Karstensens-built Shetland 75m midwater trawler features MacGregor electric-drive deck machinery
Skipper Davie Hutchison and the crew of the Whalsay midwater trawler Charisma LK 362 started to prove the new boat’s fishing credentials in December with two quick-fire trips in close proximity to Foula, west of Shetland, reports David Linkie. Photos: Ivan Reid and Sydney Sinclair
After spending 24 hours in Symbister harbour, when Charisma was warmly welcomed home to Whalsay, the vessel headed south to Lerwick to complete rigging out, having already undertaken successful fishing trials from Skagen. Having taken 800t of mackerel on the first trip, Charisma returned to Whalsay the following weekend to shelter from a 60-knot northwesterly gale, before returning to sea to take a second similar shot.
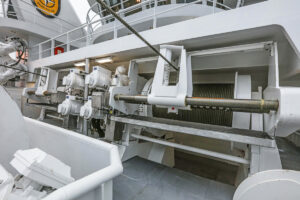
The 90t split trawl winches and the rest of the deck machinery are driven by electric motors…
The skipper and crew expressed their full satisfaction with the efficiency of the vessel’s engineroom and deck machinery, fish pumping and storage systems, and electronics equipment, together with the well-matched fishing gear.
This smooth start highlights the forward thinking and vision of everyone who contributed towards the end result of a design and build project that the Charisma Fishing Company initiated by contacting Karstensens shipyard in 2017.
Enhancing catch quality, fishing efficiency, and crew and vessel safety were cited as the main reasons for skipper Davie Hutchison and his partners taking the decision to order a new vessel to replace her 16-year-old predecessor of the same name, which was sold to Iceland in 2018.
Although just 4m longer, the new Charisma bears little resemblance to the previous one, not least in terms of significantly increased freeboard and by pumping pelagic fish over the stern – a first for the owners.
With state-of-the-art catch-handling, refrigeration and landing systems, propulsion technology that produced a top speed of 18.5 knots on acceptance trials from Skagen, and the latest wheelhouse electronics, supplied by H Williamson & Son of Scalloway, Charisma showcases the constant advancement in the design and specification of midwater vessels.
After completing two short trips, skipper Davie Hutchison said: “Hitting the ground running underlines the reliability and quality that Karstensens is renowned for delivering, and deservedly so.
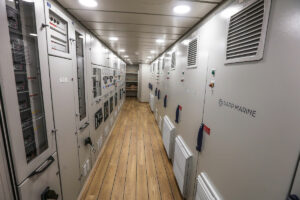
… remotely operated through cabinets in a dedicated room on the main deck.
“From the initial contact, every single member of Karstensens’ team has been superb to work with. At every stage of the design and build programme, the level of professional co-operation and friendly support we have received has been exceptional. The layout of the boat, together with the quality of workmanship, more than speaks for itself. While the level of finish in the internal accommodation areas is self-evident, it is fully matched throughout the boat by the equally impressive pipework.”
General arrangement
Designed in-house by Karstensens, Charisma features three continuous decks – main, shelter and boat – together with a sleek forecastle deck housing the anchor windlasses, mooring platforms/winches and two 80t anti-roll tanks.
Of 75m LOA and 67.2m registered length, Charisma’s round bilge hull has a beam of 15.3m, a shelterdeck depth of 9.2m, and a scantling draught of 8.5m. After being built to DNV-GL +1 Fishing Vessel – Hull: Ice-C class at the Remontowa shipyard in Gdansk, Poland, the hull was towed to Skagen for machinery installation and fitting out.
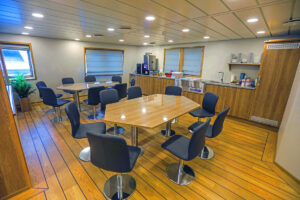
The spacious messdeck…
With a capacity of 2,311m³, Charisma’s 11 RSW tanks are arranged from forward in four tiers of three, two, two and four. The two middle tiers are positioned adjacent to the hull sides, to create a large central area in which the vessel’s RSW pumping system, refrigeration machinery and vacuum landing plant are housed over three decks amidships.
Below the main deck, the hull is subdivided into forepeak seawater ballast tank, sonar compartment, azimuth thruster room, forward insulated RSW tanks, refrigeration compressors, aft insulated RSW tanks, engineroom, laundry and aft tanks.
At main deck level, the arrangements from forward are forepeak, upper thruster room, RSW trunk section, vacuum landing/refrigeration plant rooms, aft RSW trunking, engine control room/electrical rooms/five single-berth cabins (starboard), engineer’s workshop (port), steering gear compartment and two net stores.
Layout on the shelterdeck consists of forepeak, electrical control room, workshops, tank deck with loading pipes for the RSW tanks, pumping/vacuum landing control room, two single and two twin-berth cabins and hospital cabin, crew deck wardrobe, deck store/workshop and trawl deck.
