladed fixed-pitch Wärtsilä propeller turning in a modern high-thrust low-drag Wärtsilä nozzle through a Reintjes 7.409:1 reduction gearbox.
The remaining stern gear package, including a triple rudder, was designed in-house by the shipyard and manufactured by Macduff Precision Engineering on CNC machines. Sea trials demonstrated encouraging results with this stern gear package, with an average top speed of 9.5 knots and indications of economical towing performance.
Caledonia III was using 50-55 litres of fuel at 1,275-1,350rpm when towing at 2.8-3 knots in 60 fathoms of water, on fishing trials in the Moray Firth.
A Mitsubishi 6D24TC variable-speed auxiliary engine (182kW @ 1,500rpm) is mounted on the port tank top. In addition to supplying the vessel’s main hydraulic system through a clutched pump connected directly to the engine’s flywheel, this auxiliary engine also drives a 48kW Mecc Alte 415/3/50 generator. A similarly-rated generator is driven by a Mitsubishi S4KT engine.
A back-up hydraulic net retrieval system, in the form of a clutched Dongi PTO unit, is driven off the front end of the main engine.
Cooling for all three engines and the hydraulic system is provided through Blokland box coolers arranged across the forward end of the engineroom. Stainless steel piping is used extensively throughout the engineroom.
Two electrically driven 150-amp 24V alternators from Transmotor Aps provide DC supplies to the four sets of batteries fitted – one for each engine and an emergency bank. A Victron 24V battery charger and inverter is also fitted.
Two wing tanks in the engineroom, together with a daily service tank, can carry 20,200 litres of fuel.
A Hardy T550 hydraulic bow thruster is fitted to give Caledonia III enhanced manoeuvrability when operating in restricted spaces.
Modern and well-equipped wheelhouse
Woodsons of Aberdeen supplied, installed and commissioned the electronics package fitted in the wheelhouse of Caledonia III. This was custom-designed in line with the owners’ requirements.
Most of the eight 19in Neovo and two 24in X-type glass-front screens, displays for which are selected in conjunction with an eight by eight-way matrix switch, are flush-mounted in the main forward console.
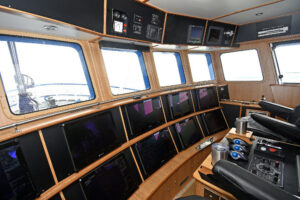
Woodsons supplied a comprehensive array of electronics equipment.
Two NorSap skipper’s seats, which have profiles of Caledonia III embroidered onto the headrests, flank a central console housing the autopilot controls, forward of a chart table arranged on top of storage drawers, together with the electrical switchboard panels.
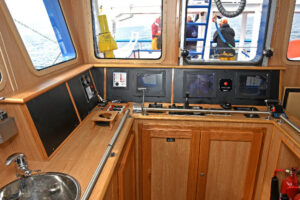
The fishing console is offset to starboard.
The trawl console is arranged in the aft starboard corner, ensuring that skipper Steven Clarke retains full sight of the gear as the codends are taken forward before being hauled to the transom again.
The wheelhouse door leading onto the shelterdeck is positioned to port of the vessel’s centreline, next to a small desk area.
Details of the vessel’s location are processed by two Furuno GP39 GPS receivers, and vessel heading is provided by a Hemisphere satellite compass. Positioning data received is interfaced to an Olex seabed mapping system and two Sodena Easywin plotters, supporting a combination of Tide T8 charts, AIS and ARPA tracking. Two Koden radars also provide ARPA and AIS tracking.
Vessel steering and navigation are taken care of by a Navitron NT921 MKII digital autopilot. A secondary jog steering lever, along with a duplicate set of Kobelt engine controls, is positioned at the trawl console, as well as aft on the shelterdeck, near the controls for the powerblock crane.
Bottom-sounding and fish detection duties onboard Caledonia III are undertaken by a Hondex HE-7300Di dual-frequency (50/200kHz) sounder, the ground hardness output of which is interfaced to the dual-screen 3D Olex plotting system.
