Macduff Shipyards delivers third new boat to Peterhead skipper, two months ahead of schedule
Peterhead skipper James West and the crew of the 21.5m twin-rig prawn trawler Westro PD 20 were expected to sail from their home port this week for the vessel’s maiden trip, reports David Linkie
Westro is the third new boat in 14 years that Macduff Shipyards has delivered to skipper James West, who is well-known for being a forward-thinking skipper, and for his enthusiasm for fishing in general. The 19.9m Fruitful Bough PD 109 was the first in 2004, followed six years later by the 21.2m Golden Sceptre PD 50.
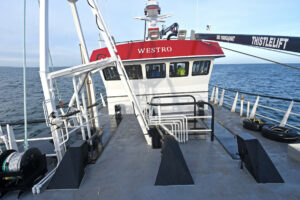
All three trawl warps run under the wheelhouse floor.
The name Westro derives from the skipper’s surname, and the family association is strengthened by the fact that the date of James West’s six-year-old son Ethan’s birthday is the same as the boat’s registration number.
From the start of the design and build project, James West liaised closely with the Macduff Shipyards team to incorporate an interesting selection of new ideas on Westro, each of which is designed to contribute to enhanced fishing efficiency, crew safety and catch quality.
These include:
- All three trawl warps running under the floor of the wider wheelhouse
- Two auxiliary single net drums atop the shelterdeck
- A catch-bagging arm and hull side Gilson rope
- A high-efficiency fishroom refrigeration system
- Two 42in display screens in the wheelhouse.
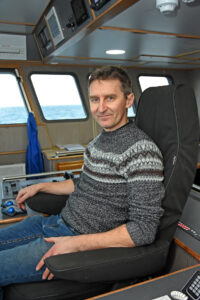
Westro skipper James West.
Combined with a number of smaller-scale but equally proactive ideas, these innovations have resulted in a modern vessel customised to the owners’ specific requirements.
Owned by skipper James West in partnership with P&J Johnstone Ltd, Westro ran fishing trials from Macduff on 18 January, and six days later, it sailed from Peterhead on its maiden trip, more than two months ahead of schedule. The earliness of its completion is highlighted by the fact that the vessel’s pre-booked naming ceremony will be held at Peterhead on 23 March.
The keel was laid in Macduff Shipyards’ main fabrication hall at the beginning of June 2018, when the first pre-fabricated hull sections were lifted into position as the hull quickly took shape from the stern forward. The yard’s in-house joinery and engineering teams, together with specialist sub-contractors, maintained this rapid rate of progress as the internal fit-out and machinery installation progressed smoothly.
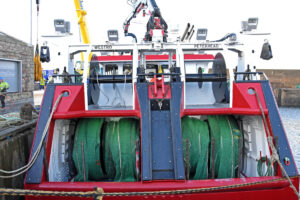
Stern view of Westro, showing the trawler’s six net drums. The link to clip in the Gilson rope is shown at the bottom right.
Skipper James West said: “The Macduff team was very receptive to my suggestions during the design and build stages, and implemented all requests effectively.
“That Westro performed totally as planned and expected on fishing trials says everything about Macduff Shipyards. The level of internal finish and engineering speaks for itself.
“Everyone who contributed to the end result should be very proud of the part they played in building Westro, which I’m confident will prove to be an efficient and economical boat to run.”
Westro’s double-chine steel hull, which incorporates a deep box-section ballast keel, was built using a Lloyds Grade A steel kit, cut by Macduff Profilers (a division of the builders) from cutting information supplied by Macduff Ship Design Ltd.
The main dimensions of Westro are LOA 21.5m, registered length 19.03m, beam 7.1m, depth moulded 4.05m, draft 4.6m, and GT 204t. Fuel capacity is 22,700 litres, and 15,267 litres of freshwater are carried.
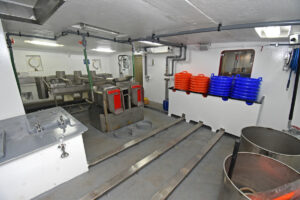
General view of working arrangements on the catch-handling deck, which is GRP-lined and fitted with stainless steel deck racks.