The boat deck is arranged with the forecastle housing the anchor/mooring winches, hydraulically operated mooring platforms and integrated roll damping tank. The fish/seawater separator forward of the accommodation casing is surrounded on three sides by a central deckhouse, the starboard side of which houses a fish-sampling room.
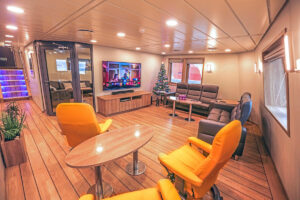
… and adjoining day lounge.
The superbly finished messdeck, in which two hexagonal tables are arranged, is positioned in the starboard side of the deckhouse, adjacent to a large day room and a smaller leisure room to port.
Cook Roy Huntley has a wide range of modern equipment available to use in the starboard stainless steel galley, which leads across the beam to the customary walk-in dry provisions store, together with separate fridge/freezer rooms, which can also be accessed off the boat deck, where a garbage room is also situated.
A further four single-berth ensuite cabins are arranged on the deck above the day areas.
Engineroom
Main engine power on Charisma is developed by a MAN 12V32/44CR-TI (common rail/long stroke) tier II-compliant propulsion unit that develops 7,200kW @ 750rpm and drives a Brunvoll Volda 4,200mm-diameter four-bladed CP propeller system housed in a high-performance fixed nozzle through a Brunvoll Volda two-step gearbox. Respective step 1 and step 2 reduction ratios of 5.77 and 7.14 give propeller speeds of 130rpm and 105rpm.
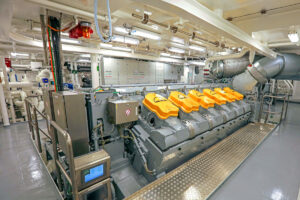
Charisma’s MAN main engine develops 7,200kW @ 750rpm.
This combination of centreline machinery, in tandem with the streamlined underwater hull lines, enabled Charisma to return an average top speed of 18.5 knots on engine trials, underlining the extent to which the design of this class of vessel has advanced in recent years.
A PTO on the gearbox drives an AvK Cummins shaft generator delivering 3,000kWe @ 1,200rpm.
Further electrical power on Charisma, to meet the requirements of the deck machinery, is provided by two Caterpillar 3512B engines. Generating 1,570kWe each, the auxiliary engines are housed in a soundproofed compartment to port in the engineroom.
Two Caterpillar C9 harbour/emergency gensets of 250kWe are located in the forepeak.
The vessel’s electrical power system is fitted for sliding frequency (60-50Hz), by means of frequency converters for 400/440V and a static converter/UPS for 230V. This arrangement allows the main engine and propeller rpm to be reduced by 17%.
A retractable Brunvoll 850kW azimuth thruster fitted forward provides an alternative propulsion facility in the event of main engine or gearbox failure, or if the propeller is disabled for any reason, in addition to transverse thrust. A 950kW tunnel thruster is fitted aft.
The combination of double bottom and deep fuel tanks allows 515,000 litres of fuel to be carried. The vessel’s domestic freshwater capacity is 63,000 litres. An 80t passive anti-roll tank is positioned forward on the boat deck.
Chief and second engineers Billy Hughson and Larry Williamson monitor the performance of all the vessel’s propulsion and generating machinery, electrical supplies and catch storage from a separate soundproofed control room and office.
Electric-drive MacGregor deck machinery
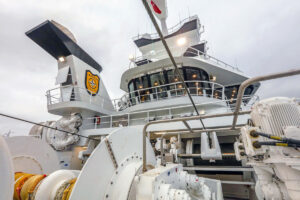
Lifeline and tail-end winches are positioned either side of the split trawl winches.
Including two 90t split trawl winches, two 95t net drums and two electric fish pumps, the 28 items of AC electric-drive deck machinery, now delivering an aggregate core pull of over 600t on Charisma, were designed and custom-built by MacGregor.
Charisma is the second new midwater trawler in the UK fleet to be equipped with electric-drive deck machinery. Research LK 62, which joined the Whalsay fleet in October 2018, was the first to be equipped with electric deck machinery, the use of which has become increasingly common on international pelagic and demersal trawlers in recent years.
Two split trawl winches, with a core pull rating of 90t and hauling/shooting speeds of 35-133m/min and 75-182m/min respectively, are positioned close to the vessel’s centreline abaft the accommodation casing on the boat deck. Protected by the upper boat deck, the winches are driven by four motors (total power 606kW) and operated through a PTS-Pentagon Cbus EE system, a sixth-generation trawl system developed and optimised by MacGregor for use with electric-drive multi-motor winches.
The winches are spooled with 2,000m lengths of 38mm-diameter Oliveira supplied by Selstad AS of Måløy. The trawl wires have slightly elevated parallel leads to inboard hanging blocks suspended within the underside of the stern gantry, to which companionways give ready access. This arrangement ensures that the crew have clear and immediate access to the midwater gear from two levels when clipping on/off helper pennants/backstrops, etc.