Communications and safety equipment include a JRC JSS 2150 150W GMDSS radio telephone, 2 x Icom M506 DSC and Sailor 6210 VHFs, Entel HT649 handheld GMDSS VHF, Jotron TR-8000 Class A AIS, Jotron TRON GPS, and a NASA Marine Easy Navtex.
Satellite communications on Caledonia III, including the E-Catch e-Log system relaying information from the VCU catch management system, are handled by an eSEA 60Ka internet system and eSEA 60 satellite TV system.
Woodsons also installed an extensive CCTV system on Caledonia III. Images from 11 HD cameras, together with an underwater video camera monitoring the propeller and triple rudder, provide comprehensive coverage across the quarter and trawl gantry, catch-handling area, winch, engineroom and fishroom, in addition to fore and aft aerial views from the top of the radar mast.
Scanmar double-distance and net-symmetry monitoring
Skipper Steven Clarke is using a Scanmar ScanMate double-distance net-monitoring system to provide optimum levels of fishing efficiency, in terms of both gear spread and fuel economy.
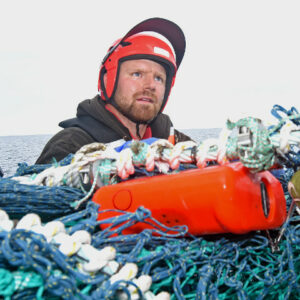
Jonny Roe fitting the headline flow sensor.
Information supplied by three Scanmar SS4 sensors mounted on the trawl doors and middle roller, operating via the popular ScanMate bridge system, provides constant numerical and graphical updates of the openings of the two nets relative to the roller, and how the central weight is positioned in relation to the trawl doors.
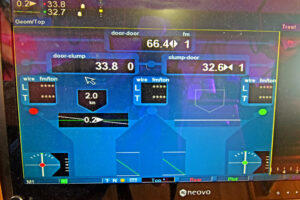
The main display from the Scanmar twin-rig trawl-monitoring system, showing door-to-door and clump-to-door spreads and net symmetry.
In a fishery where maximising gear spread and symmetrical net geometry is of paramount importance, the information provided enables the position of the middle clump to be adjusted whenever the need arises, by eliminating any doubt in the mind of the skipper about whether the clump is in line, in front of or behind the trawl doors.
Scanmar UK of Peterhead also supplied a headline flow sensor, enabling Steven Clarke to constantly monitor the symmetry of his gear.
Faithlie Trawl twin-rig groundfish nets
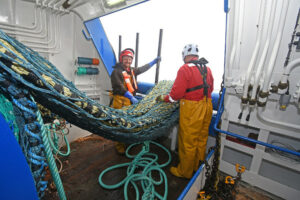
Shooting away the starboard codend…
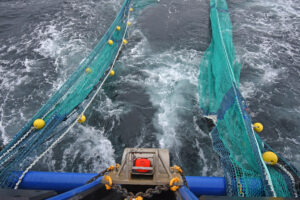
… and the 180ft letterbox twin-rig trawls…
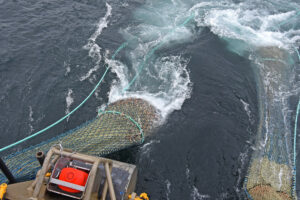
… before hauling back the gear…

… and taking the bag aboard on completion of successful fishing trials.
Caledonia III sailed from Buckie last month to fish her first trip with two sets of Faithlie Trawl twin-rig trawl customised groundfish nets wound on the drums.
Willie Hepburn and his team at Faithlie Trawl made two letterbox-style 200ft trawls rigged on 6in- and 8in-diameter discs. The nets are specifically designed to catch target species like megrim and monkfish.
Faithlie Trawl also supplied two 180ft standard scraper nets, rigged on a combination of 6in and 8in ground gear.
Both types of heavily constructed twin-rig gear, which are well-proven to keep their shape long-term and therefore minimise maintenance, are similar to those which performed successfully on Caledonia II, so skipper Steven Clarke had no hesitation in ordering the same style of net for the new boat.
Caledonia III uses 60 fathoms of 28mm-diameter six-strand combination warp and 15 fathoms of 20mm-diameter wire rubber legs – together with short lengths of chain, strategically positioned to indicate if the gear is in contact with the bottom as expected – to connect the twin-rig gear to a 1,000kg roller clump, manufactured by Macduff Shipyards, and a set of Thyborøn Type 11 66in trawl doors.