Westro’s hull design and engineroom machinery are almost identical to that of Forever Faithful PD 287, which Macduff Shipyards delivered to James West’s brother Andrew West, also in partnership with P&J Johnstone Ltd, in October 2016. The consistently successful performance of this vessel, together with that of the similar-sized Golden Sceptre PD 50, meant that skipper James West had no hesitation in placing an order for a third boat with Macduff Shipyards when he took the decision to build again.
Golden Sceptre will now be run for James West by Stuart Legge, who previously sailed with him as mate and relief skipper.
James West, who will soon start to share wheelhouse duties on Westro with his younger brother Stephen West, expects to work trips of six to seven days’ duration, working closely with Stuart Legge on Golden Sceptre and his brother Andrew on Forever Faithful. The skippers anticipate that the benefits of two virtually identical boats, and a very similar third vessel, working together will include the ability to constantly match and strive to fine-tune the performance of their gear, as well as finding better fishing.
General arrangement
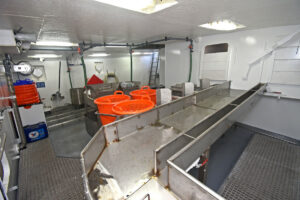
General view of the catch-handling deck amidships.
Under the full-length steel shelterdeck, which is formed as an extension of the hull without a gunwale rail, a watertight full-width deckhouse separates the weathertight catch-handling area forward from the net-handling area on the quarter. The connecting passageway is arranged slightly to starboard of the vessel’s centreline. This spacious arrangement, which incorporates bench seating, has enabled a walk-in heated compartment housing the crew’s deck gear and safety equipment, together with laundry facilities, to be positioned against the vessel’s starboard side, forward of a separate toilet and shower room.
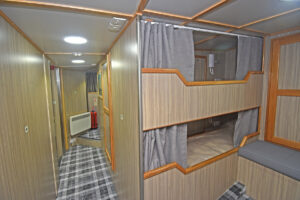
Two of the five beds arranged to port in the full-width accommodation cabin.
The doors at each end of the internal passageway give an immediate illustration of the thought that skipper James West gave to the fine points of detail on Westro. A small sliding window in the door leading forward onto the catch-handling deck enables the crew to easily operate the various deck pumps located in the passageway, thereby eliminating the need to continually open the door, and so helping to keep the passageway cleaner. A similar-sized fixed window in the after door means that the crew can see what conditions are like on the quarter before going on deck.
A dedicated winch room is positioned on the main deck, forward of a walk-in compartment housing the machinery for the fishroom refrigeration system and ice machine, installed by Airo-Tech Solutions Ltd of Fraserburgh. The refrigeration room extends to port of the vessel’s centreline, with the equipment mounted on the longitudinal bulkhead that forms the forward section of the reception hopper. This arrangement facilitated skipper James West’s request for the ice locker to be centrally positioned in the fishroom, directly beneath a 1t flake ice machine, in order to ensure that Westro remains on an even keel throughout a trip.
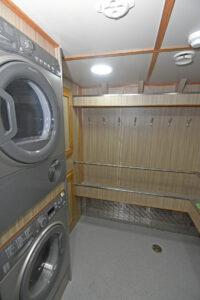
Laundry facilities are built into the heated deck clothing room…
The area under the reception hopper to starboard of the chilling equipment provides a considerable storage area at main deck level.
The catch-handling deck is kept free of excess water from the fishwashers by two deck sumps drained by electrically driven Azcue pumps.
The vessel’s immaculately finished combined galley/messdeck is arranged on the port side of the steel deck casing.
The usual range of electrical units in the galley, together with the separate washer and tumble-dryer built into the deck clothing room, were supplied by RD Downie of Fraserburgh which, as customary with all Macduff builds, wired Westro and manufactured the engineroom and wheelhouse electrical distribution cabinet boards.
Below main deck level, the layout of Westro from forward follows the usual arrangement of forepeak, fishroom, engineroom and accommodation cabin.