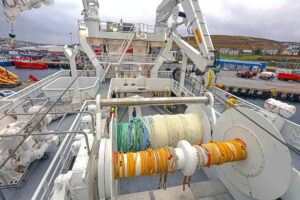
Two 95t net drums lie slightly to port of the vessel’s centreline.
Two 95t net drums, each driven by four motors (total power 817kW) and 8 x 300A frequency converters, are mounted on the shelterdeck, slightly offset to port. The net from the forward drum is shot over a large-diameter stainless steel roller mounted above the aft net drum.
A 71t lifeline winch for handling the bag is located towards the starboard side of the boat deck aft of the split trawl winch.
A 46t tail-end winch, used for pulling the bag to the stern before the sock is taken up and attached to the aft fish pump, is positioned to port on the upper boat deck, in line with a dedicated sheave mounted within the mid-height trawl gantry.
Four auxiliary winches, mounted on the underside of the trawl gantry and on the boat deck adjacent to the net drums, are available to assist the crew when shooting away the bag, and for other duties on the trawl deck. When fishing in heavy weather, the single opening through which midwater trawls are worked can be sealed off by raising a hydraulically operated vertical door, positioned aft of the customary four hydraulically operated guiding-on pins and the deck tracks for the toe-end weights.
Charisma is also equipped with two VFD-driven electric fish pumps, arranged for pumping some 1,200t of pelagic fish an hour at the stern. Similar units developed by MacGregor are reported to have performed exceptionally well on Research during her first year of fishing mackerel, herring and blue whiting.
Fish pumping
Charisma’s owners are the latest to opt for pumping pelagic fish at the stern, rather than the former location of amidships on the starboard side, the origins of which go back to the days of purse-seining when, initially, herring were brailled aboard.
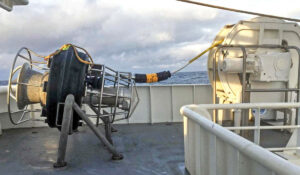
Electric-drive fish pumps and cable reels are located on the port side boat deck.
When using the net drum to dry up the brailler, the 46t tail-end winch, mounted to port on the upper boat deck, is used to haul the bag back to the quarter, before the sock is attached to the fish pump located on the wide boat deck, just forward of the trawl gantry.
Charisma is only the second pelagic vessel in the UK fleet to use an electric rather than a hydraulic fish pump. The main advantages of electric fish pumps are:
- They are more energy-efficient
- They are environmentally friendly – there are no hydraulic hoses to leak
- It is easier to handle and store the power cable. One 2in OD electric cable takes up less space than two of the larger hydraulic hoses, enabling a smaller storage reel to be used than that required for the two pipes associated with hydraulic fish pumps.
With the capacity to pump up to 1,200t of pelagic fish per hour (20t/minute), the two electric-drive fish pumps on Charisma are a recent new product from MacGregor. The VFD pumps have a new geometric shape, developed to give better fish quality and pumping control, and are driven by an oil-filled and pressure-compensated electric motor. The system on Charisma includes electric cable reels and a newly developed control system.
The fish pumps and cable reels are located on the port side boat deck, directly above two larger-diameter reels on the main boat deck, on which the fish hoses are stored.
The fish hose permanently connected to the pump sits in a captive vertical slot in the port side of the transom, allowing the hose to run clear of the stern as the pump is lowered into the water.
When the rubber hose is connected, fish are pumped some 35m forward, through a large-diameter stainless steel delivery pipe, inboard towards the fish/seawater separator system.
A short clear Perspex section (the looking glass), incorporated into the first section of the main pipe, enables the crewman controlling pumping operations to constantly monitor the flow of fish.
When pumping, the flow of pelagic fish from the separator into the 11 RSW tanks is remotely controlled from the pump room in the deckhouse.
On entering the water separator, fish are directed upwards before sliding either forward or aft into transverse troughs, from which they are directed to the allocated RSW tank by remotely operated vertical gate valves.
The large-diameter stainless steel pipes that lead from the separator are routed through the shelterdeck to enter the RSW tanks from the side, thereby leaving the tops clear for the crewmen to easily observe the level of fill.
With buyers worldwide requiring ever-higher standards of catch quality, the owners placed particular emphasis on Charisma landing a top-quality product, by being able to reduce the temperature of pelagic fish entering the RSW tanks to an optimum storage temperature as quickly as possible.
Two ammonia-based refrigeration plants from Johnson Controls (York/Sabroe), positioned at main deck level to starboard of the centreline, in the area between the central RSW tank trunking, deliver 2.6mkCal/h of cooling capacity, enabling pelagic catches to be brought down to the desired temperature of -1.3°C/-1.5°C in the minimum timescale.
