The continual evolution in vessel design and specification was further advanced earlier this month when the dedicated 27.55m fly-shooter Tranquility LK 63 arrived in Shetland, reports David Linkie
Berthing the state-of-the-art vessel in Symbister harbour for the first time was a proud occasion for the shareholders of the Tranquility Fishing Company. A large crowd of family and friends gathered on the quay to welcome the new seine-net boat home, providing a timely reminder of the vitally important socio-economic benefits that the local whitefish fleet generates throughout Shetland, and in particular on the small island of Whalsay, where fishing is very much the lifeblood of the community.
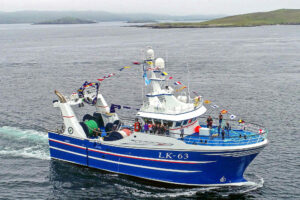
Tranquility approaches Whalsay for the first time, with flags flying proudly after family and friends boarded the fly-shooter at Lerwick. (Photo: Ivan Reid)
While Tranquility will operate with a seven-man crew, it is worth remembering that well over 10 times that number of people, including fish processors, supply personnel, office staff, local shopkeepers and school teachers, in addition to the crew’s families, will be either directly or indirectly associated with the seine-netter, in one way or another, for years to come.
Designed and built by Vestværftet ApS of Hvide Sande, Denmark, Tranquility hit the ground running by landing over 700 boxes of prime-quality whitefish, spread across three landings into Scalloway and Lerwick over five days, during which time skippers Stuart Anderson and David ‘Rodney’ Reid, together with crewmen John Johnson, Robbie Jamieson, Chris Shearer, George Eunson and Magnus Polson, were highly impressed by the performance level of the new boat, including the ease of working the gear and the efficiency of the catch-handling system.
Tranquility’s skippers and crew expect to work fairly short trips, including daily at times if fishing just a couple of hours off, as can be fairly commonplace in Shetland, before landing into either Lerwick/Scalloway, or Cullivoe if working north.
Working through Lerwick agents LHD Ltd, and insured by British Marine, Tranquility’s catches will be sold electronically on the Shetland Seafood Auction.

Tranquility skippers David ‘Rodney’ Reid and Stuart Anderson.
While landing a successful 40-hour first trip, which yielded 290 boxes at Scalloway two weeks ago, skipper Stuart Anderson said: “We are extremely pleased with the way in which Tranquility has initially performed. It is also pleasing to see that the boys have quickly got into the swing of things in terms of a completely new way of working the gear. Thanks for this seamless transition go to skipper Andrew Bremner and the crew of the Wick seiner Boy Andrew, who gave the boys the opportunity to work with them to experience a similar style of boat. Local Shetland skippers have also provided invaluable help, so sincere thanks to all.
“While the new boat is designed to give a totally different way of fly-shooting than her predecessor, which stood us in good stead and paved the way for this one, the overall aim was to replicate the fishing capabilities of our previous boat with a new build, incorporating the latest design, fishing and propulsion technologies. This will enable us to operate with enhanced levels of efficiency and safety for years to come, when landing premium-quality fish caught on the same grounds and with similar trip patterns as previously.
“From the initial contact with Ove Kristensen and his team at Vestværftet ApS, the design and build process went extremely smoothly and was an enjoyable experience. In terms of first impressions, the result speaks for itself. Now it is up to us to prove Tranquility’s year-round fishing capabilities, which we are looking forward to.”
Built to replace a 32-year-old seine-net boat of the same name, the new Tranquility represents a major step forward for a close-knit and youthful crew who, although already well-experienced, still have most of their fishing careers ahead of them.
Healthy and sustainable stock levels, high levels of market demand for prime-quality whitefish, increased levels of safety, efficiency and catch quality, and the lower maintenance costs associated with a custom-designed new boat, were among the reasons the owners gave for their decision to order a new boat that would help them to consolidate their fishing careers for the long-term benefit of their families, as well as the fishing-dependent community they live in.
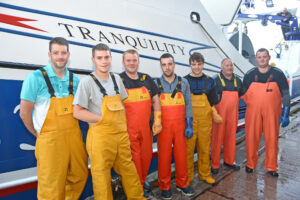
Stuart Anderson, David ‘Rodney’ Reid, John Johnson, Robbie Jamieson, Magnus Polson, George Eunson and Chris Shearer hit the ground running by landing over 700 boxes of whitefish in the first five days of fishing.
