Skipper Andrew ‘Watty’ Watt berthed the 18.8m Osprey WK 4 in its home port of Scrabster last weekend at the end of a 285-mile delivery passage from Whitby, just three weeks after the vivier-crabber was launched into the river Esk, reports David Linkie.
Designed by SC McAllister & Co, the fully shelterdecked Osprey was built by Parkol Marine Engineering for Andrew and Diane Watt and the family-based Holborn Fishing Company.
Taking delivery of a new build is a momentous milestone in the fishing career of any owner, when the initial adrenalin rush is accompanied by a full awareness of the challenges ahead associated with running a new boat.
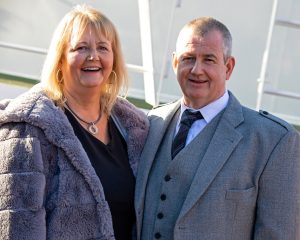
Diane and Andrew Watt of the family-based Holborn Fishing Company at Osprey’s naming ceremony on 6 March.
While unexpected bumps in the road are deeply ingrained in the fishing industry, the rapid rate of change experienced since Osprey was named at Whitby on 6 March is virtually unprecedented.
Neither the owners nor the 160 guests who attended the naming ceremony envisaged that within three weeks, the country would be in lockdown due to Covid-19. This situation immediately compounded the already complex task of completing surveys and paperwork, and obtaining the fishing licence, that is associated with every new vessel.
As this was the first new boat to run fishing trials and be handed over since the UK went into Covid-19 lockdown, owners and boatyard alike suddenly found themselves in uncharted waters.
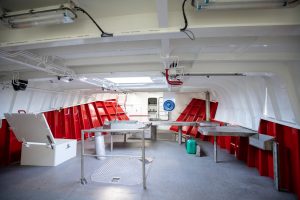
General view of working arrangements forward on Osprey’s main deck.
That Osprey was still able to run acceptance trials and leave Whitby for Scrabster via Fraserburgh highlights the unstinting level of effort that everyone associated with Osprey put in to make this possible.
When the current period of uncertainty comes to an end, Osprey will replace the owners’ previous 17m steel-hulled vivier-crabber Sparkling Line WK 43.
Andrew and Diane Watt signed the contract with Parkol Marine Engineering to build Osprey during the Aberdeen Expo in May 2018. Construction of the hull commenced 12 months later, with Osprey lifted into the water virtually finished at the beginning of last month.
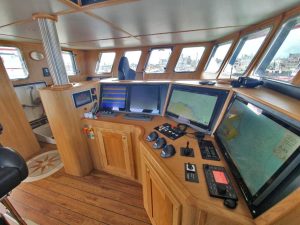
Osprey’s wheelhouse electronics were supplied by McMinn Marine of Fraserburgh.
While taking Osprey northwards, Andrew Watt said: “The frantic activity and frequent frustration of the past two weeks have been the complete opposite of the design and build programme, which progressed extremely smoothly.
“From the initial contact with Parkol Marine Engineering, they have been a real pleasure to work with. Whatever suggestions we put forward as Osprey took shape, they were delivered efficiently.
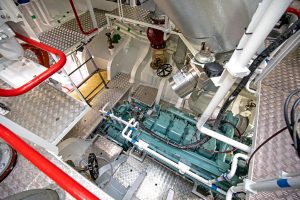
The Mitsubishi S6A3 main engine and Reintjes gearbox.
“We are delighted with the end result. The level of build, engineering and interior finish speaks for itself. Osprey will stand us in good stead in years to come – of that there is no doubt.
“While the present situation and all the uncertainty it brings is, of course, a huge concern both in the UK and globally, sight should not be lost of the fact that Osprey represents a long-term investment by Holborn Fishing Co, and one made primarily for the next generation.
“Like every other fisherman, challenges and downtimes have been consistent factors throughout my time at sea.
“That Osprey bears little or no resemblance to my first creel boat, the 24ft Stroma yawl Marigold, is a reminder that with time, as well as constant commitment and determination, problems can be overcome and long-terms goals achieved.
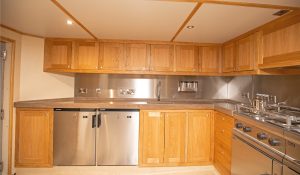
The well-equipped galley.
“Progression is seldom easy, and requires informed guidance and help. In this respect, I was extremely grateful to have my first experience of working on a vivier-crabber under the watchful eye of skipper Paul Simpson – ‘Smo’ – who tragically lost his life when Inconnu caught fire off Hoy in 1996. Paul was one of life’s true gentlemen, as well as a top crabbing skipper who always took time to share his invaluable experience. This contributed immeasurably to the new Osprey.”