Pelagic catches from Charisma are discharged to processing factories ashore by twin IRAS 4,200-litre vacuum pumping systems. Situated to port of the refrigeration machinery and operated by 4 x 66kW compressor units located in a dedicated adjoining room forward, the system has a delivery rate of 150t/200t per hour.
Furuno integrated fishing bridge
H Williamson & Sons Ltd of Scalloway, Shetland designed, supplied, installed and commissioned the state-of-the-art electronic equipment, which performed well on Charisma’s first two trips.
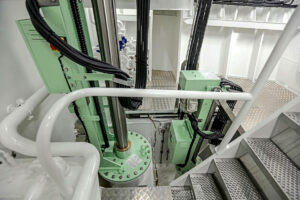
The hoists for the Furuno FSV25 and 85 sonar units.
The main forward console comprises a Furuno/Böning video wall, in which five 55in 4K Hatteland pedestal-mounted screens are arranged in a shallow arc across the front of the wheelhouse, to give an integrated fishing bridge system. The layout of the screen displays on the video wall is controlled by various presets. By using one of three 24in touchscreen controllers, skipper Davie Hutchison can select his preference from these when Charisma is searching for marks, towing, steaming or entering/leaving port.
The touchscreen panels also have radar and sonar control functionality. So, for example, common functions in sonar operation – e.g. gain/range/tilt for each sonar – can now be operated from one panel. The sonar and radar control units are hidden in the console, and can be pulled out if required.
The video wall is located in front of three NorSap Easy skipper’s chairs positioned between wing and island consoles, which together form the main navigation position.
Slim wing consoles that come into play when Charisma is manoeuvring in confined areas are located at the forward corners of the wheelhouse.
The central fishing console aft provides a commanding view of midwater trawling activities across the stern. A further 16 26in Hatteland screens are fitted on the various consoles.
Charisma is equipped with a comprehensive array of Furuno underwater acoustic equipment units. Initial location of pelagic fish is performed by Furuno FSV25 BB and FSV85 omni-sonars, of which the operational frequencies are centred on 20kHz and 80kHz.
Vertical echo detection is performed by Furuno FCV 1900B and Furuno FSS1 BB fish species discrimination sounders served by Airmar CM599
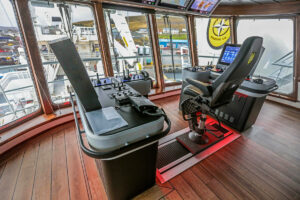
Charisma’s trawl console.
transducers. A Furuno CI68 BB current indicator provides tidal data at five different depths.
When tracking marks in heavy weather, heave compensation for the sonars and sounders is provided by a Kongsberg MRU-3 motion reference unit.
Performance of Charisma’s midwater trawls when towing is monitored by a Marport net-monitoring system, from which information is received from a combination of three trawl-eye units, six hybrid catch, two door and two catch-eye sensors. The Marport trawl-monitoring system is integrated into the MaxSea TimeZero plotting system, to enable the position of the doors to be shown relative to the vessel.
Two Furuno omni-trawl sounders operate through the cable winch mounted atop the gantry.
Navigation requirements are handled by a Furuno TECDIS 2138B electronic chart display and information system supported by two type-approved Furuno BB radars, together with a Furuno solid-state Doppler DRS6-NXT unit. This radar is also interfaced to one of the two MaxSea TimeZero ProFish plotters installed on Charisma.
GPS and heading data is provided by two Furuno GP170 type-approved GPS receivers, three Simrad GC80 gyrocompasses, a Furuno SC70 satellite compass and a Navitron NT999 dual-head autopilot system.
AIS information is handled by the latest-model Furuno FA170.
A Furuno BR500 watch alarm system gives peace of mind to the skipper and crew when Charisma is steaming to and from the fishing grounds.
A full Sailor GMDSS package was also installed by Williamson’s, including 6310 MF/HF radio telephone, 6222 Class A VHFs, Entel HT649 handheld VHFs, Furuno Felcom 18 Sat C and Furuno NX700B Navtex. Jotron EPIRBs and SARTs are also fitted.
Man-to-man communication when the crew are working on deck is handled by Icom F1000 PMR units built into Geko protective helmets.
Satellite TV is provided by a Sea Tel 120 1.2m TVRO package.
Benefits of electric deck machinery
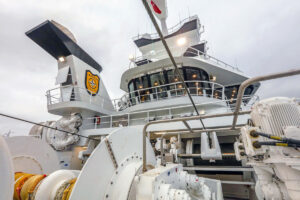
Lifeline and tail-end winches are positioned either side of the split trawl winches.
The greater focus on fuel consumption, and on carbon footprint in relation to the environment, has contributed to the growth in popularity of electric winches, which have been widely used in the offshore industry for many years.