After the partners’ initial contact with Ove Kristensen of Vestværftet ApS, the design of the new boat gradually evolved to meet the owners’ specific requirements. These included mounting the large power reels, on which some 10t of seine-net rope is spooled, on the shelterdeck, rather than being partly recessed into it. This provides optimum line of sight, while also maximising storage room throughout the vessel.
To provide enhanced levels of vessel stability, the beam was increased to 8m at the same time as the heights of the stem, forecastle deck and wheelhouse were raised, in a completely new hull design that has a registered length of 23.98m and a shelterdeck moulded depth of 6.24m. Further evidence of the deep hull form is shown by the forward and aft drafts of 4m and 5.2m respectively.
Extensive liaison between the owners and builders has resulted in maximum use being made of the internal space available throughout Tranquility, on which catches are bagged aft, at the starboard quarter.
The extended forecastle deck provides an extensive full-height storage area, forward. In addition to mooring/tow ropes etc, this area features deep storage ponds for spare fishing gear, in addition to a chest freezer. A wide assortment of fishing hardware, netting and balls of twine are racked securely down the portside walkway in this area.
Maximising propulsion and towing efficiency, in order to deliver optimum levels of fuel economy, was a key factor in the design process. Consequently, Tranquility features a slow-running (1060rpm) Mitsubishi straight-six main engine, Hundested 8:1 reduction gearbox and a large (2,780mm-diameter) CP propeller turning in a matching high-efficiency nozzle. Tranquility returned an average top speed of 12 knots on engine trials, and tows at a propeller pitch setting of around 40%, using around 60 litres of fuel per hour, depending on sea conditions. This immediately highlights the benefits of the selected centreline package, together with the new deep round bilge hull form developed in-house by Vestværftet ApS.
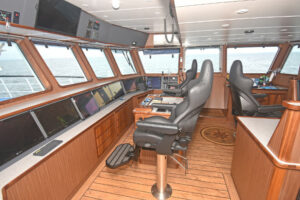
Stylish wheelhouse interior.
The choice of a controllable pitch propeller turning at a constant speed also enables the seiner’s main load-sensing hydraulic system to be driven off two gearbox-mounted PTOs.
Up to 18 coils of 46mm seine-net rope can be worked from the automated power reels set into the shelterdeck immediately abaft the wheelhouse. Three types of seine nets can be worked from three sets of split net drums positioned towards the aft end of the shelterdeck.
General layout
The hull below the main deck is subdivided into five watertight compartments: forepeak; tank section with deep fuel tanks port and starboard/thruster compartment; insulated fishroom; engineroom; and aft peak housing fuel, lube and hydraulic oil tanks as well as the steering gear compartment.
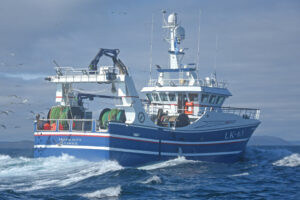
Starboard quarter view of Tranquility showing the three stainless-steel-framed gear openings across the transom and the bag hatch to starboard.
The main accommodation areas are arranged across the forward section of the main deck.
Abaft the forepeak, which provides generous storage for provisions, a well-equipped and open-plan galley is arranged on the portside, opposite a spacious messdeck/TV lounge where bench seating is arranged around two tables.
From the messdeck, a central passageway gives access to two three-berth cabins to starboard and in turn to the crew changing area, in which washing and drying facilities are available, in addition to full-height storage lockers. Two twin-berth cabins line the port side of the hull in this area, which also includes a large shower/toilet room.
All internal accommodation areas on Tranquility are finished to an extremely high standard, using rich walnut laminates and timber facings, to give an attractive and homely feel which is appreciated by the crew. Unobtrusive low-level blue illumination is fitted throughout the accommodation areas, on the stairwells and in the wheelhouse to enhance safety at night when the main lights are switched off.
Two further compartments housing 2.5t Buus ice machines are situated on the main deck, aft of the forward casing.
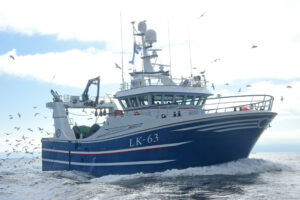
Tranquility features a customised new hull design to meet the owners’ specific requirements.
