Several years ago I purchased an ice machine, a small Ziegra unit, and have never looked back. Generally landing to restaurants, prior to having an ice supply I had no other alternative than driving to the nearest fish market (25 miles away). It was not cost-effective. And I wasn’t going to suffer ‘£5/kg one day and £0.50p/kg the following day’, ‘should I risk the market?’ – the stark reality of the topsy-turvy world now smothering hand-line fishing.
Above: Alex Pino removing the auger from the geared electric motor.
That Ziegra machine was the best investment I ever made, however, I never really ‘took-a-spanner’ to it. No major service work was carried out, I just kept the machine like gold dust and thought everything was alright. However, putting maintenance on the backburner might have cost me dearly.
On a recent visit to the C Toms & Son boatyard, I spoke to Alex Pino of the South West refrigeration company, Alpino Services. Having fabricated and installed the Our Dylan Ben refrigeration system, together with fitting a Ziegra seawater ice machine, Alex had plenty to talk about; our chat later revealed my link to Ziegra.
Hearing of my machine’s service record – hardly any – I saw Alex raise his eyebrows, asking: “Is it running at the moment?” I answered, “No”, telling him that it is safely stored away and soon to be re-housed in a purpose-made shed. “Don’t do anything until I get there, don’t start it, let me have a look,” he added.
Having not realised that ice machines need new bearings as often as once a year, my lack of care may have simply written-off the majority of the £4,000 I paid for the machine seven years ago.
Ice making ‘physics’ is fairly simple; heat energy is required when a liquid changes to a gas, and that heat energy is drawn from whatever surface(s) that may be present nearby. But in practice you need to be in full control of the switching process between liquid-state and gaseous-state. A ‘refrigerant’ is a volatile fluid that, using pressure-change, can safely and repeatedly be converted between liquid and gas.
A refrigerant is used to rapidly chill one of the main components of an ice machine, a drum or cylinder, and water is sprayed onto the inner surface of that; ice immediately being formed.
The auger, an Archimedes screw, rotates around the inner surface of the cylinder and gently wipes-free the pieces of ice. The cycle continues and, in the case of my machine (and almost all small freshwater ice machines), ‘chip ice’ is formed.
Thankfully, since 2013 my Ziegra machine has been little used. After a knee injury some years ago, a deterioration over the past 18 months has put most of my serious fishing on hold, however, with a ‘new’ knee to be fitted in mid-January, I will (says the surgeon) be back fishing by next spring. So now is a perfect time to call in Alex Pino. I first met Alex many years ago, on trials of a new under-10m trawler, Jessica Grace, owned and skippered by Dave Thomas.
Before joining the Jessica Grace, Alex had crewed on several trawlers from Looe and Plymouth. Originally an engineer in the Merchant Navy, this is where his love of the refrigeration system was born. His remit was to look after the fridges on board the ship. On leaving the Merchant Navy, although fishing was his main aim, a few years later he decided to study and gain the relevant qualifications in both refrigeration and ice-making, with sole aim of working for the fishing industry; shortly afterwards, his business, Alpino Services, was born.
With camera at hand, I watched Alex unbolt the covers of my ice machine, and a brief explanation of its inner workings revealed that the best place for me, was to go and make the coffee!
He said, “You are very lucky that your machine is still working, you should be alright, but I can ‘never say never’, and I only hope you don’t need a new auger, because that is the most important part of any ice machine.”
He added, “Any refrigeration engineer who doesn’t learn something new every day is telling fibs, no two machines are the same, and in this instance this is the smallest Ziegra unit I have ever dealt with; the sort you might see at a fishmonger’s or at a restaurant, I normally deal with much bigger machines in fish holds. But let’s have a go.
“Basically all ice machines have the same parts, a compressor, a condenser – and in this case the condenser is air-cooled – and they are driven by a geared motor, an ice-freezing unit called the auger. There is an ice chute leading to the storage, and of course all the control circuitry and piping of the machine has to be easily accessible. All ice machines look similar, but your auger measures about eight inches high, with a diameter of about 3.5 inches – it is small. On big machines the augers are huge, and on many fishing boats I might be hanging from a deck-head to get spanners to it. Day after day, this job is never the same.”
I watched Alex uncouple the pipework and remove the auger (in order to check the bearings). I heard the ominous sound of ball bearings falling to the floor. “I think the bearing that has just fallen apart,” Alex said.