New motor technology, enabling more powerful electric winches of similar overall size to hydraulic winches, is also a key factor.
Electrically driven deck machinery delivers the benefits of reduced energy consumption, reduced maintenance, less noise, precision control, and the fact that no hydraulic oil is required.
Another major advantage is that electric-drive winch efficiency is estimated to vary between 70% and 85%, compared to an efficiency level of 35-60% for hydraulic drive.
AC electric drives for winches comprise of:
- A variable frequency drive
- An AC induction motor
- A reduction gearbox
- A sensor feedback and control system
- A cooling system
- A braking system.
The new drive (VFD) technology has reduced the size of the cabinets. As a result, they require less space than an HPU at comparable power rating. This is fully apparent on Charisma, where the main electric cabinet control room aft, and the secondary room for the anchor windlasses and forward mooring winches, are considerably smaller than the customary hydraulic pump rooms.
Discussing the background to the electric-drive deck machinery, it was immediately clear that, as anticipated given the level of change involved, there is considerably more required than just replacing the hydraulic motor with an electric motor.
Rapp Marine/MacGregor started to develop the electric-drive deck machinery installed on Charisma 15 years ago. Since then, the company has spent a tremendous number of hours on workshop- and field-testing of various drive concepts, to learn new technology and optimise the drives and control system.
The conclusion was quickly reached that new electric winches should be based on the same concept as hydraulically driven winches – namely, multi-motor drives with three or four medium-speed piston motors, connected to the winch drive via a one-step gearbox of approximately 4-5.5:1 reduction.
This arrangement, which has a 25-year successful track record, gives a large degree of redundancy, low acceleration stiffness, and high serviceability, with relatively small and lightweight motors that are easy to replace and handle.
Advantages with the multi-drive concept are:
- Redundancy – motors and drives are sized to obtain 80% winch pull if one of three or four motor (VFD) drives should be out of service
- Three or four small FC motors give a moment of inertia four to five times less than single-motor electric drives, and excellent response and fast reaction times for compensation during towing.
A bevel/planetary two-step gearbox with a ratio of approximately 11-14:1, depending on winch size, is positioned between the main gearbox and each electric motor.
To meet the technical requirements for autotrawl operation, it is necessary to apply extra cooling to the electric winch motor when working at zero to low speed during towing, with up to 80% of the maximum torque. This is traditionally done by jacket/water cooling or by a separate cooling unit, and these types of motors are relatively large in size and weight.
In order to fit considerably more compact motors, MacGregor started to develop a new concept for motor cooling. This resulted in the fluid-controlled (FC) electric motor, which is now internationally patented.
This concept uses a standard high-performance motor insert (ABB) combined with Rapp ‘packing/housing’, which makes it possible to circulate cooling fluid through the inside of the electric motor (between the rotor and stator) to control the heat. Another benefit from this technology is the ability to increase the power/torque rating by more than 250%. The biggest air-cooled motor currently used for electric winch drive can develop around 75kW continuous power as standard, but FC technology, with the same safety margin, can take 188kW continuous power from the same frame size 225 SMD.
The control system developed for electric multi-motor drives ensures continuous load-sharing between the three or four motors.
The main power system for the electric deck machinery on Charisma is divided into two sections of 1,000A/660kW continuous duty at 440V.
SeaQuest Systems deck cranes
Charisma is equipped with three customised deck cranes designed and manufactured by SeaQuest Systems of Killybegs. The Co Donegal specialist has supplied a succession of similar deck cranes to Karstensens for installation on new Danish and Norwegian midwater vessels in recent years, as well as the Fraserburgh midwater trawler Grateful.
Two identical SeaQuest cranes, with a lifting capacity of 4t @ 14m, are mounted on either side of the trawl gantry aft. Each crane is fitted with SeaQuest type PB02 powerblocks featuring hydraulic tilt and continual rotation. The continual rotation facility on the powerblock is an extremely useful feature for mending midwater trawls, or taking twists out of the net, brailler or bridles.
The jib sections of the gantry cranes are custom-designed and -built, so that the operator gets maximum usage from the crane, to get down to the main deck to pick up the net in the powerblock, to get the stern fish pump in and out with ease, and when reaching over the gantry to the trawl doors.
The forward knuckle-boom crane has a reach of 18m and is fitted with 4t and 2t winches.
As is customary with SeaQuest cranes, all hinge pins, cylinder rods, hydraulic fittings and pipework are manufactured in stainless steel, while all other parts were shot-blasted and metalised before painting.
In order to ensure continuity throughout a trip, all three cranes were supplied with the same style of interchangeable radio-control unit. In the unlikely event of one control unit being dropped in heavy weather, this will allow the operator to ‘borrow’ another crane’s transmitter by swapping out a SIM card-style chip mounted in the unit. It also allows a vessel to carry a spare transmitter which will cover all three cranes.