An extensive catch-handling system, supplied by VCU of Urk, is arranged across the full beam of Tranquility between the forward accommodation casing and the large catch-reception hopper at the starboard quarter. Capable of holding around 250 boxes of whitefish, the fish hopper is flanked by a well-equipped workshop positioned against the transom to port, aft of a secondary wet gear drying room and WC compartment. The workshop is directly accessible via an easy-access companionway leading up from the engineroom. The space under the sloping base of the catch hopper is ponded out to store spare filters for the engineroom machinery, further illustrating the maximum use that has been made of all available space.
In addition to the returned stairwell connecting the wheelhouse to the main deck, a room housing all the computers and related hardware for the wheelhouse electronics is located on the first half-level down. This facility ensures that all the hi-tech electronic equipment is readily accessible at all times, without the need to dismantle any of the wheelhouse consoles.
Fishing arrangements
Thyborøn Skibs and Motor A/S (Three J’s) supplied Tranquility’s bespoke deck machinery package and also designed the hydraulic system.
Designed and built to the designers’ and owners’ specific requirements, the hydraulic deck equipment includes two power reels from which seine-net ropes are worked. With a core pull rating of 18t and spooled with 3,300m (15 coils) of 46mm-diameter seine rope, the power reels are mounted on the shelterdeck abaft the forecastle bulkhead, with further protection provided by the extended sides before they sweep down towards the gunwale rails amidships.
The reels are driven by Poclain Diamond two-speed motors that give hauling speeds of 12 and 26rpm. In order to give full movement of the spooling-on gear across the width of the power reels, the operating hydraulic cylinders extend across the aft face of the adjacent unit to give an integrated full-width structure across the vessel’s beam. A central companionway leads down from the forecastle deck abaft the wheelhouse to the shelterdeck.
With maximum and core diameters of 2,258mm and 394mm respectively, and 2,066mm wide, the reels are controlled from the fishing console in the wheelhouse using a customised computer system supplied in-house by Thyborøn Skibs and Motor A/S. Skippers Stuart Anderson and Rodney Reid are impressed with the ease of use and functionality of the system.
The Three J’s system provides a constant display of hauling speed, hydraulic pressure, tension, rope length and the differential between port and starboard warps. When the selected differential is exceeded, the reel on the longer side is automatically slowed down in order to keep the port and starboard ropes level in the water astern, before reverting to the chosen rate. The system also caters for four modes of operation – towing, stopped, heaving and shooting. When shooting away the ropes, the main motor is disengaged, allowing the power reels to freewheel, with a smaller hydraulic motor being used to apply a slight braking tension to prevent the rope from jumping.
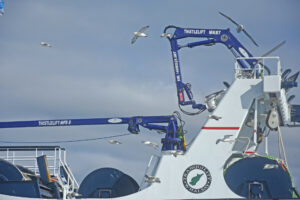
Thistle Marine of Peterhead supplied kinked- and fixed-boom deck cranes that cover the working deck.
The 46mm-diameter seine-net ropes are usually run off at 300m per minute. This equates to one side of rope being shot in just 12 minutes.
On picking up the Dahn, the preferred towing mode is selected – either constant reel speed in rpm or constant rope speed in m/min. Most Danish skippers generally favour constant reel speed.
In this mode, the rate of heave gradually increases as the core diameter of rope on the drum builds up. For the first coil, with the reels turning at 12 revolutions per minute, the ropes are heaved at a rate of 15-20m per minute, slowly increasing towards 55m/min.
When the ropes close up, heave mode is employed, typically with around 1,500m of rope on the reels, before the last few coils come in at up to 200m per minute.
When the first side of ropes are being shot, they are led directly aft above the net drums to fixed hanging blocks on either side of the gantry, from where they are directed downwards to a sheave mounted on the gunwale rail. As the seine net is shot off the drum, trawl-style, at the same time as the last coils of rope are running, a quick release is used to connect the rope to the stainless steel Danleno and the sweeps. All the hardened blocks and sheaves, which are mounted in galvanised housings, were manufactured by Blue Line.
When heaving back the ropes, they lead over movable hanging blocks mounted on the underside of the aft-raked stern gantry before passing over the fixed blocks. The movable blocks are positioned remotely from the wheelhouse by a hydraulic motor mounted on the portside of the gantry, which drives a large sprocket wheel and a heavy-duty chain. This arrangement enables the skippers to select and adjust the optimum towing position for the gear in relation to the prevailing tide and weather conditions.