Insured by Maritime Solutions (Dick Gregory), and with skippers Andrew Watt and Dave Brown sharing wheelhouse responsibilities, Osprey is expected to fish brown crab along the north coast of Scotland, west to the Butt of Lewis, on five- to six-day trips, before returning to Scrabster to land to MacNeil Shellfish Ltd. The owners’ son Ian, who has all necessary sea certificates including his under-16.5m skipper’s ticket, will be a crewman. Ian’s younger brother Danny will also join the crew when he leaves school in the next couple of years and gains the required new-entrant certificates.
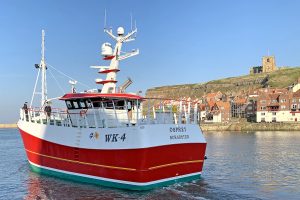
Osprey leaving Whitby…
Fishing down to 50-60 fathoms, Osprey works strings of 120 x 26in double soft-eyed D-section crab creels. Mainly manufactured by Caithness Creels in Wick, with the balance coming from Gael Force, the creels are spaced at 15-fathom intervals on Eurosteel heavy 14mm-diameter backropes supplied by Caithness Creels.
Caithness Creels’ MD John Sinclair has worked closely with Diane and Andrew Watt for a long time, during which an extremely strong working relationship based on mutual trust and professional respect has been built up.

… and crossing Thurso Bay before entering Scrabster harbour.
For the past 18 months, this has included a new brand of potting rope, Blue Viking, being trialled on Sparkling Line, as well as by a number of other potting skippers who have equally well-established ties with the Wick company.
Having been impressed by the performance of the appropriately blue-coloured Blue Viking backropes, which are available in 2mm increments from 10.5mm to 16.5mm diameter in both leaded and unleaded format, Holborn Fishing Company has ordered further supplies of 14.5mm- diameter Blue Viking rope for use on the new Osprey.
The Blue Viking potting ropes are the result of Caithness Creels working in liaison with an Indian company to develop a new product which John Sinclair describes as ‘a good rope at a good price’.
General layout
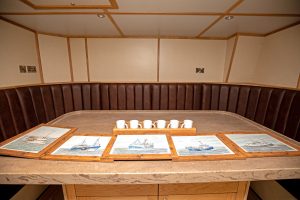
Sketches of Andrew Watt’s previous boats Marigold, Faith Ann, Osprey, Carina and Sparkling Line on the large mess table, prior to being mounted above the bench seating.
Designed by Ian Paton of SC McAllister, the main dimensions of Osprey are LOA 18.8m, registered length 16.45m, beam 7m, depth moulded 4.40m and GT 163t. Of double chine form, the steel hull incorporates a semi-bulbous bow, raked soft-nose stem and transom stern, the corners of which are well rounded to enhance manoeuvrability, both in harbour and when keeping station to the gear while hauling.
Below main deck level, the hull is arranged from forward into a large dry hold, the 32t vivier tank, the engineroom, and an eight-berth accommodation cabin split into two four-berth areas.
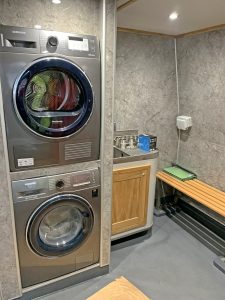
Laundry and tea/coffee-making facilities in the spacious deck wardrobe.
A frozen bait store is positioned on top of the vivier tank, on the port side of the central trunking leading to the vivier tank. The evaporator-based freezer unit was supplied and installed by Premier Refrigeration of Fraserburgh.
A Hercules Hydraulics 0.5t winch is mounted on the underside of the shelterdeck to assist with handling the cartons of frozen pot bait. After being removed from the freezer store, these are placed in a bait bin on the port side of the main deck to defrost ready for use.
The fully lined and insulated bait store will be used to store 20kg packs of frozen fish. These will be delivered by Enterfoods of Fraserburgh when the company is picking up fresh whitefish from trawlers coming into mainly Scrabster and Kinlochbervie.
A large insulated and lined dry hold extends into the equivalent space to starboard.
As the full-width deck casing is arranged across the transom stern under the full-length shelter, two-thirds of the vivier vessel’s main deck is clear of any obstructions, providing the maximum amount of deck space possible for working and storing static gear.
