Featuring a new concept of bulbous bow and an aft bagging arrangement designed to enhance fishing efficiency, crew comfort and safety, the 24m twin-rig prawn trawler Virtuous FR 253 significantly advances the parameters of divergent thinking on vessel design, reports David Linkie
Built at Whitby by Parkol Marine Engineering, after being designed by Ian Paton of SC McAllister & Co Ltd in close liaison with Fraserburgh father and son skippers Sandy and Alexander West, Virtuous is the result of three years of extensive thinking and planning by everyone associated with the build project.
While the evolution of fishing vessel design is generally acknowledged to be a gradual process, every so often a fresh approach contributes to a markedly new end result – as Virtuous exemplifies.
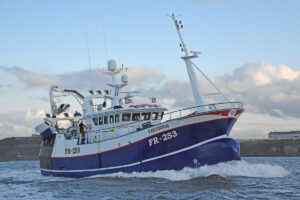
Virtuous leaving Whitby for Fraserburgh.
Having taken the decision to replace the previous 23.3m Virtuous, which has performed consistently well in all aspects since being completed by Parkol in 2010, Sandy and Alexander West started to consider their options regarding gear-handling arrangements.
Essentially, the preference was to make hauling twin-rig trawls a continual – and safer – process by bagging catches aft, rather than taking them aboard forward on the starboard side, while retaining the customary practice of locating two sets of split net drums on the fully enclosed quarter.
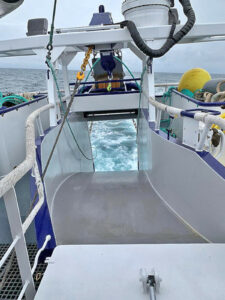
The stern ramp is positioned under the secure box for the middle roller before curving slightly to port.
It quickly became apparent that for this to become a realistic option, what was needed was a ‘blue-sky’ approach to the general layout on the main deck, together with the all-embracing hull design.
Standout features on Virtuous include:
- A high-profile parallel-sided bulbous bow
- A full-length steel shelterdeck with integral Gilson and trawl gantry
- A stern ramp for aft bagging
- Three two-speed 15t split trawl winches
- A 1,000-box fishroom
- Two Ziegra ice machines
- A Simrad wheelhouse electronics package including a twin-rig monitoring system.
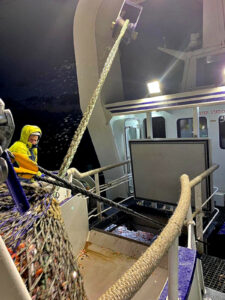
Hauling a codend up the ramp towards the hopper hatch using a block on the integral steel Gilson gantry.
In essence, the convex stern ramp is positioned centrally at the transom, between the net drum openings and below the secure box for the middle clump, before curving slightly to port towards the reception hatch abaft the wheelhouse. Catches are worked up on the port side of the weathertight main deck, parallel to the galley and messdeck, which lie to starboard.
The owners’ drive to achieve these changes was matched by similar levels of motivation, particularly in the Netherlands, to explore new ideas in the bow design of fishing vessels. These were loosely based on the X-bow designs that, in recent years, have become a fairly standard feature on North Sea supply vessels.
Achieving more consistent buoyancy forward, thereby reducing slamming when steaming into weather – which, in turn, contributes to enhanced fuel economy – was the key consideration. After looking at various images of new bulbous bows, it became apparent that these could be incorporated into the hull design without going over 24m LOA.
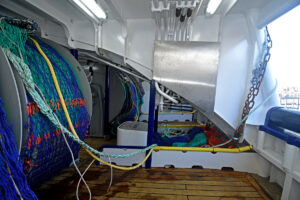
The radiused stern ramp is positioned between the two sets of split net drums on the enclosed quarter.
When conventional bulbous bows are submerged when a vessel is pitching, forward waterplane area is reduced, until it is increased again as the flared bow section comes into play to pick up buoyancy again – at which point the cycle starts to repeat itself.