Two sets of 2 x 12t split net drums are positioned across the end of the shelterdeck, in line with openings across the transom fitted with tubular section stainless frames to protect the seine. The starboard drum is set slightly further forward, allowing for the bag hatch on the quarter.
Similar arrangements are in place on the opening that straddles the vessel’s centreline. This serves a third 2 x 12t split net drum set forward of the other two units. The middle unit is primarily intended for hauling back a wing in the event of torn gear, when it can be stretched out for repair before being taken back on to the working drums.
All three split net drums are fitted with equalising values. These can be engaged at any point when hauling or shooting, to ensure that the sweeps and net are worked evenly.
The codend is lifted aboard at the starboard side of the transom using a 9t Gilson winch mounted on the aft face of the fishing gantry directly above the reception hopper.
A Thistle Marine MKB7 short-post kinked-boom crane, fitted with power block and 2t auxiliary winch, is mounted on the centreline of the trawl gantry to assist with general gear handling.
Catch-handling
Tranquility is equipped with a highly-automated whitefish handling and electronic catch management system, designed and fabricated by VCU of Urk, Holland to deliver optimum levels of catch quality and full traceability for years to come, while minimising the amount of manual effort required by the crew.
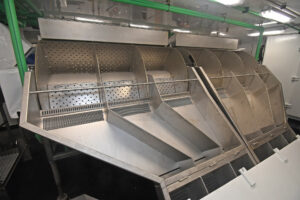
A KM MK II gutting machine is incorporated into the fish-handling system.
On being released into the stainless steel reception hopper, which can hold around 250 boxes of whitefish, catches are moved forward by an elevated conveyor positioned to starboard before being transferred to a second conveyor leading across the full width of the main deck.
Crewmen select and gut the catch from the waist-height transverse conveyor positioned forward of the aft deck casing.
After gutting, larger fish are placed into one of two large revolving stainless steel drums, with horizontal axes, housed in watertight troughs arranged parallel to, and forward of, the fish selection conveyor. Both independently-operated drums are divided into nine sections, three each transversely and radially. After an adjustable length of time, during which fish in the receiving section are sprayed with water, the drum is automatically rotated through 120°. As a result, the fish are then fully immersed in water at the bottom of the trough and washed thoroughly, for the selected time, after which the drum rotates through a further 120°.
This second movement lifts fish clear of the washer, and they slide across short drainage shelves before being automatically transferred by one of six stainless steel chutes down to the fishroom via dedicated coamings in the main deck, tight to the aft deckhead of the accommodation casing.
Further selections of, generally smaller, fish are made into elevated bins, from where they are released into the main system directly below. Less frequent selections can also be made into baskets placed in a secure deck rack aft of the gutting station.
Another three selections of fish can be made into a trough between the gutting conveyor and the circular selection drums for delivery to a KM MK II gutting machine positioned towards the vessel’s starboard side.
The fish-handling area is kept clear of water by three Xylem Flygt 4in submersible pumps fitted in deck sumps.
To keep the automated selections made into the revolving fish washers and the gutting machine, seven freestanding vertical hoppers are arranged against the aft bulkhead of the fishroom. Clear Perspex fronts are fitted to each compartment, to allow holdman Robbie Jamieson to immediately see how much fish is in each of the bins, and which ones to focus on first.
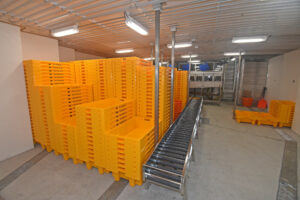
The extensive fishroom ready to receive Tranquility’s first catch.
On being released from the selected hopper, fish are electronically weighed, with part-basket weights stored on the catch management system, before a label displaying all relevant information, including species, grade size, time and date, is printed off and affixed to the end of the corresponding box. This information is also transferred automatically to a PC in the wheelhouse, where it is accumulated to provide a running total of Tranquility’s trips.
Served by a dedicated access hatch and easy-access companionway, located on the port side aft, Tranquility’s fishroom has a working capacity of some 1,100 nest/stack boxes stacked 10 high.
The absence of any terraces further emphasises the amount of space available in Tranquility’s long, flush-floored and parallel-sided fishroom. To maximise efficiency and reduce workload for the crew in a fishroom that – positioned between frame 15 and 39 – is 12m long, baskets of fish, filled from the hoppers at the aft end, are slid forward to the working tier of boxes on a series of rollers. At the start of a trip, six sections of rollers are joined together in a continuous length, before the forward sections are removed as the number of full tiers accumulates.
