“I enjoy the fact that with my role it’s all different. Nothing is ever the same. There are always different challenges,” Matthew Langham (pictured above, right) technical director at marine navigation equipment specialist Mantsbrite, told Fishing News.
“Since I was young, I’ve always been interested in electronics and the hardware side of how things work.
“I joined the army cadets and was taught how to use amateur radio and other bits and pieces. I then went off to college, followed by university – where I studied for an engineering degree specialising in electronics.”
Shortly after graduating, Matthew spotted an opportunity with Essex-based Mantsbrite, which distributes a wide range of marine electronic and navigation equipment, as well as providing installation and support services.
“I didn’t have all the experience necessary for the role, but I thought I would apply anyway and see how it went.
“I came for an interview and explained that I understood I couldn’t earn the full amount of money stipulated in the advert as I didn’t have any experience. So I said I’d happily start at a lower salary and work my way up – and I got the job.”
Thirteen years on, and Matthew has progressed to technical director – a position he has been in for the last five years. “I wear many hats in this role, and there’s quite a lot to it. I do a range of different things – that could be technical drawings for various new builds and other vessels which we provide the equipment for, or providing support for the equipment we distribute.”
The diversity of his role makes a ‘typical day’ for Matthew something of a rarity, and when it comes to installations, he could find himself in any part of the country.
“Generally, the process begins with a customer or client calling or emailing us. We’ll then discuss what their requirements are, what equipment they already have aboard and what they’re looking for. We’ll then provide a quotation, and if they wish, we can also install the equipment for them.