The 3 x 275 fathoms of 20mm-diameter compact trawl wire spooled on the barrels of the three-drum trawl winch came from Karl Thomson of Buckie.
Continuing large-scale investment by Macduff Shipyards at Buckie
Work on an extensive project to create modern slipping and refit facilities, that will enable Macduff Shipyards to take boats up to 800t and 40m, is progressing well at Buckie, as part of a fully integrated development. This will bring long-term benefits for vessel maintenance and refit work, together with new builds.
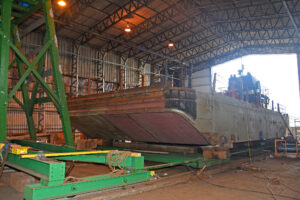
Replating work in progress in the repair hall on the freshwater tanker Albatross.
In the latest in a series of large-scale improvements that Macduff Shipyards has initiated since opening a division at Buckie, contractors are currently constructing an extensive area adjacent to the main slipway, which on completion will accommodate a new side-slipping cradle from the refurbished main slipway.
Incorporating hydraulically operated side arms to hold boats in place, the cradle has been custom-designed to give maximum operational flexibility when side-slipping vessels. The two independently operated cradles will have the capacity to side-slip two vessels up to 15m and 24m LOA, as well as a bigger boat up to 40m when they are linked together, to give three retaining stanchions along either side of a vessel.
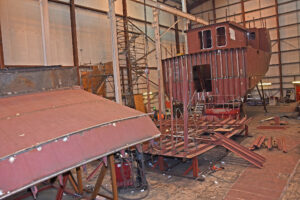
The hull of a 19.2m scalloper for Whitelink Seafoods of Fraserburgh, under construction in Macduff Shipyards’ new boat hall at Buckie.
When used in the single mode, the new facility will have the capability to handle some of the largest fishing vessels in the UK fleet, including the stern trawlers like Endeavour IV and Venture III, as well as the bigger class of beam scallopers.
Earlier this year, the first stage of renovation work on the large repair hall, situated to the south of the main slipway, was completed. Since taking over the premises and slipways, previously owned by Buckie Shipyards and before that by Herd & Mackenzie, Macduff Shipyards has created 30 jobs at Buckie, including a number of apprenticeships, in a coastal town that for decades was synonymous with building fishing boats.
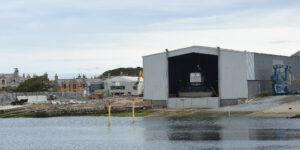
Macduff Shipyards’ expansive new slipping and refit facilities at Buckie are expected to be fully operational in spring 2019.
The repair hall has an interesting history, as it was originally an RAF aircraft hangar at nearby Boyndie. On securing the contract to build minesweepers for the Royal Navy at Buckie in the early 1950s, which stipulated that the boats had to be built in secure premises, Herd & Mackenzie dismantled two hangars and rebuilt them on either side of the slipway. This novel solution led to the building of the 110ft HMS Greetham, followed by the 158ft HMS Monkton and Woolaston in 1955, and the 153ft HMS Lewiston four years later.
In addition to renewing the cladding on the north side of the repair hall, a watertight ‘cofferdam’ style door was fabricated to fit across the head of a second slipway, after this dedicated facility was fully refurbished and strengthened. New internal rails and a slipping winch were also fitted to the repair hall, at the same time as all internal service supplies and lighting were renewed.
On completion of all renewal work to the repair hall, the Invergordon-based 22m x 9m freshwater tanker Albatross was slipped and winched up, as the Macduff Shipyards Buckie team started to carry out a major refit. Now nearing an advanced stage of completion, this work includes renewing the deck and bow plating. A wide range of mechanical work has also been carried out, including refurbishing the tail shafts and rudder stocks. Albatross will then be fully repainted before being refloated.
Two buildings located in close proximity to the main slipway have been fitted out as well-equipped joinery and light engineering/fabrication workshops, after the adjoining premises were fully refurbished internally.
