Two gear technologists from New Zealand completed a whistle-stop tour of the UK at the end of last month, discussing the potential uses of their novel codend technology – which has now become widespread in the Kiwi fishing industry – in a wide range of different UK fisheries.
The new technology was featured in FN earlier this year, during trials aboard a Dutch beamer by scientists from the University of Wageningen. Martin de Beer and André Pinkert of Precision Seafood Harvesting say that the concept they’ve developed, which they refer to as the Modular Harvesting System (MHS), can be widely varied to take account of very different fish behaviours and fishing practices.
“Precision Seafood Harvesting was set up by New Zealand’s three largest fishing companies,” they told FN, “and originally the focus of this gear was on maximising catch quality. It was only further down the line that we realised just how positive an impact this could also have on improved selectivity and discard survival.
“In the New Zealand hoki fishery, we were seeing a lot of fish being damaged – it’s a very soft fish, caught at depths down to 800m, and a lot of otherwise prime-quality fish taken was being crushed and was destined for fishmeal.
“The original concept of the MHS was to provide a stable environment in the trawl that prevents the fish from being crushed. Successful early trials with the design led to the creation of Precision Seafood Harvesting as a stand-alone business, with $21m of industry money, matched with NZ$21m of New Zealand government funds invested into developing and trialling commercially viable fishing gears from the concept. On top of that initial $42m, we’ve now committed additional funds to scale up production for the international market.”
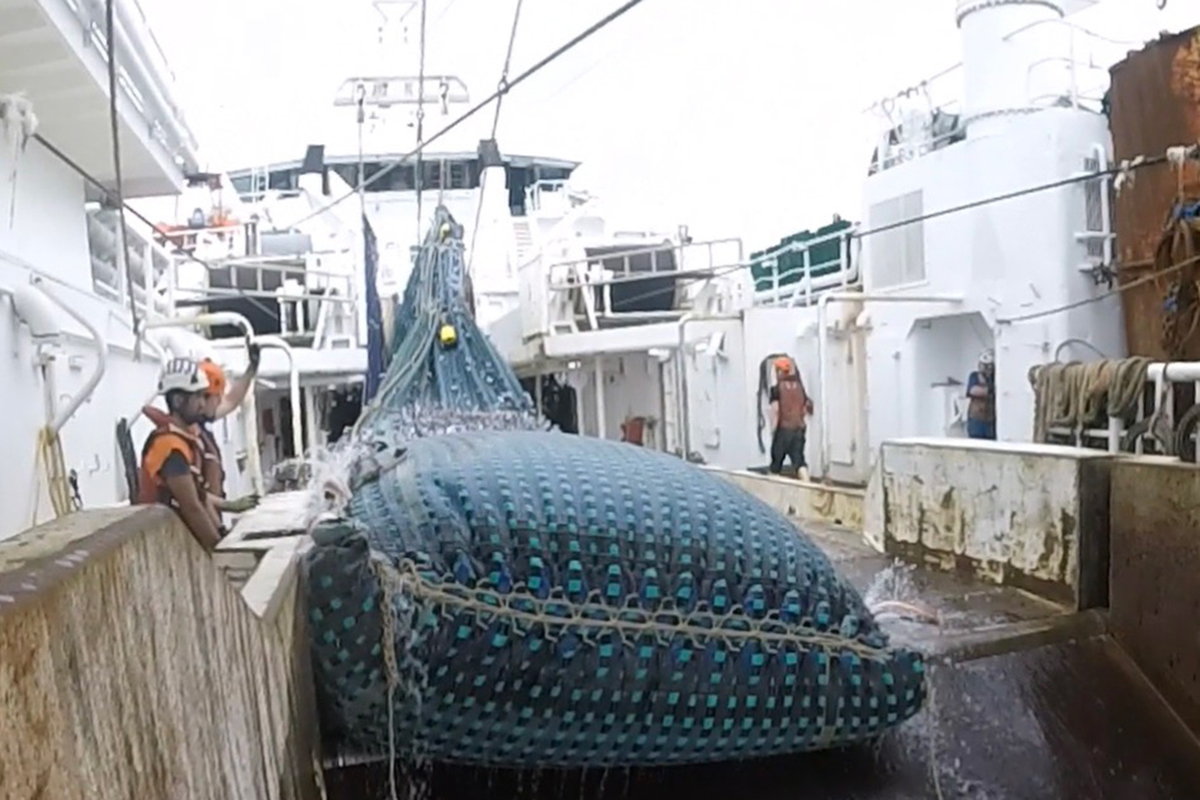
The MHS in now standard kit in the New Zealand hoki fishery, where a fleet of 50m to 64m freezer trawlers work in depths down to 800m. The lifting bag seen here is full of water – when opened, the fish, which unlike in a conventional trawl are alive, with very little damage, are washed down to the processing deck below. Fillet yields from the catches have risen dramatically since the MHS replaced conventional codends.