The working deck received specialist treatment from PBP Services of Fraserburgh, being coated with Degafloor hardwearing non-slip resins. The four-coat Degafloor resin compounds, in which quartz aggregate stays suspended in the top surface of the coating to give high-adhesion properties, are well proven to withstand the rigours associated with potting.
PBP Services also applied the glass-fibre coatings to the freezer and dry hold areas.
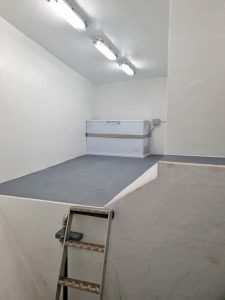
A raised section of the fully lined and insulated dry hold lies to starboard of the central trunking leading to the vivier tank.
A watertight door positioned to port of the vessel’s centreline gives access off the working deck to the full-width deck casing arranged across the transom. On coming off the deck, the crew enter a large heated oilskin changing and storage area that also includes a washing machine, tumble drier and tea/coffee-making facilities.
A central lobby area leads to a spacious shower/WC room to starboard, forward of a single-berth skipper’s cabin.
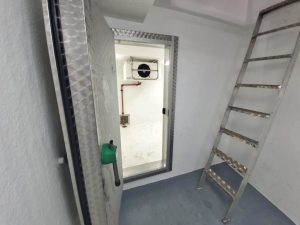
The port side bait freezer room…
The well-equipped galley is arranged fore and aft to starboard of the vessel’s centreline. The adjoining messdeck extends across the transom from the centreline to the port side.
Eight berths and generous locker storage provision are arranged in the main accommodation cabin down the aft stair, which is subdivided into two either side of the compartment housing the Wills Ridley steering gear.
Finished to a high standard using light-coloured natural oak, all the internal accommodation areas are warmed by electric convection heaters.
Potting arrangements
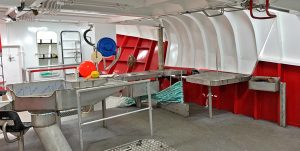
Pot strops layered on a toggle bar adjacent to the shooting table.
The carefully planned gear-handling arrangements, developed in line with the owners’ well-established crew and vessel safety management systems, include a gunwale rail self-hauling roller leading to an adjoining clearing table, positioned forward of a dedicated pot retoggling and shooting table and an anchor box.
Osprey’s pot-hauling and shooting stations are served by a single hatch raised and lowered by two hydraulic arms. When in the raised position, the hatch provides the skipper with a commanding view of hauling and shooting activity at all times from the Recaro helmsmen’s chair near the forward starboard corner of the wheelhouse.
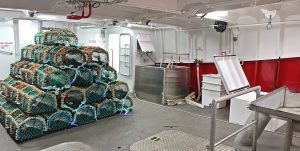
Preparing gear for Osprey’s first trip.
Osprey uses a 2t Britannia slave hauler for hauling her gear. The hauler is mounted on a hanging box mounted on the underside of the shelterdeck, fitted inboard of large-diameter stainless steel gunwale and forward vertical rollers, which guide creels onto the first of two stainless steel clearing and baiting tables.
The pivoted drop-down creel receiving table is separated from the inboard clearing and re-baiting table by a small parallel gap, allowing the backrope to be flaked into a large storage well recessed below the level of the main deck. Built into the deck structure, this arrangement significantly reduces the amount of rope lying on deck.
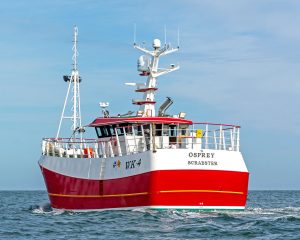
Osprey is expected to fish five- to six-day trips in line with market requirements when crabbing off the north coast of Scotland, west to the Butt of Lewis.
When emptying creels, undersized and white crab are returned to the seabed from the clearing table via an adjacent waste chute that leads straight down through the vessel’s forward dry hold before exiting the hull near the keel.
Selected brown crab are placed into a rubber-lined tray, from where they are nicked by a crewman sitting on the aft side of it, before being placed into a chute leading to the vivier hold.
Capable of holding 32t of shellfish and seawater in a 50/50 ratio, the vivier hold is served by one of two 6in Azcue pumps driven by 7.5kW electric motors that change the seawater every 12 minutes.
After being untoggled from the backrope, cleared and rebaited, creels are stacked four high in four tiers across the main deck amidships. When Osprey is running gear, the creels are placed on a shooting table aft of six toggle bars, from where the short legs are
reattached as the creels pass over the gunwale rail.