Down the aft stair, the main accommodation cabin has been cleverly arranged to give a total of seven beds, five to port and two to starboard, in addition to a separate single-berth skipper’s cabin to starboard. The equivalent area on the port side of the central passageway has been used to create a storeroom for the boat’s medical boxes and stretcher, which supplements the customary lockers and drawers adjacent to the beds.
Trawling arrangements
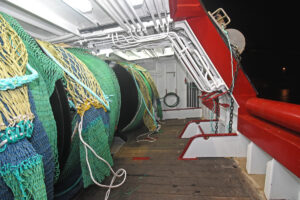
General view across the quarter.
Macduff Shipyards manufactured the deck equipment installed on Westro, including the three-drum trawl winch, positioned forward on the main deck in a dedicated compartment. Rated 30t core pull, the winch is fitted with two-speed drive motors for faster hauling and shooting of the wires.
At the owners’ request, the middle drum was made considerably longer than the two outer drums, and is currently fitted with easily removable reducer flanges. This will give maximum flexibility in years to come, as on removal of the side flanges, the middle barrel of the winch will have sufficient capacity to accommodate the considerably longer length of wire and combination warp used when pair-seining.
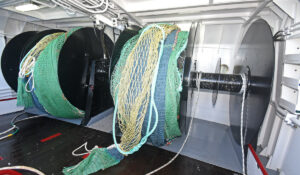
The outer sections of the split net drums are wider to accommodate the bulkier prawn hopper trawls.
The three equal-length winch barrels are spooled with 275 fathoms of 20mm-diameter covered Dyneema warp, supplied by Faithlie Trawl of Fraserburgh. Having used a set of similar warps successfully on Golden Sceptre for the past two years, skipper James West had no hesitation in rigging out Westro with Dyneema warps.
In addition to greater durability (up to three years, compared to eight to 12 months for trawl wires), Dyneema warps also give reduced abrasion to the vessel and blocks. Dyneema DynIce warps are also reported to perform more efficiently when towing in soft mud.
A 150-fathom length of Dyneema warp is attached to the chains worked at the foreside of the doors and middle clump. Five x 25-fathom lengths of Dyneema warp next to the core of the winch drums enable accurate settings to be made in relation to the prevailing depth of water, weather and tidal conditions. Each section of Dyneema warp is fitted with soft eyes and Dyneema lashings to sit smoothly on the winch.
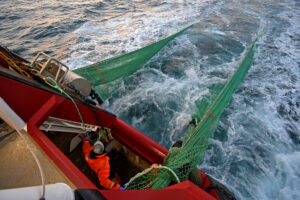
Shooting the 100ft twin-rig prawn hoppers for the first time on fishing trials.
Led up from the drums at around 35° to hooded rollers, all three warps have short straight runs across the top of the shelterdeck to a second set of sheaves positioned at the foreside of the wheelhouse casing. In a new arrangement, following the owners’ request for a wider wheelhouse, the outer wires, as well as the middle one, run under the wheelhouse floor to a third set of guides positioned at the aft end of the casing on the shelterdeck. The middle wire then leads upwards to pass over a roller incorporated into the transom rail, directly above a secure track for the safe storage of the middle roller. The outer wires are directed upwards towards hanging blocks mounted on a conventional trawl gantry.
When towing, the outer warps are connected to a Dyneema strop running over a large-diameter sheave attached to a central towing point on the trawl gantry. This ‘poor man’s’ auto-trawl arrangement allows the port and starboard warps to take up natural leads when the vessel is turning, before equalising again with the fixed middle warp, when a straight heading is resumed.
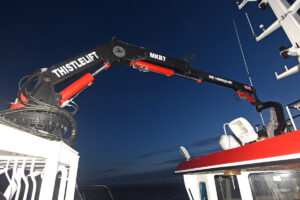
Westro’s ‘colour-co-ordinated’ Thistle Marine MKB7 short-post crane is centrally mounted atop the trawl gantry.
Hardwearing UHMW-PE sheathing panels and strips are secured to outer hull areas in line with where the trawl doors and middle roller are worked, to minimise abrasion, wear and paint discolouration.