“In New Zealand itself, as well as the larger freezer filleters targeting hoki that are using this gear, we’ve got inshore trawlers, down to 12m, using the MHS, which are really seeing the benefits of extra selectivity, and which are also showing how flexible and adaptive the MHS can be for an individual fishery,” they said.
“The trip we have had to the UK, ahead of visits to the Netherlands, Norway and Denmark, has been really useful. We’ve been able to discuss it with skippers and vessel managers of beam trawlers and stern trawlers in Devon and Cornwall, Scottish and Northern Irish prawn skippers, whitefish skippers, and have learned at first hand about a range of different fisheries in the UK that could certainly benefit from adapting the MHS to their particular fisheries.”
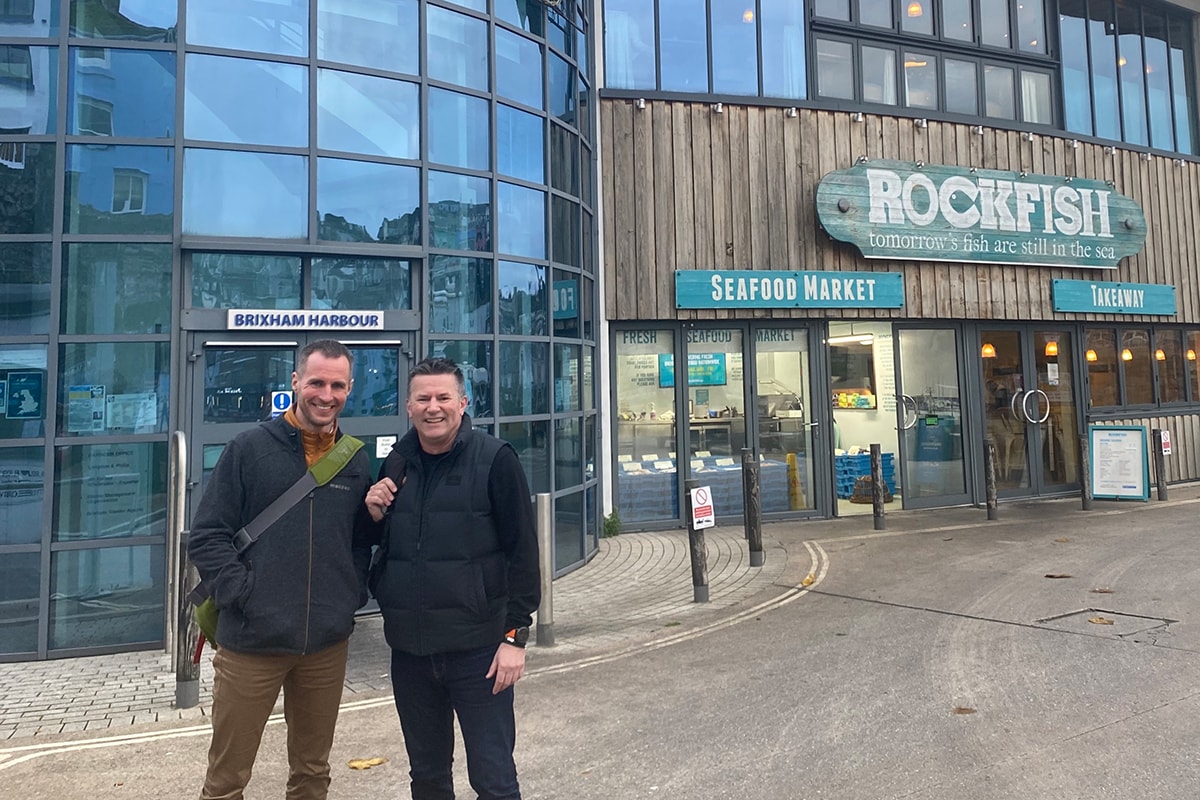
André Pinkert and Martin de Beer in Brixham, where they met a number of beam trawl skippers, vessel owners and Seafish staff.
“We’ve learned over the last three years how small changes to the make-up of the gaps in the MHS panels can have large influence on fish behaviour and escape reactions, and tailor the design to each fishery,” they continued. “It means that if, for example, a new ‘zero TAC’ species enters the mix, it could be possible to amend the net to allow this fish to exit the gear, through a combination of the shape, slot size and position, without losing other species that you want to retain.
“Then, on top of this, is the improved survivability of fish hauled onto the boat, and vastly improved catch quality. In New Zealand, we saw survival rates of small snapper retained in the net of 86% after 48 hours, compared to just 24% when compared with a conventional codend.