Reducing the differential in waterplane area at the necking point between the bulbous bow and the overhanging forward flare – i.e. creating more consistent buoyancy – was identified as the main aim. While X-bows usually retain fine sections in their characteristic long slope and reverse flare profiles, it was decided that a parallel-sided high-profile bulb, the sides of which were well filled out in plan view, and continued up to directly meet the stem flare, would be the most effective solution in terms of delivering consistent forward buoyancy.
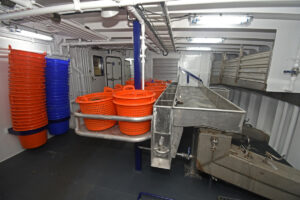
General view of catch-handling arrangements on the port side of the main deck.
Initial indications are that the new form of bulbous bow is proving highly effective. Skipper Sandy West and crew report that Virtuous refused to slam during some testing weather on its maiden trip, when the vessel handled comfortably regardless of which direction it was towing relative to prevailing conditions.
Insured by Sunderland Marine and working through Westward Fishing Company Ltd, Virtuous is expected to work six- to seven-day trips to the North Sea grounds before landing into Fraserburgh. Whole langoustine will be distributed to prawn processors locally and further afield, with tails going to Moray Seafoods of Buckie.
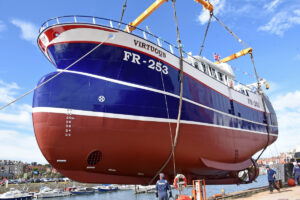
Virtuous features a new form of parallel-sided high-profile bulbous bow.
After fishing a successful maiden trip southeast of Shetland, which included some fairly poor early winter weather, with wind speeds of up to 40 knots, skipper Sandy West said: “Virtuous handled some testing conditions well, and immediately started to show her seakeeping capabilities. Early indications are that she will be an extremely comfortable sea boat, which was one of our main objectives.
“Although it’s early days, in my mind there is no doubt that the new style of bulbous bow is a major contributory factor to the first-class seakeeping qualities we are now benefiting from. Full credit for this – together with the new aft bagging arrangements – goes to designer Ian Paton, for applying divergent thinking to our initial requests and turning them into reality.
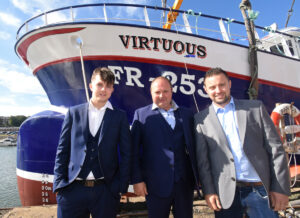
Sandy West with his sons Aidan (left) and Alexander on launch day.
“The Parkol team also deserve particular credit for ensuring a very smooth build programme for what was a very different hull design. As well as being extremely amenable to suggestions, the team managers kept in constant touch to ensure that they delivered exactly what we required, every step of the way.
“The quality of build, machinery installation and internal finish is self-evident. A lot of people, including my family and crew, as well as the companies, contributed to the end result, so sincere thanks to everyone involved.”
Of round bilge hull form, Virtuous has main dimensions of LOA 24m, registered length 23.1m, beam 7.8m, moulded depth 4.25m, draught 5m and GT 242t. Incorporating a continuous wine-glass-shaped skeg similar to that characteristic of wooden-hulled vessels, the vessel’s full beam is virtually continued to the transom, in order to meet the requirements of the new stern bagging arrangements.
General arrangement
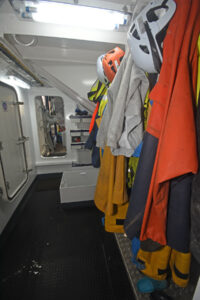
The fore and aft passageway is situated between the deck casing to starboard and the port side catch hopper.
Virtuous features a customised layout on the main deck in line with taking the codends aboard aft.
A full-width bulkhead incorporated into the aft end of the steel deckhouse separates the forward catch-handling area from the quarter. The weathertight deck shelter is fully constructed in steel from the transom to the stem.
The deckhouse extends to the vessel’s centreline from the starboard side of the hull, and from the aft bulkhead to forward of amidships.
A wide passageway lies to port of the centreline, between the reception hopper and the deckhouse. In addition to providing heated oilskin storage facilities, this passageway gives access to a general storage room and the accommodation areas, as well as to the engineroom via a trap in the main deck.
Separate shower and toilet facilities are positioned towards the aft end of the deckhouse off the central lobby, which also includes washing and tumble-drying facilities in an open-plan area.