Similarly, an already well-stocked stores facility is now fully up and running. In addition to being of huge benefit in relation to new builds and vessel refitting, this is already proving popular with local and visiting skippers fishing from Buckie.
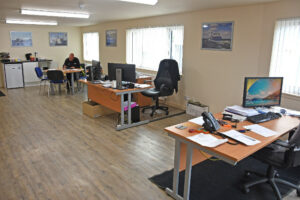
Macduff Shipyards’ new open-plan office accommodation at Buckie.
The original office accommodation has been fully renewed internally, and is now being used by Stuart Mack and John Watt Jr, general managers of Macduff Shipyards’ Buckie division.
While Caledonia III ran sea trials last month from Buckie, hull fabrication of a 19.2m scalloper for Whitelink Seafoods of Fraserburgh continued to forge ahead in the main building hall.
Designed to work 10 dredges aside, in conjunction with hydraulically operated tipping doors and side conveyors, the new scalloper will feature a Mitsubishi S6R2 main engine, Masson 7.063:1 reduction gearbox, 2,200mm-diameter propeller and triple rudder. Mitsubishi 6D24 and S4KT auxiliary engines will also be fitted.
By successfully bringing boatbuilding back to Buckie, Macduff Shipyards is creating employment in a traditional fishing community that has long been synonymous with new fishing boats going on sea trials. In not so distant days, three boatyards, Herd & Mackenzie, Jones, and Thomsons, were situated around the harbour.
With further new builds scheduled, including vivier-crabbers, twin-rig trawlers and pair-seiners, and the new vessel refit facility expected to be fully operational in the spring of 2019, the commitment by Macduff Shipyards means that Buckie can once again look forward to a succession of new boats leaving the harbour for fishing trials.
Third Caledonia in 25 years
As her name indicates, Caledonia III is the third boat Steven Clarke has been associated with in 25 years.
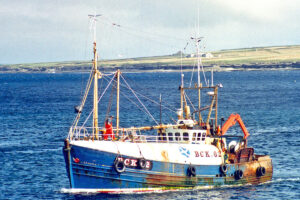
Seagull started off skipper Steven Clarke’s career in the wheelhouse.
He first skippered his father Edwin Clarke’s boat Seagull BCK 62, a 55ft wooden-hulled trawler, built by Herd & Mackenzie for Kenneth Watt of Macduff in 1971, and bought from Michael Kirwin of Clogherhead in 1987. Steven Clarke then acquired the first Caledonia in 1993.
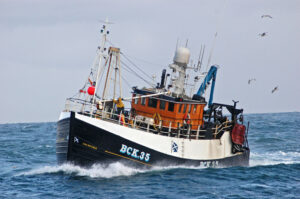
Steven Clarke’s first Caledonia.
This 18.2m wooden-hulled trawler was built by Herd & Mackenzie as Unity BCK 35 in 1986, for local skipper John Flett. Now owned by Mallaig skipper John McQueen as Mareather OB 503, Caledonia was renamed Aubretia BCK 32 when Steven Clarke sold the boat to Tarbert in 2007.
Pleiades BF 155 became Caledonia II BCK 35 in 2007, when Steven Clarke bought the 16.7m steel-hulled twin-rig trawler from Phillip and Gary Hepburn.
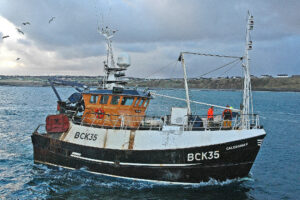
Caledonia II.
Together with Antaries BF 27 and Holly B II FR 29, Pleiades was one of three twin-rig trawlers to be completed by Buckie Shipyards in 2001, after the hulls of these vessels were built in Russia and transported by sea to Buckie.
As Caledonia III was nearing completion, Caledonia II was bought by Barra skipper Angus MacLeod and renamed Grinan Øir CY 155, as a replacement for the 19.8m wooden-hulled Aquarius CY 34, which was sold to Portavogie.