Engineroom
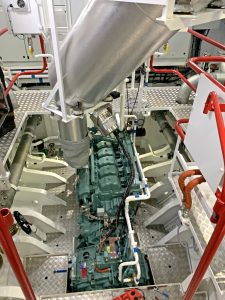
Supplied by Padmos, Osprey’s Mitsubishi S6A3 main engine develops 360kW @ 1,800rpm.
The Dutch company Padmos of Stellendam supplied and commissioned Osprey’s Mitsubishi S6A3 MPTAW main engine. Dedicated to propulsion duties, the main engine develops 360kW @ 1,800rpm and drives a 1,900mm-diameter fixed-pitch four-bladed open propeller through a Reintjes WAF 274 7.049:1 reduction gearbox.
This combination of centreline machinery enabled the crabber to record an average top speed of 9.5 knots on trials off Whitby.
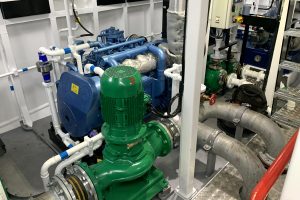
Twin 6in Azcue pumps, driven by 7.5kW electric motors run from Baudouin auxiliary engines and Leroy Somer generators, serve the 32t vivier hold.
As is customary with new Parkol boats, the propeller shaft and stern tube, which is fitted with Lips deepwater seals, were machined by Premier Engineering of Scarborough, together with a stainless steel cutting disc that will deal efficiently with any stray ropes that come into contact with the propeller.
Main electrical power on Osprey comes from two Baudouin 4W105S auxiliary engines driving 100kVA Leroy Somer 415/3/50 generators. The electrical distribution cabinets are arranged across the fore end of the engineroom.
Two electrically driven 35kW power packs supply hydraulic power for the deck machinery.
The skipper has full control of the electro-hydraulic system, together with the hauling/shooting hatch, from a console-mounted panel at the fishing position in the wheelhouse.
Pearson Electrical of Hull was subcontracted by Parkol Marine Engineering to undertake the electrical installation work on Osprey alongside the boatyard’s own electricians.
One Victron 100-amp charger is fitted to charge the two sets of batteries in the engineroom. A similar Victron charger is situated in the wheelhouse to serve the lighting batteries, in addition to a 50-amp GMDSS charger.
Cooling for all three engines and the hydraulic system is provided through NRF box coolers arranged across the aft end of the engineroom. Stainless steel CuNiFe piping is used extensively throughout the engineroom.
Port and starboard wing tanks in the engineroom carry 10,000 litres of fuel. A central tank positioned on top of the vivier hold between the aft side of the vivier trunking and the engineroom bulkhead houses 4,590 litres of freshwater.
Good teamwork overcomes challenges
Compiling this new boat feature was considerably more challenging than usual due to the measures imposed by the government to combat the Covid-19 pandemic.
Twenty-four hours before Osprey ran engine trials from Whitby, the first tranche of regulations were put in place, restricting personal travel. A few days later, when Osprey was carrying out fishing trials 18 hours before leaving Whitby, measures had been escalated to a virtual lockdown, and police were monitoring cars on the North York moors roads leading to Whitby, to prevent a recurrence of people travelling to the popular seaside town to walk their dogs on the beach, as had happened during a spell of fine weather over the previous weekend.
Text messages asking for help immediately produced a series of positive responses, followed by the photographs that made this feature possible.
Sincere thanks to everyone who helped so readily, despite the operational difficulties they themselves were facing.
High-spec surface coatings from PBP
PBP Services once again attended Parkol Marine Engineering’s premises to assist with the finishing surfaces on Osprey, which included fibreglass applications in the hold rooms and deck resin application to the working deck.
The PBP Services team arrived in Whitby with plant equipment and materials in order to apply fibreglass, resin and gel coats to the various refrigerated crab holding areas below deck, to leave a high-spec finish suitable for food storage areas. This also has the added benefit of achieving an easily cleaned hygienic surface, in order to enhance product quality.
Once this was completed, PBP applied Degafloor anti-slip deck resin to the working deck. PBP is the sole supplier of this specialist German resin product. The deck received a four-layer rapid-cure resin application, which is very visually pleasing, very hardwearing, and also comes with food and drink industry certification, anti-slip health and safety certification and Lloyd’s shipping class certification.
The experienced PBP team worked for seven days, night and day, in order to complete the work with minimum disruption to all other ongoing trades.