“Dutch scientists working with the beam trawl fleet saw an 11-fold increase in survival of discarded plaice, and six-fold of turbot, even during a summer trial that saw record high water temperatures that were likely placing the fish under additional stress.”
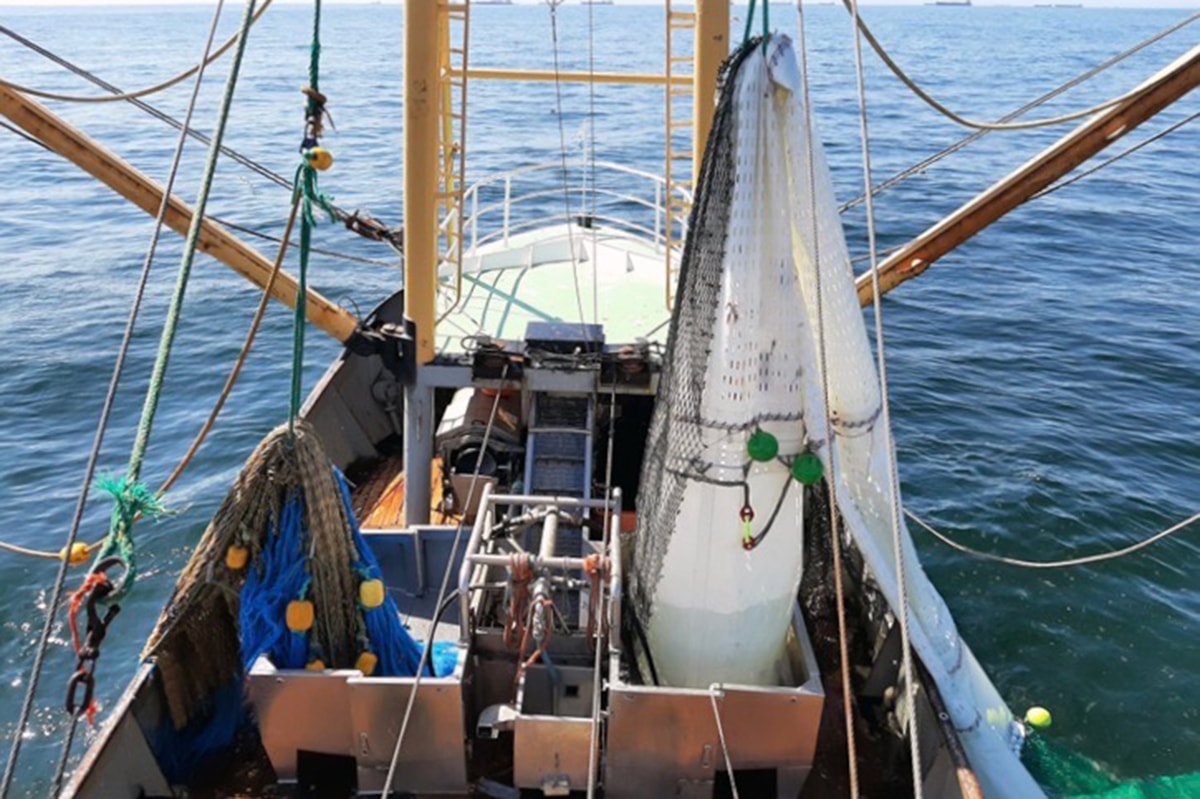
Emptying the conventional beam trawl and the Kiwi pit during trials undertaken with scientists aboard. The full lifting bag of water in the MHS is clearly visible. The quality of the sole caught in the new gear was, said one fisherman involved in the work, ‘quite incredible’.
“We’ve been really pleased with the many conversations we’ve had around the UK, supported by Seafish, which is now looking at putting together a full project proposal, where we can build and test protypes at sea,” they continued.
“One lesson we have learned from New Zealand – and a reason why we’ve also already met with scientists from Cefas and officials from Defra – is the need for regulation to keep up with the evolving technology. In New Zealand, we were fortunate in that the government quickly adopted some innovative regulations that allowed for early trials of alternative types of fishing gear.
“It is vital, in our experience, for regulators to adopt fishing gear regulations that are less prescriptive and more enabling, and not to get bogged down in ever lengthier sets of rules detailing every aspect of what makes a trawl legal.
“We had a really interesting week in the UK, and we’d like to thank everyone across the country who helped make the visit a success. We’ll be looking forward in due course to working with fishermen to adapt the MHS for use in British fisheries.
“We are confident that the environmental and financial benefits from successfully adapting the system for British species and conditions will be as positive as they have been for our fishermen in New Zealand.”
Counter-intuitive – but it works!