Two sets of 2 x 10t split net drums are arranged side by side on the non-watertight wooden-decked quarter, in line with the customary transom shooting and hauling hatches, the lower edges of which are fitted with free-turning large-diameter rollers. The middle flange on each net drum is slightly offset to one side, thereby providing more room on the drum for the bulkier prawn hopper trawls, compared to the scraper nets. This arrangement is also expected to prove beneficial in the event of skipper James West changing over to squid, as he did in some years on Golden Sceptre.
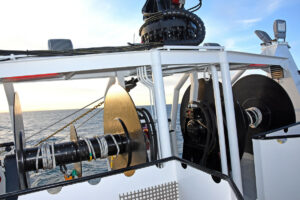
Two single net drums are mounted on the shelterdeck aft.
Two similarly-rated single net drums are positioned aft on the shelterdeck. These are primarily intended to provide increased flexibility when dealing with fouled gear and torn nets, as well as carrying spare gear.
Thistle Marine Ltd supplied the MKB7 short-post crane (1,400kg/5.5m), with a tilting 24in ribbed powerblock that is centrally fitted on the trawl gantry. Appropriately, the finish on the two Thistle Marine cranes on Westro is colour-co-ordinated to the vessel’s hull colours, with the red-painted cylinder rams standing out against the black boom sections.
Catch-handling
The codends are taken aboard forward on the starboard side, by a 4t Gilson winch serving a lifting tripod arranged over a hydraulically operated hatch and a large-capacity reception hopper. In order to keep the shelterdeck clear of obstructions, the hydraulic ram used to lift and lower the bag hatch is positioned at 60° within the lifting gantry, instead of the more usual location just above the shelter.
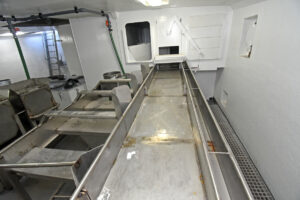
The selection table extends down the starboard side of the fully-lined catch-handling deck.
Westro features new working arrangements for taking the codends forward, following their successful trial on Golden Sceptre. These were developed to enhance efficiency and safety, and to enable skipper James West to operate the Gilson winch using controls located at the forward starboard corner.
A pivoting ‘bagging arm’, arranged at the aft side of the bag hatch, is central to the new arrangements. When Westro is fishing, the round-section stainless steel arm is lowered and clamped into position parallel to the shelterdeck, extending outboard for 1m. At the same time, the Gilson rope is clipped in at the starboard quarter, and heaved tight along the side of the hull under the bagging arm. On hauling, the Gilson is slackened off and attached to the bag, which is then taken forward in the usual manner.
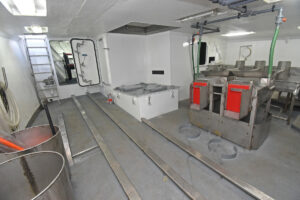
Stainless steel deck tracks are fitted on the port side of the main deck between the prawn washers and dip tanks.
After being released from the codend into the hopper, the catch is gravity-fed onto a table that leads aft, from which the crew sort and gut the catch. Selections are placed into elevated selecting baskets, while prawn tails are directed into baskets on the deck via separate chutes.
Twin prawn/whitefish washers are fitted abaft the fishroom hatch, adjacent to the sorting area. Two circular prawn dip tanks are positioned to port of stainless steel deck tracks for the secure storage of filled baskets.
In order to ensure ease of cleaning and promote optimal levels of hygiene, the catch-handling area is fully lined and coated with several layers of GRP matting, to provide a durable waterproof finish on completely flush surfaces that are easily cleaned down. The use of plastic piping serving the hopper, prawn washers and dip tank further enhances ease of maintenance, as do the stainless steel basket racks on the port side of the main deck.
Capable of holding around 650 CHEP nest/stack boxes, the fishroom was fully lined and insulated by the yard in conjunction with Davidsons of Peterhead.