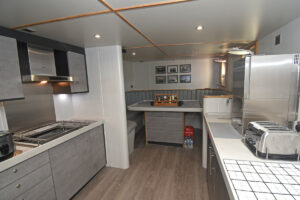
Two views of the stylish galley…
A well-equipped modern galley, which includes four below-bench fridges and freezers, is positioned aft of the adjoining messdeck. Reflecting the owners’ longstanding association with fishing, photographs of six previous family boats, spanning some 60 years – Virtuous FR 353, Quiet Waters FR 253, Gracious FR 167, and three Virtuous FR 253s – are displayed over the mess table.
On the port side of the main deck, the catch-handling system runs parallel to the deckhouse.
Three split trawl winches are mounted forward of the fishroom hatch and the adjacent secure basket deck racks.
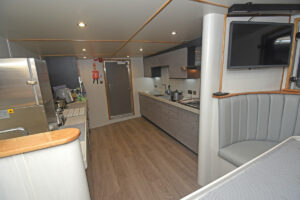
… and messdeck, situated along the starboard side of the hull amidships.
Below main deck level, the layout of Virtuous from forward follows the accepted norm of forepeak and chain locker, thruster compartment, fishroom, engineroom and accommodation cabin.
The layout and finish of the main accommodation cabin down the aft stair was also given extensive thought, in order to maximise the considerable space available and give a modern appearance. Eight deep bunks, together with generous locker storage and bench seating, are provided in what, while essentially an open-plan layout, is effectively subdivided by round-ended panels to give discrete areas.
All internal accommodation areas on Virtuous are finished to an extremely high standard, using a combination of solid timber and light-coloured co-ordinated modern materials to give an attractive and homely feel.
Engineroom
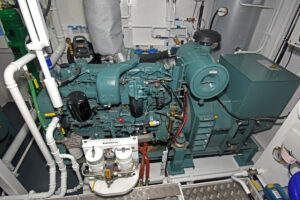
One of the two Mitsubishi 6D16T auxiliary engines, which drive 125kW Stamford 415/3/50 generators.
Virtuous features an extremely well-laid-out engineroom, ensuring maximum accessibility for routine weekly servicing and longer-term service requirements.
Padmos of Stellendam in the Netherlands further strengthened its association with Parkol Marine Engineering by supplying and commissioning the four Mitsubishi main and auxiliary power units installed in the engineroom of Virtuous.
Dedicated solely to propulsion duties, the Mitsubishi S6R2 T2-MPTK-3 main engine develops 555kW @ 1,350rpm, and is coupled to a Reintjes WAF 474 7.476:1 reduction gearbox.
As part of the vessel’s fully integrated hull and propulsion package, Ian Paton also designed the customised 2,500mm-diameter four-bladed propeller and modern high-thrust, low-drag nozzle, fabricated by Parkol Marine Engineering.
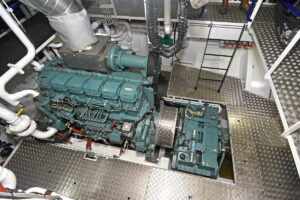
The Mitsubishi S6R2 T2-MPTK main engine and Reintjes 7.476:1 reduction gearbox.
Engine and fishing trials demonstrated encouraging results with the stern gear, which was machined by Premier Engineering of Scarborough and is fitted with lip seals, delivering a very smooth and quiet performance in all operating modes, and strong towing performance.
The centreline combination, together with a single rudder, gave Virtuous an average top speed of 10.6 knots on sea trials.
A Mitsubishi S6B3 variable-speed auxiliary engine (335kW @ 1,350rpm), mounted on the port tank top, powers the deck machinery hydraulics through a JBJ splitter box driving two Kawasaki load-sensing 115kW pumps.
An electrically driven 45kW power pack is used to drive a load-sensing hydraulic towing pump, as well as to provide back-up hydraulic power. This arrangement also enables the deck machinery to be operated in harbour, when the crew are either mending or taking on gear while routine maintenance work is carried out on the main engine.
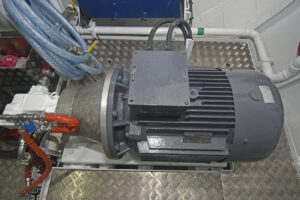
A 45kW power pack runs the secondary hydraulic system.