Hercules Hydraulics supplies bespoke system
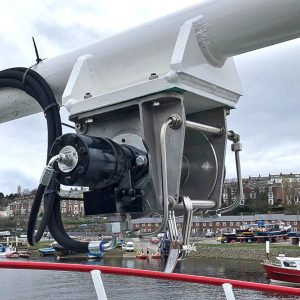
Hercules Hydraulics manufactured Osprey’s 1t landing winch…
The Paignton-based company Hercules Hydraulics designed and supplied Osprey’s bespoke hydraulic system using quality-brand hydraulic equipment.
As sole UK distributor for Marine TMA, Hercules Hydraulics also supplied the 0.5t bait lift winch mounted on the underside of the shelterdeck to assist with handling cartons of frozen pot bait.
Osprey’s hydraulic system comprises a twin load-sensing pump set up for full redundancy and efficiency, run off two 35kW three-phase motor units. This arrangement gives a very clean and compact set-up with no belts or clutches and, most importantly, minimal maintenance.
The system has high-spec inline filtration and cooling and incorporates load-sensing and fully proportional valves for safe and precise control of the equipment, including the heavy-duty 2t Britannia slave hauler, double ram-operated hauling/shooting hatch, Hercules 1t landing winch and 0.5t bait lift winch.
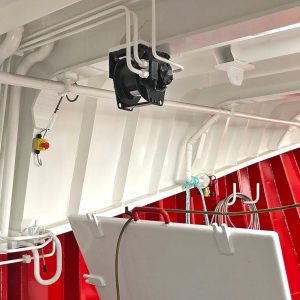
… and supplied a TMA 0.5t bait lift winch, mounted on the underside of the shelterdeck
Integrated safety e-stops and hydraulic system monitoring are built into the main hydraulic control panel for operational efficiency when the system is running, with all functions switch-operated.
The Britannia slave and main hatch are operated via push-button and joystick controls in the wheelhouse, along with additional local controls if required.
All other operations are locally operated near the equipment.
Osprey replaces Sparkling Line
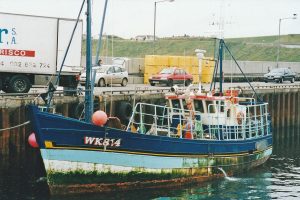
Faith Ann (ex George William C J 556) landing brown crab at Scrabster.
Osprey replaces Holborn Fishing Company’s previous vivier-crabber, Sparkling Line WK 4, which was re-registered WK 43 as her successor was nearing completion at Whitby.
Sparkling Line PW 3 moved to Caithness from Cornwall in 2015 after gill-netting from Newlyn for four years.
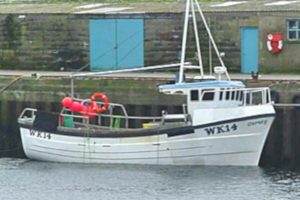
The first Osprey was a Kingfisher 33 vivier-crabber built at Macduff by Seaway Marine.
The 17m steel-hulled Sparkling Line – originally registered GY 36 – was built at Macduff Shipyards Ltd in 1989 as an advanced longliner for the well-known Grimsby skipper John Hancock.
After performing consistently well when lining for mainly dogfish in the North Sea and off the west coast of Scotland, the 228kW Gardner-engined boat left Humberside in 1996 after being bought by Colin Garriock of Stenness, Orkney, when Sparkling Line was re-registered K 364.
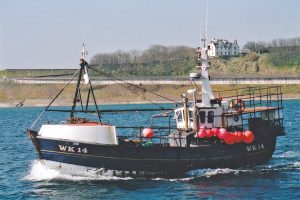
The French-built Osprey (ex Edward Harvey PZ 242).
The following year, Iain MacAulay of Great Bernera took Sparkling Line to the Isle of Lewis. Iain MacAulay sold Sparkling Line to Iceland in 2000, where the boat was renamed Eyrun AR 66 by owner Erlingur Jonsson.
Seven years later, Robin and Andrew Grantham of Chichester brought the vessel back to the UK to work as a potter from Portsmouth, when the boat was renamed Sparkling Line GY 364.
Sparkling Line moved along the south coast of England to Newlyn in 2011 after being bought by Waterdance Ltd and converted to netting by Macduff Shipyards.
Osprey is skipper Andrew Watt’s fifth vivier-crabber. The first, bought to replace the Stroma yawl Marigold, was the former Jersey-based George William C J 556. Built by Chantier Sibiril at Carantec, Brittany in 1978, this 17.5m vessel was renamed Faith Ann WK 814 on arrival at Scrabster.