Ten tonnes of flake ice, made by two 2.5t Buus ice machines positioned in separate compartments on either side of the main deck, aft of the accommodation casing, can be stored in full-height lockers in the fishroom.
The fishroom refrigeration system, which uses stainless steel refrigeration pipes mounted on the deckhead, was installed by Lemvig Maskin og Køleteknik, which is a sister company to Thyborøn Skibs and Motor.
When landing, an electric winch mounted on the underside of the main deck is used to pull stacks of boxes aft towards the portside, from where they are lifted ashore through a large hatch by a Thistle Marine MFB8 stiff-boom crane served by a 2t landing winch.
Engineroom machinery
Tranquility’s aft engineroom, which is characteristic of this design of vessel, features a particularly well-thought-out arrangement ensuring that engineer Chris Shearer has maximum ease of access for all levels of service for years to come.
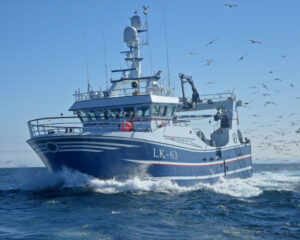
Tranquility steaming at 12 knots.
The Mitsubishi S6U straight-six main engine develops 680kW @ 1050rpm and is coupled to a Hundested CPG 120-2 8:1 reduction gearbox to turn a Hundested 2,780mm-diameter four-bladed CP nickel aluminium bronze propeller mounted in a matching high-efficiency nozzle. The centreline propulsion system is operated through one of three sets of SeaMech electronic engine controls strategically positioned in the wheelhouse.
Two Rexroth load-sensing pumps drive the main hydraulic system via gearbox-mounted PTOs.
An electrically-driven 45kW power pack is used to drive a standby pump, enabling the main hydraulic equipment to be operated at reduced power. This arrangement also allows the deck machinery to be operated in harbour when the crew are either mending or taking on gear, while the driver is carrying out routine maintenance work on the propulsion unit after stopping the engine.
Two Volvo D7AT auxiliary engines, run trip-about, drive 149kVA Newage Stamford 415/3/50 generators. The electrical generators are fully synchronised through the switchboard panels to give load sharing and automated auxiliary start-up.
The engine exhausts are routed up through the starboard leg of the stylishly-raked aft gantry.
A fourth exhaust system, serving a Beta Marine harbour genset that provides electrical power to keep the accommodation areas warmed when Tranquility is berthed in harbour, is housed in the port leg of the gantry.
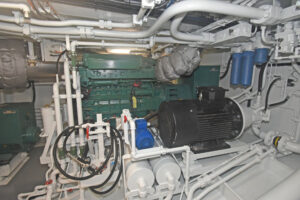
One of two Volvo Penta D7AT auxiliary engines that drive 149kVA Newage Stamford 415/3/50 generators.
Tranquility can start a trip carrying 36,000 litres of fuel, housed in a combination of four main deep tanks (two forward and two aft), together with daily service and two wing tanks in the engineroom. Electronic fuel gauges and a fuel meter are conveniently placed in the engineroom adjacent to the pipe manifolds leading from the various tanks, allowing Chris Shearer to know precisely how much fuel he is transferring,
Freshwater capacity is 27,000 litres. This total includes 12,000 litres in double-bottom tanks under the fishroom floor for domestic use and 15,000 litres in the bulb serving the two ice machines. The 9,400 litres housed in an anti-roll tank located across the vessel’s full beam under the wheelhouse floor can also be used to supplement freshwater supplies should the need arise.
Two Bloksma coolers serve the main engine, gearbox and hydraulics. The Volvo auxiliaries are freshwater-cooled in conjunction with cooling pipes built into the bilge keels.
A hydraulically-operated Hundested bow thruster of 120kW is fitted, to give maximum vessel manoeuvrability in restricted areas.
A particular feature of Tranquility is the extremely low level of noise evident throughout the boat. When steaming at 12 knots during trials, with 95% load on the Mitsubishi propulsion engine, the noise levels in the messdeck and cabins was recorded at 55dB (A). These very low levels, which mean that the main engine is barely discernible, are highly appreciated by the skippers and crew.