Installation of the vessel’s hydraulic system was completed in-house by Parkol Marine Engineering, with stainless steel piping being used throughout.
A hydraulically powered Kort bow thruster of 170kW is fitted to give maximum vessel manoeuvrability in restricted areas.
Electrical supplies on Virtuous are provided by two Mitsubishi 6D16T auxiliary engines of 105kW @ 1,500rpm, running 125kVA Newage Stamford 415/3/50 generators.
Cooling for all four engines and the hydraulic system is provided through NRF box coolers arranged across the forward end of the engineroom. CuNiFe (copper/nickel/iron alloy) piping is used extensively throughout the engineroom.
One Victron 80-amp charger is fitted to charge the three sets of batteries in the engineroom. A similar Victron charger is situated in the wheelhouse to serve the lighting batteries, in addition to a 50-amp GMDSS charger.

An electric-drive winch mounted on the underside of the shelterdeck is used to pull stacks of boxes toward the fishroom hatch when landing.
Pearson Electrical of Hull was subcontracted by Parkol Marine Engineering to undertake the electrical installation work on Virtuous, alongside the boatyard’s own electricians.
Sea chests, valves and associated pipework on Virtuous are protected from mussel growth by a Sonihull ultrasonic generator supplied by NRG Marine. Accumulations of mussels can gradually reduce the supply of seawater going to a vessel’s cooling systems and the fishroom chilling plant. Every time this happens, a boat has to be slipped in order for the sea cocks to be removed and cleaned, incurring lost fishing time and additional maintenance costs.
The Sonihull system works by producing bursts of ultrasonic energy in multiple frequencies, to create a pattern of alternating positive and negative pressure. Microscopic bubbles are created by the negative pressure, while the positive pressure implodes them, forming vapour cavities known as cavitation. The result of the implosion is a micro-jet action that achieves a cleaning effect on the hull’s surface below the waterline. It also resonates and destroys single-cell organisms such as algae.
Disrupting this first link in the food chain keeps the surface clean, and makes it a much less inviting habitat for larger organisms that feed on algae. The microscopic movement of water also prevents barnacle and mussel larvae from embedding on the surface.
Twin wing tanks in the engineroom and a single double bottom tank under the fishroom floor allow 22,000 litres of fuel to be carried. A forepeak tank holds 17,000 litres of freshwater.
Working arrangements
EK Marine Ltd of Killybegs designed, manufactured and commissioned the bespoke package of deck machinery, together with the associated main and secondary hydraulic systems, now performing well on Virtuous.
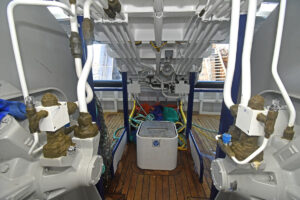
The 2 x 15t split net drums, supplied by EK Marine, are positioned either side…
The biggest difference compared to other recent new Scottish twin-rig prawn trawlers is the presence of three split trawl winches forward on the main deck. Following discussions with Eunan Kennedy, the owners opted for this arrangement in order to further enhance working safety and efficiency.
Of 15t core pull rating, the two-speed split trawl winches are spooled with 275 fathoms of 22mm-diameter fibre-core wire, supplied by Karl Thomsen of Buckie, plus 50 fathoms of 28mm backing wire.
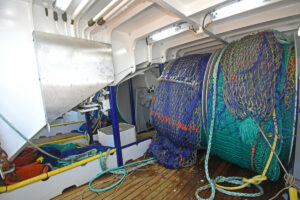
… of the stern ramp on the quarter.
The over-spooled wires have relatively shallow leads to hooded rollers incorporated into the shelterdeck slightly forward of the landing hatch.
The outer wires run across the top of the shelterdeck to a second set of sheaves positioned near the aft corners of the wheelhouse, from where they are directed upwards towards hanging blocks mounted on a conventional trawl gantry.
The middle wire runs slightly to starboard under the wheelhouse floor, before leading upwards to pass over a roller incorporated into the trawl gantry directly above a secure box for the safe storage of the middle roller. Set into the transom rail, this is centrally located directly above the stern ramp.