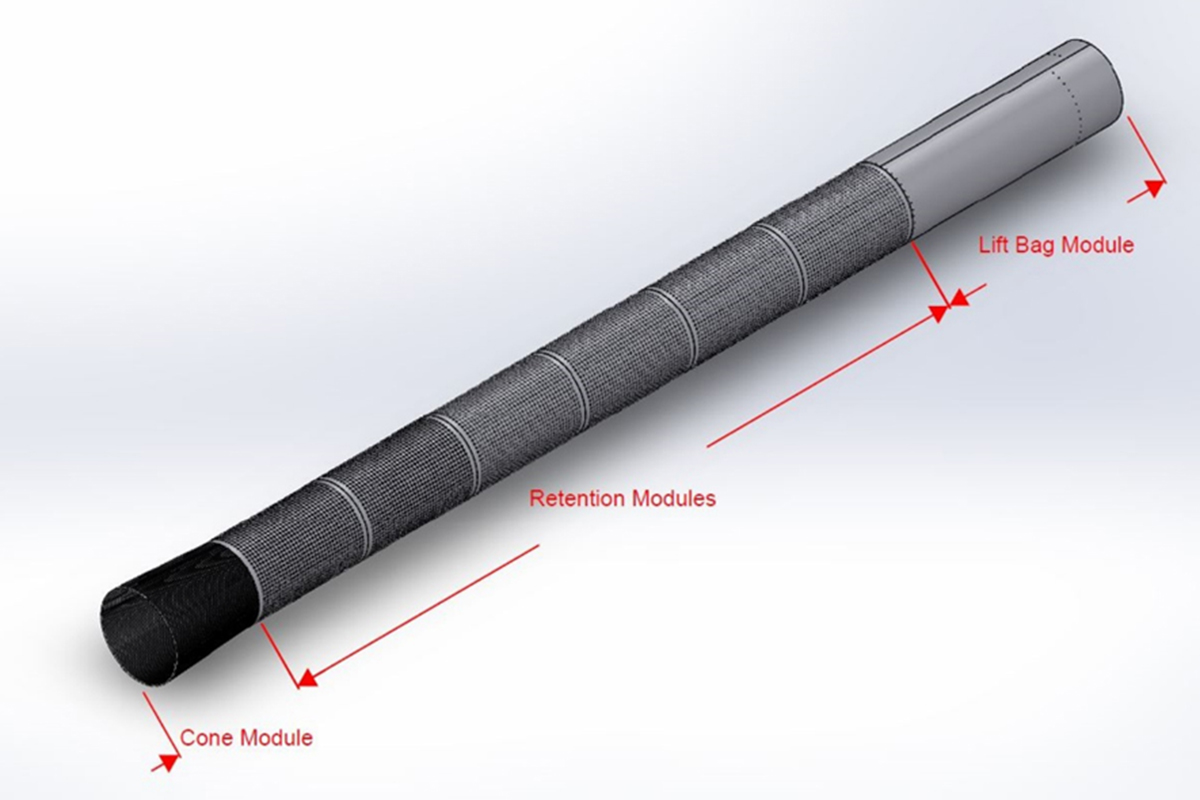
The Modular Harvest System (MHS) works by replacing the final section of a conventional mesh trawl with solid sheeting, into which slots or holes can then be placed. Although the material can easily be wound onto existing net drums, when shot away and filled with water, it retains its shape during a tow, and will not collapse straight away if, for example, a door becomes fast.
Within the MHS, waterflow will vary from close to zero, up to whatever towing speed the skipper has chosen, depending on the positioning of the various slots and escape panels. This means that fish within the MHS can naturally gravitate to the areas of flow that they prefer, quickly recovering from the exertions of trying to avoid entering the mouth of the trawl.
The nature of the codend means, too, that it remains full of water when hauled, with the fish remaining free-swimming, until the codend is emptied into a container on deck. There is therefore no crushing, no meshing of fish in the codend, and much less decompression damage to fish, even when hauled from depth.
In many vessels that are now working the MHS full-time, discarded fish can even be ‘swum’ back into the sea from the tank where the codend is emptied, reducing work for the crew, and further reducing the stress on juvenile fish or unwanted bycatch.
Kiwi fishermen report that fuel consumption with the new system is pretty much the same as with conventional codends, which also create a ‘blowback’, especially after codend meshes become blocked with exhausted fish, that creates almost as much drag as that of the MHS, but without any of the positive benefits for the fish.
The trial earlier this year on the Dutch beam trawler Catherina KW-145, however, saw a marked reduction in fuel consumption, due to reducing towing speed from 6k down to 4.5k. Although this was originally done by skipper Geert van der Plas to try to get the gear to behave correctly on the seabed, he subsequently noticed that he had seen no drop in catch rates compared to the conventional beam trawl towed at 6k for the trial to compare the two gears.
More details of the MHS can be found at here.