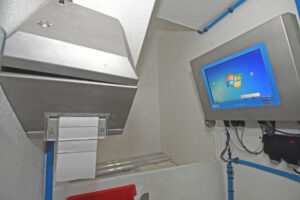
Weighing and labelling equipment serving a VCU catch-management system is positioned in the port wing locker.
The fishroom features similar GRP-lined flush surfaces, including the deckhead. This highlights the fact that Westro is equipped with a fan-based evaporator refrigeration system, installed by Fraserburgh company Airo-Tech Solutions Ltd, rather than the customary stainless steel piped deckhead chilling system. (See ‘Airo-Tech Solutions Ltd – new fishroom refrigeration system’ opposite.)
On being lowered by basket down to the fishroom, prawns are electronically weighed and labelled using a VCU catch-management system positioned in the port wing.
Flake ice, produced by a 1t Geneglace machine, is stored in a central wing, behind which spare boxes can be stored.
While Westro is primarily expected to target prawns, provision has been made for whitefish to be delivered by a square-section GRP-coated chute to a selection table in the fishroom.
The fishroom bilges are served by float switches and an automatic pump.
Catches are discharged from the fishroom using a Thistle Marine MFB8 straight-boom landing crane. The landing hatches in the main and shelter decks are slightly offset to port to accommodate the central ice locker.
Engineroom
The degree to which the owners, in close liaison with the builders, have endeavoured to ensure that Westro will be an efficient and economical boat to operate well into the future is revealed by the combination of centreline machinery in the well-arranged engineroom.
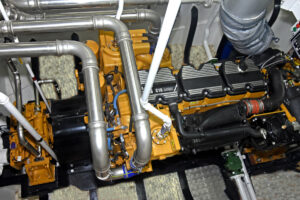
Westro’s Caterpillar C18 main engine develops 447kW @ 1,800rpm…
Westro is powered by a Caterpillar C18 ACERT main engine, supplied by Finning UK Ltd. Skipper James West and the boatyard personnel were impressed by the initial level of performance and fuel economy that this electronically controlled engine delivered on sea trials.
Developing 447kW @ 1,800rpm and solely dedicated to propulsion duties, the main engine drives a 2,000mm-diameter four-bladed fixed-pitch Teignbridge propeller turning in a bespoke-designed fixed nozzle through a Reintjes WAF374 7.476:1 reduction gearbox.
The centreline combination gave Westro an average speed of 9.3 knots on sea trials. Perhaps more importantly for a vessel that will spend more than 80% of its time at sea towing, Westro was using 50 litres of fuel @ 1,150rpm while comfortably towing the twin-rig prawn trawls at three knots in 55 fathoms of water, during fishing trials in the Moray Firth.
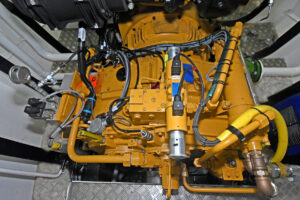
… and is coupled to a Reintjes 7.476:1 reduction gearbox.
A Cummins QSL9 variable-speed auxiliary engine (212kW @ 1,800rpm), mounted on the port tank top, runs the main hydraulic pumps for the deck machinery through a Centa drive unit.
Standby hydraulic power is provided by pumps driven by a Dong-I power take-off mounted at the fore end of the main engine.
Main electrical power onboard Westro is provided by two Beta Marine generators based on a Cummins 6BT5.9D1(M) engine (58kW @ 1,500rpm) and a 58kW 415/3/50 Mecc Alte generator.
Cooling for all four engines and the hydraulic system is provided through Blokland box coolers, arranged across the forward end of the engineroom.
Stainless steel piping is used extensively throughout the engineroom.
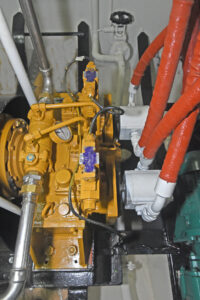
A gear retrieve system is run off the fore end of the main engine by a Dong-I power take-off and standby hydraulic pumps.
Two electrically driven 150-amp Transmotor 24V alternators provide DC supplies to the four sets of batteries fitted. A Victron 24V battery charger and inverter are also fitted.