Fourth Charisma for Whalsay partners
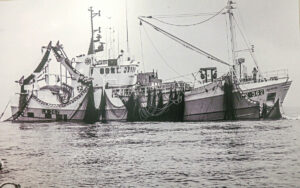
The first Charisma pursing.
Charisma is the fourth new pelagic boat of the same name to be skippered by Davie Hutchison.
The first Charisma arrived at Whalsay in 1979. With an LOA of 107ft and 25.36ft of beam, this fully shelterdecked purser/trawler was fitted out by Sigbjørn Iversen at Flekkefjord after the hull had been built at Hellesund by Bentsen & Sønner. Powered by a 1,100hp Mirrlees Blackstone engine, the first Charisma had six RSW tanks, giving a fish-carrying capacity of 220t.
The first Charisma fished from Shetland until 1995, when the boat was sold to Peterhead and renamed Alert FR 396, later moving to Castlebay and being renamed Charisma CY 88. During the 16 years that the vessel was in Shetland, it was extensively altered, being lengthened by 49ft, fitted with a raised wheelhouse and re-engined in 1985, before a whaleback was added atop the shelterdeck in 1989.
Davie Hutchison and his partners renewed their acquaintance with Flekkefjord in 1995 when they took delivery of the 57.7m and 2,190kW Wärtsilä-engined midwater trawler Charisma LK 362 from Simek AS.
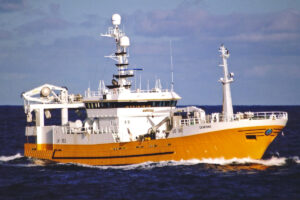
Simek AS built the 57.7m Charisma at Flekkefjord in 1995.
The second Charisma was replaced in 2003 with a 71m midwater trawler, built for the Charisma Fishing Company by Flekkefjord Slipp & Maskinfabrikk AS. Powered by a 6,000kW MaK 12M32 engine, the third Charisma was bought by the Icelandic fishing company Eskja in 2018, when the vessel was renamed Jón Kjartansson.
The continuity that boats like Charisma bring to Whalsay is shown by the fact that four of the new Charisma’s crew, John Pearson, William Polson, James Tulloch and Larry Williamson, have sailed with skipper Davie Hutchison for 40 years, since the first Charisma arrived in Shetland.
Charisma completes renewal of Whalsay pelagic fleet
When skipper Davie Hutchison took Charisma alongside at Symbister for the first time, it marked a notable achievement for the small island of Whalsay, where the local pelagic fleet has been renewed over three years.
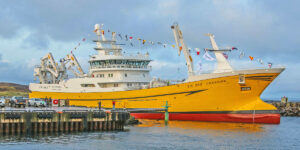
Charisma entering Symbister harbour for the first time, to complete the renewal of Whalsay’s midwater fleet.
Charisma is the third new arrival in four months, after Adenia and Zephyr were both welcomed home to Whalsay in September.
The new Serene and Research joined the local pelagic fleet in September and October 2018, less than a year after Antares started the ball rolling in December 2016.
Antarctic II was lengthened as part of a major upgrade project in 2017.
This largescale reinvestment in the pelagic sector firmly underlines the hugely important role fishing continues to play on Whalsay, and the determination of the island’s fishermen to stay ahead in a highly competitive international fishery for the benefit of their families, and just as importantly, future generations.
Lying a few miles to the east of mainland Shetland, Whalsay is less than six miles long and two miles wide, and probably has the largest concentration of vessel owners and fishermen in Britain in the island’s resident population of just over 1,000 inhabitants.
In the continuing absence of fixed transport links with mainland Shetland, residents are extremely familiar with the ferry timetable for the 45-minute crossing to Laxo – or Vidlin when poor weather prevails, as is regularly the case.
Inevitably, this puts additional logistical constraints on skippers, not least in relation to trying to meet service engineers, etc, flying into Sumburgh from Norway and Denmark.
At the same time as the pelagic fleet development was in progress, Whalsay-based whitefish partnerships also invested in new vessels, in the form of the fly-shooters Resilient and Tranquility.
This level of ongoing reinvestment in an industry that is the lifeblood of the community is a fantastic achievement. It is also a ringing endorsement of long-term confidence in the health of the demersal and pelagic stocks, which is self-evident on the rich fishing grounds around Shetland, the benefits of which should now be further enhanced by sound fisheries management post-Brexit.
Charisma takes on new Swan Net-Gundry midwater trawl technology
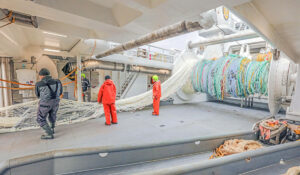
Pulling a midwater trawl…
Following its recent provision of an extensive package of midwater gear to the new Whalsay pelagic trawler Zephyr (Fishing News, 7 November), Irish net designer and manufacturer Swan Net-Gundry (SNG) has again been the popular choice for pelagic gear for the new Charisma.