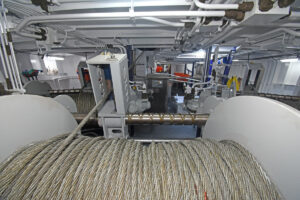
Looking aft over the top of the middle wire winch, positioned forward between the outer split winches.
Hardwearing UHMW-PE sheathing panels and strips, supplied by DockGuard, are secured to outer hull areas in line with where the trawl doors are worked, to minimise abrasion, wear and paint discolouration.
The split trawl winches are operated from a control panel built into the fishing console in the wheelhouse, from which the skippers have full sight of the trawl doors and clump coming up to the blocks.
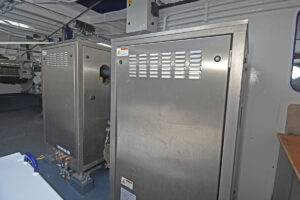
Ziegra supplied two TW1250 ice machines, which produce 1.25t of micro and 1.25t of midi flake ice per 24 hours.
When towing, the outer wires are chained up to a free-running slewing block on a short strop attached to swivel blocks mounted either side of the aft face of the trawl gantry – an arrangement commonly referred to as a ‘poor man’s autotrawl’. The middle wire is worked directly off the winch drum, enabling the skipper to adjust the length when required, depending on the spread of the gear being shown by the Simrad TV80 trawl-monitoring system.
All the necessary Flemings Fairleads hanging blocks and deck rollers were manufactured by F&R Belbin of Tynemouth.
Two sets of 2 x 15t split net drums are arranged side by side on the hardwood-decked quarter in line with the customary transom shooting and hauling hatches, the lower edges of which are fitted with large-diameter free-turning rollers.
In order to fit either side of the central stern ramp, the net drums feature larger-diameter flanges and slightly narrower cores. In turn, the wider than usual separation between the net drums provided the opportunity to use Staffa drive motors.
An EK Marine 1.5t @ 7m kinked-boom crane, fitted with a Thistle 24in W-sheave powerblock, is fitted atop the trawl gantry on the port side of the middle wire sheave.
The codends are taken up the stern ramp by a 7t Gilson winch mounted at the aft port corner of the hydraulically operated bag hatch, directly in line with a hanging block mounted on a stylishly raked and profiled gantry. Constructed as an integral part of the steel shelterdeck aft, and adjoining the aft end of the wheelhouse, this framework also houses the main and auxiliary engine exhaust trunking.
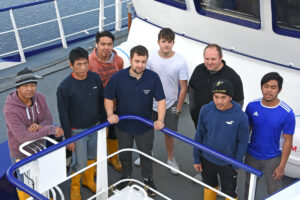
Virtuous skippers and crew, left to right: Jowel, Jolito, Ritchel, Alexander West, Aidan West, Sandy West, Marcello and Jerome.
After being released from the codend into a large-capacity hopper that runs across the boat from the centreline to the port side, catches are gravity-fed onto an elongated sorting table that extends forward. The crew immediately pick out the selections of whitefish and place them in a shoulder-height trough adjacent to the port side of the shelter behind their backs. This arrangement, which worked well on the previous Virtuous, enables the crew to focus on selecting and tailing prawns before gutting the various selections of fish, which are returned to the selection table after being allowed to pass back into the main reception hopper once it has been emptied.
Standing with their backs against the whitefish trough, the crew sort and gut the catch off the table. Selections are placed in elevated baskets, while prawn tails are directed into baskets on the deck via separate chutes.
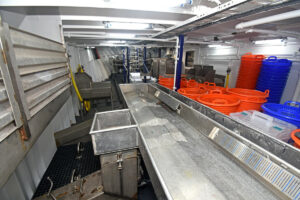
Looking forward along the sorting table.
Two prawn/whitefish washers are positioned against the deckhouse on the vessel’s centreline just forward of the sorting area. A third washer is located directly opposite to port. A rectangular prawn dip tank is positioned immediately forward of the twin washers. Spare baskets are securely stored against the side of the deck casing opposite the sorting table.