Two wing tanks in the engineroom, together with a daily service tank, allow 24,800 litres of fuel to be carried.
A bulbous bow tank can carry 11,032 litres of freshwater, with a further 4,235 litres in a double bottom tank under the fishroom floor.
A Hardy T700 hydraulic bow thruster is fitted to give Westro enhanced manoeuvrability when operating in restricted spaces.
West(ro) twin-rig trawls
Skipper James West, together with his father James West Snr, made the two sets of twin-rig trawls that Westro will use on its maiden trip.
A set of 140ft prawn scraper nets, rigged with 8in discs in the bosum section and 6in discs down the wings, are used when towing on softer bottom, together with 60 fathoms of 40mm-diameter single combination warp and 20 fathoms of rubber legs.
When fishing on harder ground, skipper James West works 100ft twin-rig prawn hopper trawls rigged on 8in/10in discs.
Macduff Shipyards manufactured a set of 76in trawl doors (700kg) and a 900kg roller clump to an in-house design.
Customised wheelhouse layout
Westro features a customised wheelhouse layout designed by the boatyard in line with skipper James West’s requirements. These included direct access to the forward corner windows of the wheelhouse, for optimal line of sight when taking the bag aboard using the internal controls for the bag hatch and Gilson winch.
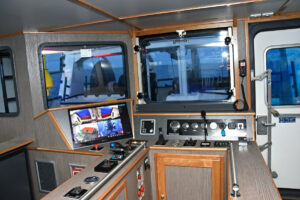
The trawl console lies to port of Westro’s centreline.
In order to accommodate the shallow consoles positioned at the corners, the ends of the main forward console are returned at 45°.
A single NorSap seat is positioned centrally in a six-sided island unit, on which the communications equipment, main radar controls and mouse plotters are arranged to starboard.
A table is flanked on either side by bench seating at the aft starboard corner of the wheelhouse, separated from the trawl console by the accommodation trap.
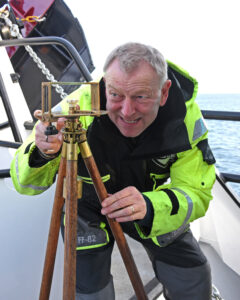
Thomas Gunn of Poseidon Navigation Services Ltd lines up marks along the Moray coast while adjusting the compass on Westro.
Westro is the first new-build of its class to feature large-screen displays. Two AG Neovo 42in-wide monitors are built into the main console. A similar third screen is situated on the messdeck. Supplied and installed by Woodsons Marine Electronics, the wide screens, together with six 24in displays, are controlled through an 8 x 8-way HDMI digital matrix switcher unit.
An iPad app will enable skipper James West to select the preferred screen arrangement for the prevailing mode of operation, including split-screen viewing.
The level of finish in the wheelhouse, together with the other internal accommodation areas on Westro, further illustrates the extremely high standards for which Macduff Shipyards is renowned.
Details of the vessel’s location are processed by two Furuno GP39 GPS receivers, and heading is provided by a Vector GPS gyrocompass. Positioning data received is interfaced to an Olex 3D seabed mapping system and a Sodena Easywin plotting system, which support tidal data, AIS and ARPA tracking.
The Koden MDC-5006F main radar is backed up by a Koden MDC-941 unit. Both radars are interfaced to an Em-Track Class A AIS transceiver and, with ARPA, provide tracking through the Olex and Sodena plotters.
Steering and navigation is taken care of by a Navitron NT921 MKII digital autopilot with duplicate levers at the forward wing consoles and aft at the trawling station.
Communications and safety equipment includes a JRC JSS-2150 MF/HF GMDSS SSB radio telephone, Sailor and Icom DSC VHFs, Entel HT649 GMDSS handheld VHF, and JRC Navtex receiver.
Woodsons also installed a comprehensive CCTV system. Four of the 17 HD cameras provide comprehensive coverage of the engineroom, including one that skipper James West can easily and quickly mount wherever it is required, should the need to monitor a specific item of machinery arise.