CALEDONIA III BCK 35
DETAILS
Owners: Steven Clarke and Caley Fisheries (Fraserburgh) Ltd
Designer/boatyard: Macduff Shipyards Ltd
Agent: Caley Fisheries (Fraserburgh) Ltd
DIMENSIONS and CAPACITIES
Length overall: 19m; Length reg: 16.48m; Beam: 7.2m;
Depth moulded: 4.1m; Draft: 4.3m; Tonnage: 168t gross;
Fuel: 20,200 litres; Freshwater: 10,000 litres; Lube oil: 450 litres; Hydraulic oil: 1,600 litres; Fishroom: 650 boxes; 8t ice
ENGINEROOM
Main engine: Caterpillar C18 ACERT of 447kW @ 1,800rpm driving through a Reintjes 7.409:1 reduction gearbox to a 2,000mm-diameter four-bladed propeller. Speed: 9.5 knots
Auxiliary engines: Mitsubishi 6D24TC of 182kW @ 1,500rpm driving deck machinery hydraulics through a clutched pump and a 48kW Mecc Alte 415/3/50 generator; Mitsubishi S4KT of 54kW @ 1,500rpm driving a 48kW Mecc Alte 415/3/50 generator
Bow thruster: Hardy T550 hydraulically driven 67kW
Fuel/oil filters/separator: CC Jensen
Bilge/deckwash and deck sump pumps: 4 x Bombas Azcue SA electrically driven
Power washer: Nilfisk SC UNO 5M-200 electric power washer
DECK MACHINERY
Suppliers: Macduff Shipyards Ltd
1 x three-drum Macduff trawl winch 23.8t; 2 x Macduff split net drums 2 x 7t; Macduff Gilson winch 5t; Thistle MKB7 kinked-boom short-post crane SWL 1400kg 5.5m and Thistle 24in tilting with powerblock head; Thistlelift MFB8 stiff-boom crane and Thistle Marine landing winch 1t; 0.5t hydraulic fishroom winch
FISH HANDLING/FISHROOM
Fish handling system: Macduff Shipyards Ltd;
Fishroom chilling: E&R Refrigeration Ltd, Fraserburgh;
Ice machine: Geneglace, 1t per day
ELECTRONICS
Suppliers: Woodsons of Aberdeen and Scanmar UK, Peterhead
Fish detection
Hondex HE-7300Di dual-frequency (50/200kHz) sounder with hardness output; Scanmar ScanMate double-distance twin-rig net-monitoring system c/w Scanmar SS4 master door and clump sensors and headline flow sensor
Navigation
Koden MDC7006 and Koden MDC941A radars; Olex 3D seabed mapping system; 2 x Sodena Easywin plotting systems c/w AIS, ARPA, tides and hardness module; 2 x Furuno GP39 GPS receivers; Navitron NT921 MKII autopilot c/w NT920 digital heading repeater and NT920 non-follow-up lever; Hemisphere satellite compass; Ultrasonic wind speed and direction sensor
Communications
JRC JSS 2150 150W GMDSS MF/HF SSB radio telephone; 2 x Icom M506 DSC VHF; Sailor 6210 VHF; Entel HT649 GMDSS handheld VHF; Phontech 3100 five-way talkback system; Jotron TR-8000 Class A AIS; NASA Marine Easy Navtex; Jotron TRON GPS; eSEA 60 satellite TV system; eSEA 60Ka internet communications system; VCU catch management system; E-Catch E-Log system
FISHING GEAR
Warp supplier: Karl Thomson, Buckie – 3 x 275 fathoms of 20mm-diameter compact trawl wire; Net supplier: Faithlie Trawl, Fraserburgh – 2 x 200ft twin-rig letterbox trawls rigged on 6in and 8in discs and 2 x 180ft twin-rig scraper trawls rigged on 6in and 8in discs; Trawl doors: Thyborøn Type 11 66in 560kg; Middle roller: Macduff Shipyards – 1t
ACCOMMODATION
Skipper’s three-man cabin with en suite, and five-man cabin
GENERAL
Engine controls: Kobelt; Insurance: Sunderland Marine; Lifesaving appliances: Blue Anchor Fire & Safety Ltd, Fraserburgh; Crew’s PPE: Caley Fisheries, Fraserburgh; Paint system: International Paints; Steering: Tenfjord 100; Wheelhouse seats: 2 x NorSap 1500; Windows: HK Van Wingerden & Zn BV, Holland