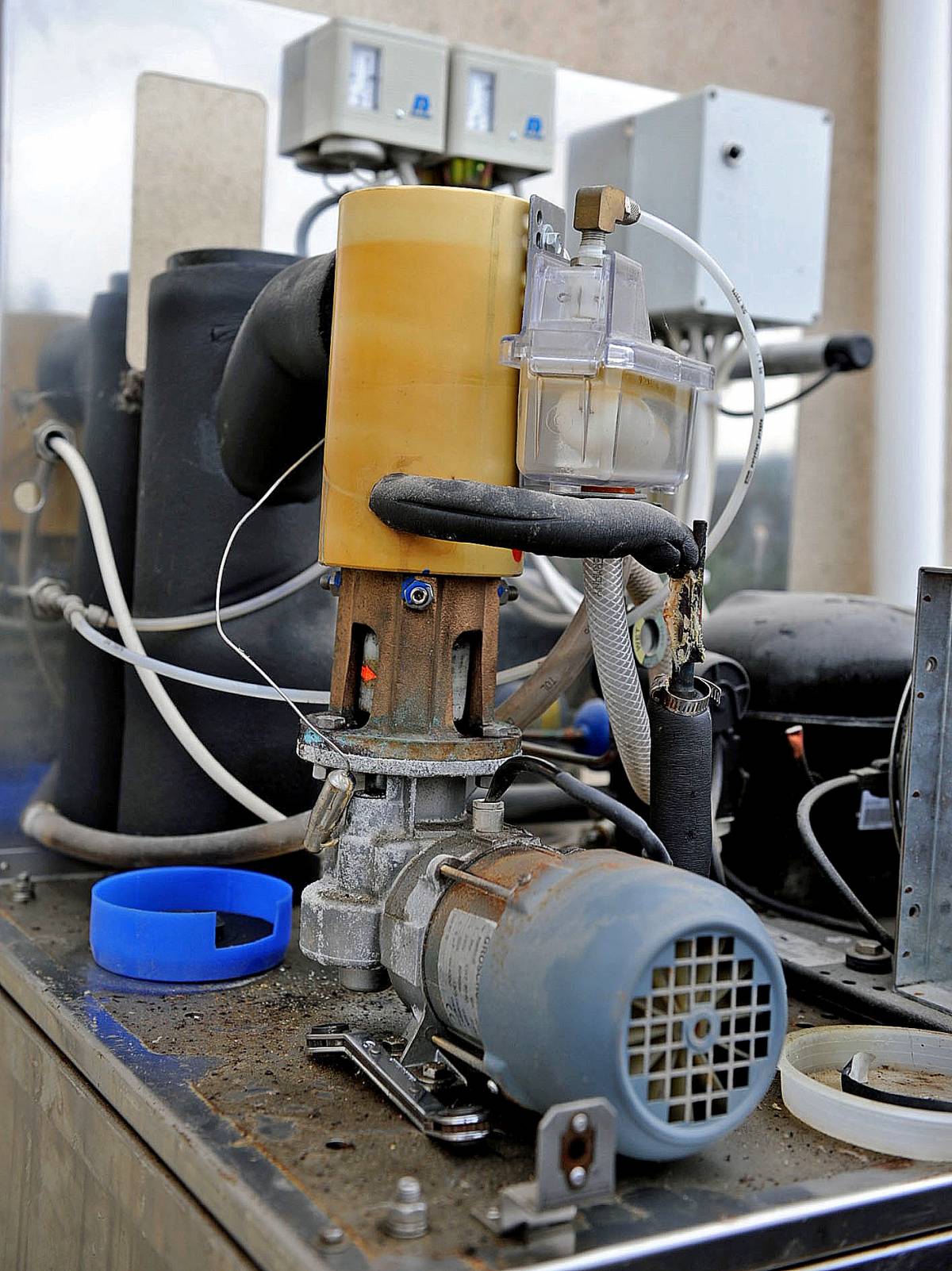
An ice machine should be serviced every year, I was told. This is a small/medium Ziegra machine – often used in restaurant/industrial situations. Ziegra products are top of the range and are not cheap. I cannot praise it enough, it has been a workhorse, and in my opinion, the best investment that any inshoreman could make.
“That is why you must never assume that if the ice-making machine is working, nothing needs doing, because it does. Those bearings should be replaced regularly. The auger might be working, but the tolerances inside are so precise that unless the axle is running true, damage is inevitable.”
On seeing what was left of the bearing, it was no surprise to hear Alex say, “I will have to take the auger back to the workshop and draw-out what’s left.
“Here we have the best-case scenario of a bearing failure, we hopefully caught it before it did too much damage. Before we began the service, the machine did make ice, and there was no water leakage. Normally, the first sign of a bearing failure is water leakage, because with the bearing gone, the water seals are not working. And, taking it one step further, the worst-case scenario is that the bearing shatters and the auger is no longer concentric – and the motor isn’t going to stop – so it may write-off the auger; a very expensive part to replace.”
So there we have it. Alex is soon to return and I can complete this tale. Hopefully I can relocate my Ziegra machine to its new shed before getting ready for my new knee-refit!
I must let you into this secret… I had a couple of specialised scans to get soundings of the damaged knee. I asked the surgeon what he used the information for, and he told me it’s sent over to Belgium. They make the knee there, ship it over here and he fits it. Apparently we don’t make knees! What will we do after the EU referendum? Swap sole quota with the Belgians for making false knees? A dozen beamers plundering the Trevose ground so that I can get a new knee? I’m going to have words with the CFPO and the NFFO about this…
Read more from Fishing News here.