Supplied from its Lerwick and Killybegs depots, SNG’s large range of gear for Charisma includes a 1,024m dual-purpose mackerel/herring trawl, on which the front of the trawl is constructed with a combination of PE overbraided ropes (PEPA) and Danline ropes.
Kraftex frame ropes are used, in conjunction with SNG’s own Prima Overbraided footrope, which has proven to be excellent due to its abrasion-resistant qualities.
For the trawl tunnel, Charisma is supplied with SNG’s eight-panel model, which can provide added benefits compared to the conventional four-panel type, as this offers improved water flow, greater stability, added strength and increased mesh opening.
With SNG’s Fast Flow system taking the international pelagic industry by storm last year, it is no surprise that Charisma is now using two SNG 65m Fast Flow braillers with DynIce Handle System (DHS) and 44mm DynIce SK75 used for the splitters.
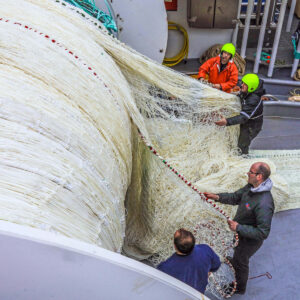
… onto the lower net drum.
A full report on SNG’s Fast Flow brailler system will be included in Fishing News soon.
Skipper Davie Hutchison and crew also took delivery of two 1,460m mackerel trawls and a 1,280m dual-purpose herring/mackerel net from SNG.
MMG gangways give safe boarding
Killybegs company MMG Welding supplied one of their patented Compact Gangway systems to the new Charisma.
Since the innovative design was launched in 2018, MMG Welding has supplied vessel-to-pier and vessel-to-vessel gangways to a succession of Irish and Scottish pelagic boats, including Father McKee, Menhaden, Western Chieftain, Western Viking, Antares, Christina S, Quantus and Zephyr.
Although evolution over the past 40 years has been extraordinary in terms of vessel design, catching capability, carrying capacity, hydraulics, refrigeration, electronics, etc, some things onboard have changed very little, as the ‘old reliable’ way of doing things, or a particular piece of equipment, has never been improved upon.
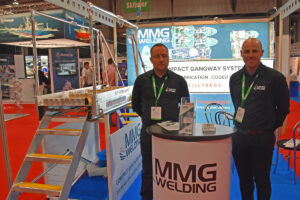
Mark McCallaig and Martin McGuiness standing on one of MMG Welding’s vessel-to-vessel Compact Gangway systems.
One such item that has remained largely unchanged during this time is the method used to board vessels while tied to the pier and, despite this not sounding like an issue of any great importance, increasing safety requirements have led to officially certified gangways becoming mandatory for all sizes of commercial craft.
Recognising the need for a safe and versatile method of accessing vessels from the quayside, MMG Welding focused on finding a solution.
Built to the requirements of DNVGL-ST-0358/ISO 7061:2015, the patented Compact Gangway systems feature drainage-perforated tread plate steps for maximum safety and, for easy storage purposes, a unique manual folding mechanism with collapsible handrails, making it an ideal solution for vessels with limited storage space.
DETAILS
Owners: Charisma Fishing Company Ltd, Whalsay, Shetland
Designer/boatyard: Karstensens shipyard, Skagen, Denmark; hull built by Remontowa shipyard, Gdansk, Poland
Class: DNV-GL +1A1 Ice-C
Agent: LHD Ltd, Lerwick, Shetland
DIMENSIONS and CAPACITIES
Length overall: 75m; Length between pp: 67.2m; Beam: 15.3m; Depth main deck: 6.5m; Depth shelterdeck: 9.2m; Draught: 8.5m; Tonnage: 2,950 GT; Fuel: 515,000 litres; Freshwater: 63,000 litres; Technical water: 150m³ + 88m³ roll reduction tank; RSW: 11 tanks – 2,311m³
ENGINEROOM
Main engine: MAN 12V32/44CR-TI of 7,200kW @ 750rpm driving through a Brunvoll ACG-980/PS750 two-step 5.77/7.14 reduction gearbox to a Brunvoll Volda CP105/4 4,200mm-diameter four-bladed CP propeller in a fixed nozzle; Speed: 18.5 knots
Shaft generator: AvK Cummins DSG 114M2 6W 3,000kW/3750kVA @ 1200rpm 415/3/50 with sliding (50/60Hz) frequency