“For example, I recently carried out a radar install in Wells-next-the-Sea. I loaded the gear and my tools into the van the night before, and was up at 5am the next day to drive to Wells-next-the-Sea to meet the customer – Ben Gathercole, skipper of Blucher LN 8.
“I had a look onboard to get an understanding of cable runs. I then took the old equipment off, and installed the new. Following that, I set the system up, and explained how it all works and made sure Ben understood everything and was happy.
“Some installs can take a day to a day and a half, but because the fishing vessel was quite small and there was an existing system already in place, it was finished in about half a day.”
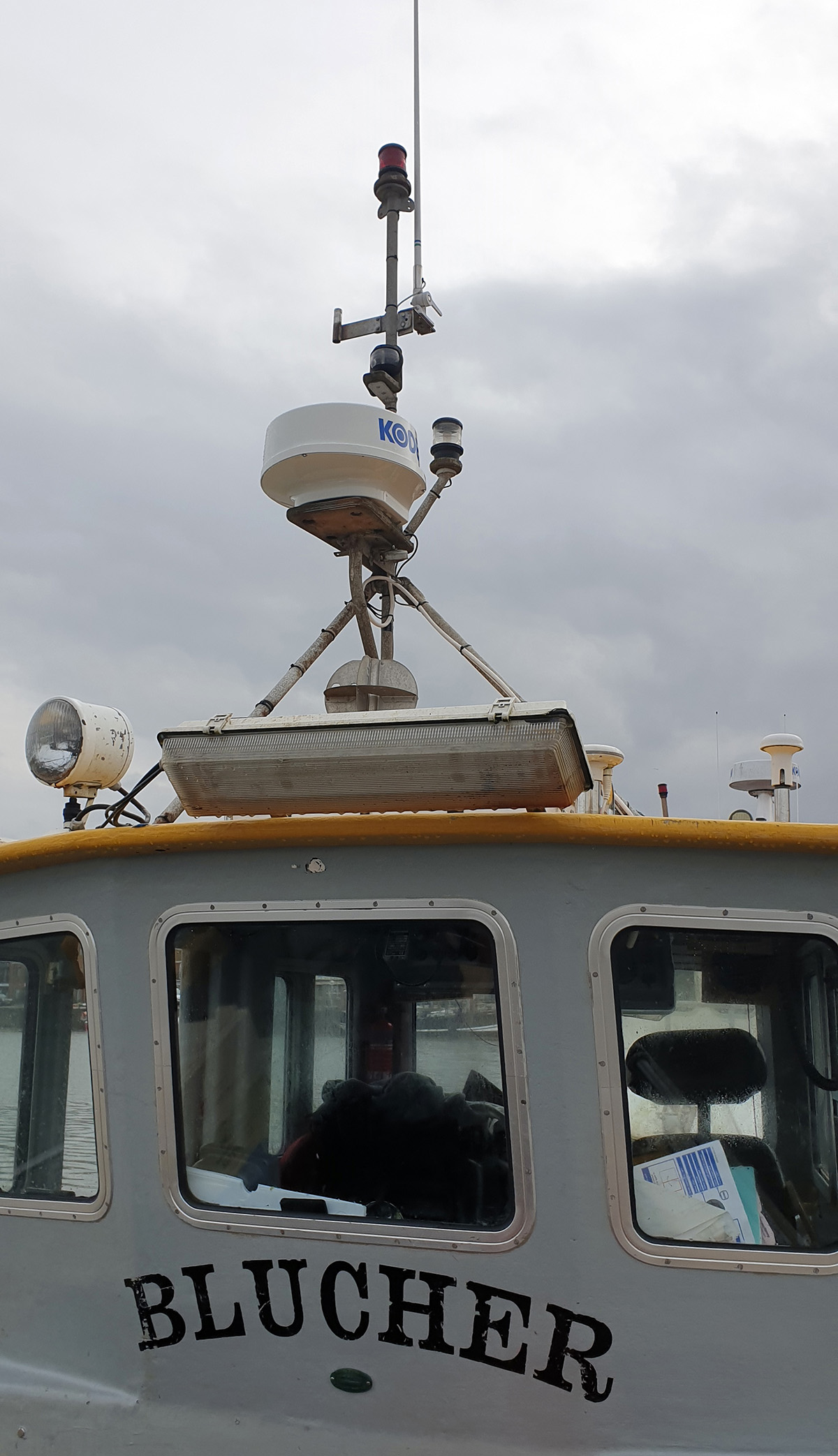
The radar installation on Blucher took Matthew around half a day. “What you tend to find on fishing vessels is that they try and keep the equipment working themselves. Generally, when they can’t get it working, that’s when they call us.”
Matthew’s role also sees him provide varying levels of support across the country. “We offer a range of support to our customers. We’re also UK distributor of the Koden equipment – which I provide technical support for.
“For some customers, we also provide support for their maintenance agreements – and I do their surveys as part of that. For example, last year after we exhibited at the Skipper Expo in Aberdeen, I had to drive to different vessels to conduct their surveys. I travelled to Mostyn, North Wales, then to Liverpool, on to Barrow-in-Furness, then Grimsby and down to Great Yarmouth – and then drove back home.
“I’ve also had it where I’ve received a phone call from David Ash, our managing director, saying there’s an issue on a boat in Liverpool.