After buying the almost new Kingfisher 33 Osprey as an additional vivier-crabber from Fraserburgh, Andrew Watt replaced the Kingfisher 33 by purchasing the former Newlyn-owned 14m vivier-crabber Edward Harvey PZ 242, which was renamed Osprey WK 14.
The fourth vivier-crabber, Sparkling Line PW 3, was bought in 2015 as a replacement for the wooden-hulled Osprey, which was lost off Cape Wrath in July 2014.
McMinn Marine wheelhouse electronics equipment
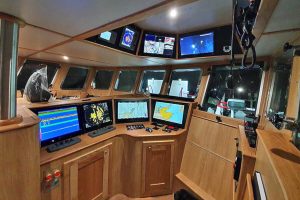
Supplied by McMinn Marine, the wheelhouse electronics equipment…
Osprey’s electronic wheelhouse equipment was supplied, installed and commissioned by brothers David and Kevin McMinn from the Fraserburgh-based company McMinn Marine Ltd.
In terms of both general layout and high quality of finish, the wheelhouse interior epitomises the attention to detail that is evident throughout Osprey, which is a credit to the owners and builders alike.
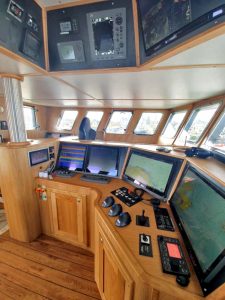
… is grouped together around the helmsman’s position.
The skilled use of solid oak facings and matching light-coloured laminates, co-ordinated with contrasting horizontal surfaces and radiused corners, combine to create a modern appearance, in which all available space is fully used.
Osprey’s wheelhouse provides skippers Andrew Watt and Dave Brown with a commanding view of hauling and shooting operations on the main deck from the deck track-mounted Recaro helmsman’s chair positioned in the forward starboard corner. Electronic controls for the Britannia hauler are conveniently located to the right of the skipper’s seat, as are the Kobelt engine controls.
Crown Marine Seats also supplied a second Recaro chair located to port, forward of hot drink-making facilities and a desk area with a laptop.
AG Neovo screens (22in and 19in) displaying information from the plotters, main radar and sounders are flush-mounted in the main console to port of the skipper’s chairs. Screens displaying images from the vessel’s CCTV system and secondary equipment are arranged in the overhead console.
Data on Osprey’s positioning is supplied by a JRC JLR-7600 GPS receiver and a JRC JLR-21 GPS compass, displayed on Olex 3D dual-screen seabed mapping and Sodena Turbowin plotting systems. Additional screen displays for the Sodena plotter are also provided in the messdeck and the skipper’s cabin.
In addition to the usual AIS and tidal provision, the Olex plotter also displays ground hardness discrimination from the input provided by a JRC JFC-130 single-frequency (50kHz) BB colour sounder.
Steering and navigation is taken care of by a Navitron NT777 digital autopilot. JRC JMA-5312 (12kW) and JRC JMA-3300 (4kW) radars with AIS and ARPA interfaces are also fitted.
Communications and safety equipment includes Icom M323 and M506 DSC VHFs, Entel HF649 GMDSS handheld VHF, Emtrak Class A AIS, Phontek talkback, X21 V-Sat and Intellian i4 satellite TV system.
McMinn Marine also installed Osprey’s eight-way CCTV system, from which eight cameras provide constant coverage of the engineroom, propeller and working deck.
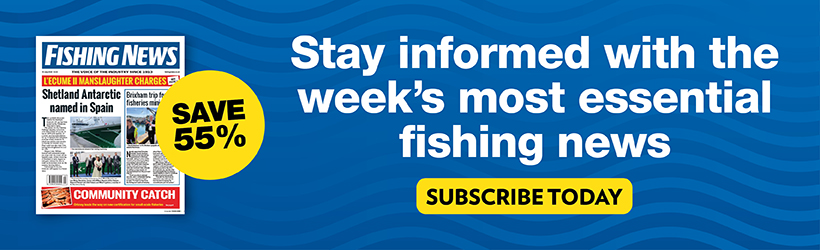
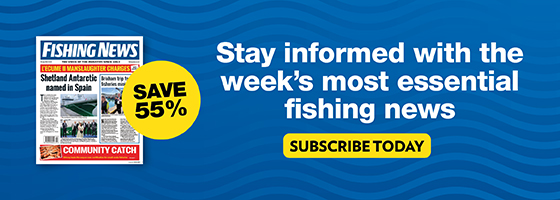