Auxiliary engines: 2 x Caterpillar 3512B of 1,570kWe @ 1800rpm driving Stamford 415/3/15 generators; 2 x Caterpillar C9 250kW harbour/emergency gensets
Thrusters: Brunvoll – 1 x 850kW retractable combi azimuth/bow thruster and 1 x 950kW stern thruster
Fuel/lube oil separators: GEA Westfalia; Main engine and hydraulic cooling, bilge/deckwash/fire ballast and engine fuel transfer pumps: Bombas Azcue; Bilge ejectors: Ellehammer; Starting/working air compressors: Sperre HL2/105A; Atlas Copco GA11FF
DECK MACHINERY
Suppliers: MacGregor and SeaQuest Systems Ltd, Killybegs
MacGregor: 2 x split trawl winches TWS-34041RE 90t first-layer pull with capacity for 3,130m 38mm-diameter trawl wire; Rapp PTS-Pentagon Cbus-EF autotrawl system; 2 x net drums ND-3400EB 43m³/95t; 1 x topline winch TWS-22031TE 71t; 1 x tail-end winch GW-20001BE 46t; 2 x Gilson winches GW-200E 3.6t; 2 x backstrap winches GW-200E 2.6t; 5 x mooring winches GW-680E 6.6t; 2 x anchor winches AWW-4000E 6.3t; 1 x net-sounder cable winch SOW-502RE 3.6t first-layer pull with capacity for 2,950m 12.4mm-diameter Dyneema cable; 2 x MacGregor 20in electric fish pumps CP-3501 20in; fish hose storage reel FHR-480N 3.5t; fish pump electrical cable storage reel RHM326692 1.6t
SeaQuest Systems: 2 x 4t/14m radio-control cranes c/w 4t winches and SeaQuest powerblocks c/w endless 360° rotation; 1 x 4t/18m radio-control knuckle-boom foredeck crane c/w 4t and 2t winches
FISH PUMPING/STORAGE
Fish pumping system: 2 x 24in SeaQuest fish pumps; RSW cooling plant: Johnson Controls (York/Sabroe) – 2 x 1,435kW (1,234,000kCal/hr); Vacuum landing system: 2 x IRAS c/w 2 x 4,200-litre tanks served by 4 x 66kW compressor units; Vessel monitoring system: Marine Control Services
ELECTRONICS
Supplier: H Williamson & Sons Ltd, Scalloway
Fish detection
Furuno FSV25 360° low-frequency (18/20/22kHz) and Furuno FSV85 360° medium-frequency (71/84kHz) sonars; Furuno FCV1900B sounder c/w Airmar CM599 transducer; Furuno FSS1 BB MK2 fish ID sounder c/w Airmar CM599 transducer; Simrad ES80 38kHz and Simrad ES80 200kHz split-beam sounders; Simrad dual ES80 processor; Kongsberg MRU-3 motion reference unit; Furuno C168 BB current indicator (160kHz); 2 x Furuno omni-trawl sounders; 1 x Marport M6 acoustic receiver c/w 6 x wide-band hydrophones, 3 x trawl explorers for tunnel, 6 x hybrid catch sensors and 2 x door sensors with pitch, roll and depth, 2 x catch explorers and 3 x sensor chargers
Navigation
Furuno DRS6A-NXT, FAR3220 BB and FAR3230 SSD BB radars; Furuno TECDIS system c/w T-2138B dual BB processing unit; 2 x Furuno GP170 GPS receivers; 2 x MaxSea TimeZero ProFish plotting systems; Navitron NT999 dual-head autopilot interfaced to dual Simrad GC80 gyrocompasses; Simrad GC80 compact gyrocompass; Furuno SC70 satellite compass; Furuno FA170 AIS; Furuno BR500 bridge watch alarm; Gill Windsonic anemometer
Communications
Sailor 6310 MF/HF 150W GMDSS RT; Sailor 6222 GMDSS VHF; 3 x Entel HT649 handheld GMDSS VHFs; 3 x Sailor 6248 VHFs; Furuno Felcom 18 Sat C; Furuno NX700B Navtex; Jotron 60S GPS EPIRB; 2 x Tron SART 20; Peitel GSM bridge and ECR phones; 16 x Icom F1000 PMR VHFs and 10 x Geko headsets; Sea Tel ST120 satellite TV system; CCTV camera system c/w 16 cameras
FISHING GEAR
Midwater trawls: Swan Net-Gundry, Killybegs – 1 x 1,024m and 1 x 1,280m dual-purpose mackerel/herring nets; 2 x 1,460m mackerel nets; 2 x 65m Fast Flow braillers; Trawl wire: Selstad AS, Måløy – 2 x 2,000m of 38mm-diameter Oliveira trawl wire; Midwater trawl doors: Thyborøn Type 20 Slider 15m² 4,000kg
ACCOMMODATION
12 x single-berth and 2 x two-berth ensuite cabins plus hospital cabin
GENERAL
Engine controls: Brunvoll BruCon; Insurance: British Marine; Lifesaving appliances: Viking and Ikaros; Paint: Sigma; Skipper’s chairs: 4 x NorSap; Steering: Rolls-Royce Tenfjord SR SR 662 – 170kNm; Windows: Van Winderden; Wipers: Wynn straight-line