On being lowered by basket down to the fishroom, catches are weighed and labelled using a set of Marel M2200 marine packaging electronic labelling scales, from which the data is transferred to the wheelhouse, for subsequent reporting by the skipper using CatchLog electronic logbook software.
Capable of holding 590 stacker boxes in four tiers aft of the hatch, the fishroom has a working capacity of approximately 1,000 boxes. Six hundred boxes, supplied by Box Pool Solutions, are usually taken onboard at the start of a trip.
Up to 6t of flake ice can be stored in two full-height central lockers, positioned directly below two Ziegra TW1250 machines. Supplied and commissioned directly by Ziegra and housed in stainless steel cabinets on the main deck adjacent to the fore end of the deckhouse, the units produce 1.25t of micro and 1.25t of midi flake ice per 24 hours.
In order to ensure that catches are landed in optimum condition, Premier Refrigeration Ltd of Fraserburgh fitted chilling to both the forward and aft bulkheads, as well as to the deckhead.
The copper chilling pipes secured to the vertical bulkheads are protected by stainless steel sheeting. Stainless steel 22mm-diameter piping is mounted on the deckhead.
Automatically controlled from the wheelhouse and set to the required temperature by a digital thermostat, the cooling plant comprises a Bock compressor, an Azcue water pump driven by a three-phase electric motor and a Blitzer seawater condenser.
When landing, stacks of boxes are pulled towards the hatch by an electrically driven Bonfiglioli winch mounted on the underside of the shelterdeck. Catches are discharged from the fishroom using an EK Marine 1t @ 8m straight-boom crane fitted with a 1t landing winch. The landing and fishroom hatches are slightly offset to port, to complement the main deck layout.
Echomaster Marine wheelhouse electronics
Virtuous is equipped with a comprehensive array of mainly Simrad electronics equipment that was supplied, installed and commissioned by Echomaster Marine of Macduff.
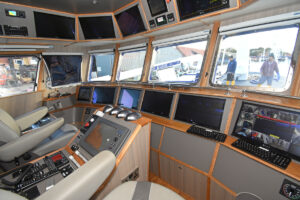
The wheelhouse electronics were supplied and commissioned by Echomaster Marine.
A combination of 17in, 22in and 24in Neovo X-Series flat screens are flush-mounted in the main and overhead forward consoles, and aft at the trawl console.
Another display screen is positioned at the central desk area in the wheelhouse for fish scales operation, e-log and weather forecasting, and general internet use.
Positioned across the full width of the wheelhouse and terminating in slim wing consoles housing engine and steering controls, the main console is arranged on a single level forward of two NorSap NS1500 skipper’s seats that flank a central island console.
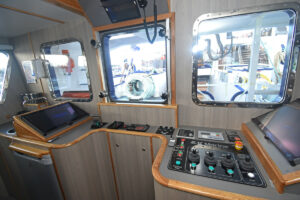
The central trawl console provides a clear view of activity across the transom.
The fishing console aft gives a commanding view of the doors and clump coming up, aided by comprehensive CCTV displays of activity on the quarter, forward at the split trawl winches and from the top of the aft mast.
Virtuous is equipped with a Simrad twin-rig double-distance net-monitoring system to provide optimum levels of fishing efficiency, in terms of both gear spread and fuel economy.
Information supplied by three Simrad PX sensors provides constant numerical and graphical updates of the middle clump’s position in relation to the trawl doors.
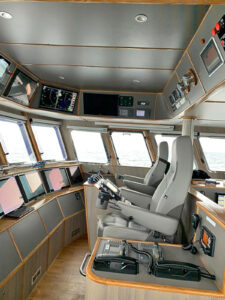
Two NorSap chairs flank a central console.
The door sensors provide twin net spread and pitch/roll measurement, while the clump sensor provides depth and water temperature measurement. An Airmar DT800 hull-mounted water temperature sensor is also fitted.
Details of Virtuous’ location and heading are processed by two JRC JLR-21 GPS compasses. Positioning data received is interfaced to three fishing and navigation plotters – an Olex 3D plotter, complete with ground discrimination, and two Sodena Easywin plotters – supporting a combination of Tide T8 charts, AIS and ARPA tracking.