Westro’s CCTV system includes an underwater hull camera focused on the propeller, nozzle and rudder. Images from this or any of the other cameras look particularly impressive when displayed on the large screens.
Scanmar UK supplied and installed the twin-rig double-distance monitoring system that James West is now using to provide optimal levels of fishing efficiency, both in terms of gear spread and fuel economy.
Information supplied by three Scanmar SS4 sensors, operating via the popular ScanMate bridge system, together with flow sensors, provide constant numerical and graphical updates of the middle clump’s position in relation to the trawl doors.
Poseidon Navigation Services Ltd of Buckie supplied Westro’s requisite charts and publications, along with the compass located in the floor of the wheelhouse, to port of the skipper’s seat, from where it can be easily viewed.
Airo-Tech Solutions Ltd – new fishroom refrigeration system

The machinery for Westro’s evaporator fan-based fishroom refrigeration system, installed by Airo-Tech Solutions Ltd of Fraserburgh, is housed in a dedicated walk-in room on the main deck…
The evaporator-type refrigeration system fitted in Westro’s fishroom was designed, supplied and installed by the Fraserburgh company Airo-Tech Solutions Ltd. Managing director Ryan Summers had previously done some work for skipper James West on Golden Sceptre, when options for the pending new-build were

… together with a Geneglace 1t ice machine…
discussed.
Fishroom chilling on Westro is provided by three large-capacity evaporator fans with automatic defrost, mounted in a single unit on the forward bulkhead of the fishroom. Although this type of system is not by any means new technology, it is increasingly viewed as being better and more effective than chilling pipes.
The high level of efficiency delivered by the evaporator system on Westro was immediately shown on commissioning, when after being switched on while the fishroom was at 8°C, within 20 minutes the temperature throughout the fishroom had dropped to -2°C, the normal preferred working temperature.
Two hours later, the fishroom was at -15°C. While well below the requirements of skipper James West, this extremely low temperature proved the power of the system and its capability of comfortably maintaining a full fishroom at -2°C while adding in factors such as an open hatch, lighting load, and crew entering and working.
A fan-based evaporator system delivers the benefit of constant and effective cooling of catches from top to bottom of each tier of boxes, to ensure optimum levels of catch quality on landing.
Achieving consistent catch temperature in a conventional deckhead piped system is more difficult, as when the fishroom is full, the bottom boxes do not always get the required cooling effect, while some of the top fish can freeze and grow hard.
The cooling effect of pipework can also be jeopardised when the pipes ice up due to the moisture content in the fishroom, with the result that the system can be working at a very low capacity and be unable to prevent temperatures rising.
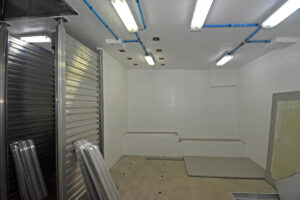
… from which flake ice descends into a central locker in the fishroom.
The system on Westro eliminates this by automatically defrosting four times a day for around 30 minutes, to ensure maximum heat exchange across the system and constant effective cooling of catches.
Evaporator systems are also reported to be more energy-efficient than piped installations, as the greater cooling power means that the plant only needs to have been switched on for 30 minutes in order to reach the required temperature – normally 0°C to -1°C before hauling for the first time at the start of a trip – rather than when leaving harbour, possibly up to 12 hours earlier.
Ryan Summers also installed a Geneglace F30M flake ice machine, from which the daily output of 1t is expected to last longer, due to the capabilities of the vessel’s fishroom refrigeration system.
Ryan Summers said: “I thank James for taking the opportunity to go with this type of system, and perhaps taking a leap of faith in bucking the trend on the typical fishroom set-up. I know that the owners are very impressed with the initial results, so I am looking forward to hearing about the catch quality when Westro lands for the first time.”
Airo-Tech Solutions is scheduled to install similar refrigeration and ice-making systems on the new 19.2m scalloper that Macduff Shipyards is currently building at Buckie for delivery to Whitelink Seafoods Ltd of Fraserburgh in a few months’ time.