“So I drove up there the next day. The vessel came in at 6pm, and I was working on it until 1.30am. It was quite a surprise seeing some of the nightlife in Liverpool at that time of the morning when trying to find food!”
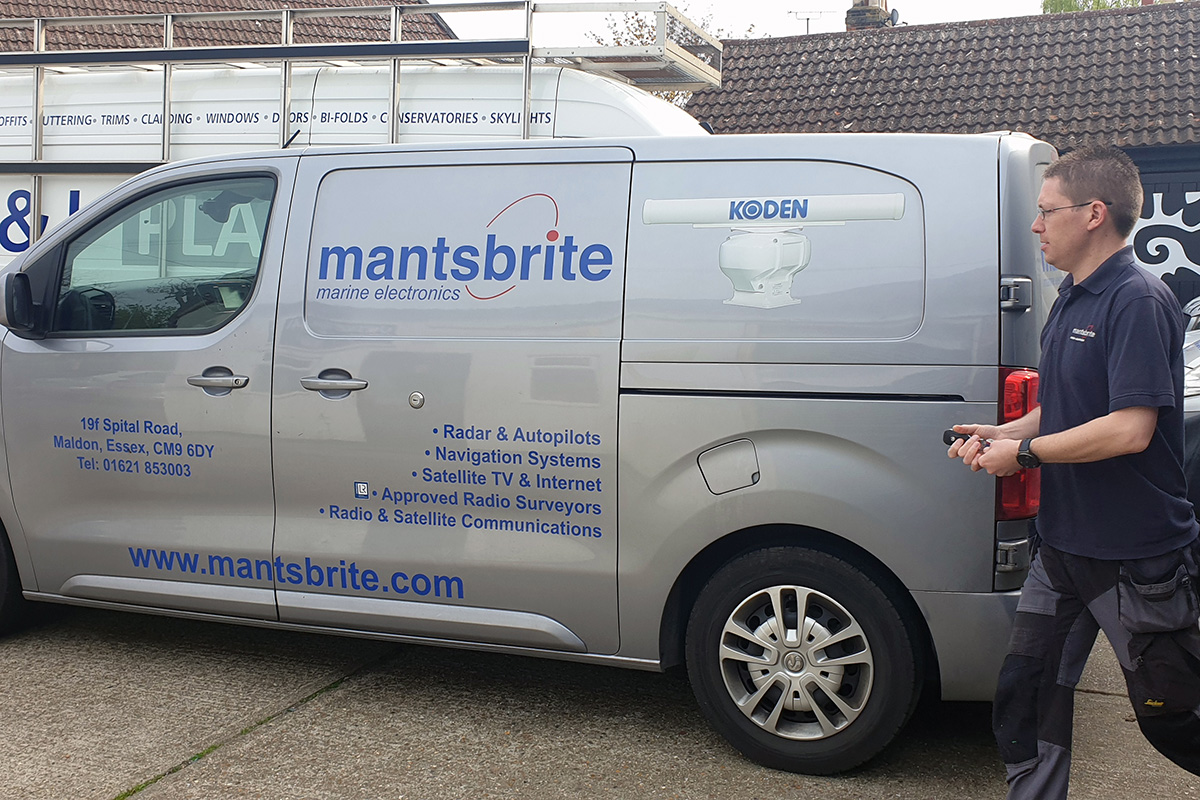
Matthew preparing to hit the road. “There are days when you’re in Grimsby or somewhere and its 6am or 7am and you have that lovely view of the docks and the water – it’s just nice to get out and about sometimes.”
When he’s not on the road, Matthew catches up with a wide range of administrative tasks back at the office. “With the equipment we need to keep up to date with the latest regulations. We’re also putting quotes together, and then there’s the paperwork for other things – such as forthcoming installations.
“In a way, fishing vessels are the same as any other vessels – but of course, each boat has its quirks. I’ve worked quite a lot recently with Fastline Shellfish, working on the refits for most of their vessels.
“When I was doing those refits, I used wire diagrams – where I work out all of the equipment and how it interfaces, and also work out the current loads. You then have to label the wires – so you have traceability and can follow it from start to finish.”
However, Matthew is always happy to leave his desk should the need arise. “With fishermen we know it’s their livelihood – so the commercial guys tend to take priority. If they call you up, then there’s an issue and they need it fixing.
“Fishermen know we’ll get it sorted, and it’s done – and they don’t have to worry about it again.”
This story was taken from the latest issue of Fishing News. For more up-to-date and in-depth reports on the UK and Irish commercial fishing sector, subscribe to Fishing News here or buy the latest single issue for just £3.30 here.
Sign up to Fishing News’ FREE e-newsletter here.
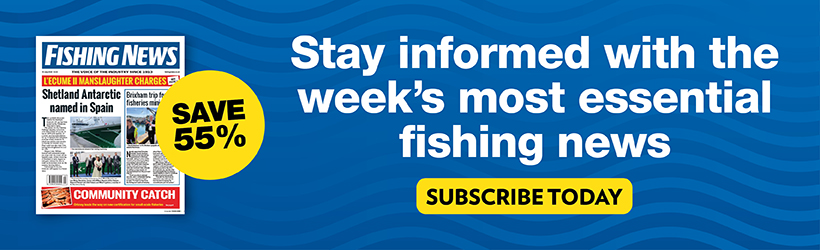
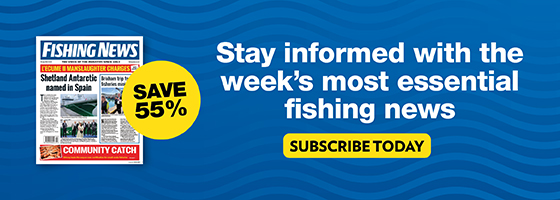