Radar requirements are handled by two Simrad NSO Gen2 processors with Halo 4 and 6 antennas, the smaller of which is mounted on the foremast.
Vessel steering and navigation is taken care of by a Navitron NT777 digital autopilot complete with dual control heads, three jog levers and indicators.
Bottom sounding and fish detection onboard Virtuous is provided by a Simrad ES80 split-beam echosounder with 38kHz split-beam and 200kHz single-beam transducers.
Communications equipment includes two JRC JSS 2150 MF/HF DSC radio telephones, Sailor 6215 DSC and RT6210 VHFs, Icom IC-M506 VHF, Icom IC-GM1600E liferaft radio and JRC NCR333 Navtex.
Echomaster Marine also installed a comprehensive CCTV system deploying 14 cameras. An underwater hull camera covers the propeller, nozzle and rudder area.
Stern bagging proving effective
Skippers Sandy and Alexander West are delighted with how the new aft bagging arrangements are working on Virtuous.
Skipper Sandy West said: “Although adapting to the new working arrangements represented a considerable learning curve, we were helped by the fact that they worked smoothly from the off. The anticipated benefits were immediately apparent, and provided initial encouragement that we had made a sensible decision.
“There is no doubt that fishing efficiency and safety have been significantly enhanced. Without the need to come round on the gear, the process of hauling is now continuous. In turn, this has reduced the time taken to shoot and haul. Further time savings occur when moving grounds, as Virtuous can start steaming to the next selected position as soon as the gear is up, rather than having to lie until the codends are aboard, as was the case previously.”
In the past decade, an increasing number of skippers have moved towards taking catches aboard at the stern when ordering new vessels.
In the UK fleet, such arrangements are increasingly common on new pelagic and whitefish trawlers/seiners, having already become a standard feature on the smaller class of inshore trawler.
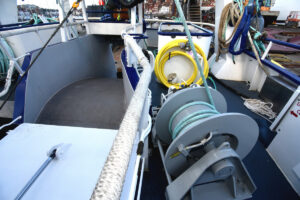
A 7t Gilson is mounted on the port side of the stern ramp atop the steel shelterdeck.
Bagging catches aft has long been a characteristic feature of French twin-rig trawlers. When a succession of these boats were sold to Ireland, their subsequent successful performance led to some Irish skippers ordering new boats built along similar lines.
However, while the concept of aft bagging is well-established, Virtuous advances the design evolution by retaining the net drums on a fully enclosed main deck, rather than moving them up to shelterdeck level – when, in some instances, catches are taken aboard on an open quarter.
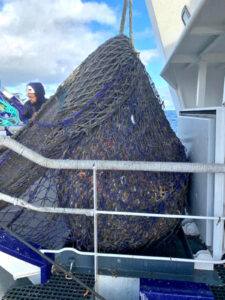
Preparing to release the contents of a codend through the reception hatch into the catch hopper.
Although the end result, which combines the well-established practice of working twin-rig trawls from an enclosed quarter with taking the codends aboard over the top of the net drums, looks deceptively simple now it is in place, numerous hours went into developing the initial concept into a practical working solution.
The key to realising the initial idea of having the hopper forward on the net drums was having the bag hatch on the centreline and the hopper running across the boat, to give good access aft – a concept that has not been seen before.
Fourth Virtuous over four generations
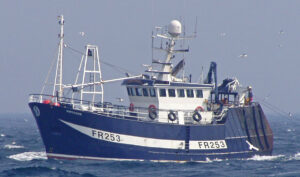
The first Virtuous FR 253 was built by Macduff Shipyards in 2000 as Amethyst BF 19, and renamed in 2003 when bought by skippers Sandy West and Keith Buchan.
By displaying the same name and registration as the owners’ previous boat, the new Virtuous continues a family tradition that now spans four generations, going back to when Sandy West’s paternal grandfather Alex, together with his brother Jimmy West, took delivery of the 32ft traditional Fraserburgh ripper yawl Virtuous FR 353, built by Tommy Summers in 1953.
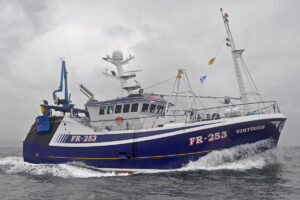
Built at Whitby in 2010, the 23.3m Virtuous FR 253 has recently been renamed Accord BCK 262 by Buckie skipper Michael Wilson.
Six years later, the same Fraserburgh boatbuilder delivered the 55ft Quiet Waters FR 253 to Sandy West’s maternal grandfather William Ritchie. The combination of name and number for the new Virtuous originates from these two boats.
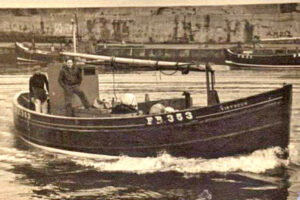
The ripper yole Virtuous FR 353 was built for Fraserburgh brothers Alex and Jimmy West at the Tommy Summers boatyard in 1953…
The family’s links with Tommy Summers’ boatyard were further strengthened towards the end of 1957 when Alex West took delivery of another traditional ripper yole, the 33ft Gracious FR 167, while his brother kept Virtuous. When Alex West retired, his son Zander, Sandy West’s father, took over as skipper of Gracious.
Sandy West’s fishing career started when he left school and became a crewman for five years aboard Fraserburgh skipper James Buchan’s seiner Renown FR 246, before joining skipper George Hepburn on the wooden- and steel-hulled Celestial Dawn BF 109 for 11 years.
In 2003, in partnership with Keith Buchan, he bought Amethyst BF 19 – built by Macduff Shipyards six months before her sistership, the new steel-hulled Celestial Dawn, entered service – from David West and Ralston Johnston.
Renamed Virtuous FR 253, this boat was sold to Brian Harvey and renamed Orion BF 423 in 2010 when the next 23.3m Virtuous was nearing completion at Whitby.
Sandy West’s 17-year-old son Alexander maintained his family’s fishing traditions by joining his dad on the new Virtuous, having previously spent a year at sea on her predecessor after leaving school.
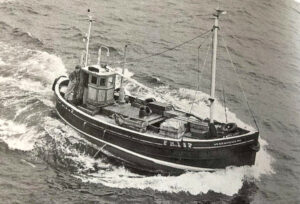
… four years before the same boatbuilder completed Gracious FR 167.
Nine years later, Alexander’s younger brother Aidan West is continuing this pattern as a crewman on the new Virtuous, a few months after embarking on a fishing career on her predecessor immediately after leaving school.
The 2010-built Virtuous was renamed Accord BCK 262 two months ago, after being bought by Buckie skipper Michael Alexander Wilson. Taking her new name and number from a 21m steel-hulled trawler that the family owned for 26 years, Accord replaces the 21.7m wooden-hulled twin-rig trawler Bonaventure BF 262. Bought from Eyemouth in 2016, this boat has now been renamed Elkanah BF 200 by new Gardenstown owners Kieran Reid and his father Michael.
Broch and Buckie twin-rig trawl gear
The twin-rig trawl gear now being used by Virtuous was supplied by Fraserburgh netmaker Andrew Whyte of Scotnet and Karl Thomsen of Buckie. This continues the owners’ longstanding association with both well-established companies.
The low-standing 195ft prawn scraper nets are rigged on 6in and 8in discs. When working on slightly harder bottom, a set of 155ft discer nets, set on 8in and 10in discs, come into play.
Both sets of twin-rig trawls are worked in conjunction with 60 fathoms of single 36mm four-strand combination warp, and six fathoms of doubles on 18mm wire next to the wing ends.
In addition to making up all the sweeps, chain connectors and pennants, Karl Thomsen also supplied three 275-fathom lengths of 22mm fibre-core trawl wire.
A set of Thyborøn Type 11 69in trawl doors and a 1,300kg roller clump, consisting of a series of freely rotating discs in an outer frame, manufactured by BNW Engineering of Fraserburgh, is used to spread the twin-rig prawn trawls.
When towing the prawn scraper and discer nets in 75-80 fathoms of water on the first three trips, the door spread was between 68 and 72 fathoms, with 200 fathoms of wire shot and the main engine running at 920-1,050rpm.